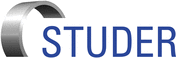
Group: UNITED GRINDING Group

Catalog excerpts
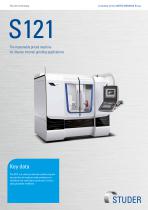
S121 The reasonably priced machine for diverse internal grinding applications. Key data The S121 is a universal internal cylindrical grinding machine for medium-sized workpieces in individual and small batch production. It has a swing diameter of 400 mm. A member of the UNITED GRINDING Group
Open the catalog to page 1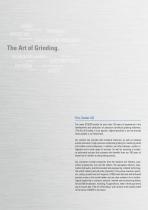
TECHNOLOGY LEADER CUSTOMER FOCUS SOPHISTICATED PROCESSES The Art of Grinding. TECHNOLOGY LEADER EFFICIENCY PRECISION GLOBAL CUSTOMER FOCUS SOPHISTICATED PROCESSES Fritz Studer AG The name STUDER stands for more than 100 years of experience in the development and production of precision cylindrical grinding machines. «The Art of Grinding.» is our passion, highest precision is our aim and top Swiss quality is our benchmark. Our product line includes both standard machines, as well as complex system solutions in high-precision cylindrical grinding for machining small and medium-sized...
Open the catalog to page 2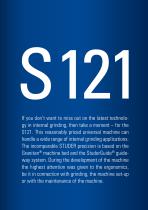
S121 If you don’t want to miss out on the latest technology in internal grinding, then take a moment – for the S121. This reasonably priced universal machine can handle a wide range of internal grinding applications. The incomparable STUDER precision is based on the Granitan® machine bed and the StuderGuide® guideway system. During the development of the machine the highest attention was given to the ergonomics, be it in connection with grinding, the machine set-up or with the maintenance of the machi
Open the catalog to page 3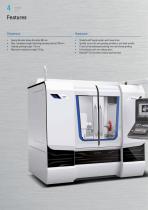
Dimension • Swing diameter above the table 400 mm • Max. workpiece length (including clamping device) 300 mm • Internal grinding length 175 mm • Maximum workpiece weight 125 kg • StuderGuide® guide system with linear drive • Spindle turret with two grinding spindles or one fixed spindle • C-axis for the workhead enabling form and thread grinding • Full enclosure with two sliding doors • Granitan® S103 mineral casting machine base
Open the catalog to page 4
Very simple operation and programming thanks to StuderWIN Short setup and resetting times e.g. with Studer Quick-Set Standardized interfaces for loader and peripheral devices The S121 universal internal cylindrical grinding machine has an exceptional price/performance ratio and is the ideal machine for internal, surface and external grinding of chuck components. It has a host of sophisticated technical features such as the revolutionary StuderGuide® guideway system, high-precision axis drives with linear motors, a swivel-in dressing unit, etc. The S121 is the ideal machine for a wide range...
Open the catalog to page 5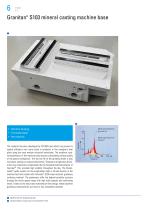
Granitan® S103 mineral casting machine base 1 • Vibration damping Machine bed made from gray cast iron • Thermally stable • Non-wearing 1 Machine bed with longitudinal guides 2 Vibration behavior of gray cast iron and Granitan® S103 The material structure developed by STUDER and which has proved its superb efficiency over many years is produced in the company›s own plant using the most modern industrial techniques. The excellent cushioning behavior of the machine base ensures outstanding surface quality of the ground workpieces. The service life of the grinding wheel is also increased,...
Open the catalog to page 6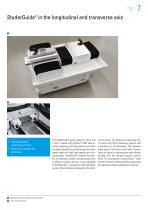
StuderGuide® in the longitudinal and transverse axis 1 • High geometrical traversing accuracy • Effective covering of the guideways 1 Machine base with longitudinal and cross slides 2 Z-axis with linear motor The StuderGuide® guide system for the X and Z axis is coated with Granitan® S200 wear-resistant guideway surfacing material and offers the highest possible accuracy through the entire speed range with high load capacity and cushioning levels. StuderGuide® extends the benefits of hydrostatic systems and guideways with a patented surface structure. A big advantage of StuderGuide® in...
Open the catalog to page 7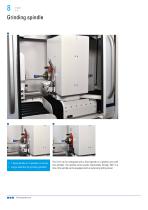
• 1 fixed spindle or 2 spindles on turret • Large selection of grinding spindles 1 2 3 Grinding spindle turret The S121 can be configured with a fixed spindle or a spindle turret with two spindles. The spindle turret swivels hydraulically through 180° to a stop. One spindle can be equipped with an external grinding whee
Open the catalog to page 8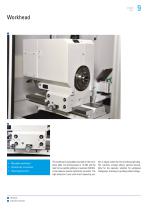
• Movable workhead • Cylindricity correction • Good ergonomics 1 Workhead 2 Cylindricity correction The workhead is adjustably mounted on the workpiece table. The driving power is 1.6 kW, and the load for live spindle grinding is maximum 300 Nm. It also features manual cylindricity correction. The high-resolution C-axis with direct measuring sys- tem is ideally suited for form and thread grinding. The machine concept allows optimal accessibility for the operator, whether for workpiece changeover, dressing or grinding wheel chan
Open the catalog to page 9
• Configurable according to client›s requirements • Rotating or stationary dressing tools can be used 1 2 Swivel-in dressing units 3 Dressing with rotating dressing tool An easy-cutting grinding wheel is essential for cost-effective and high-quality grinding. Rotating and fixed dressing tools can be mounted on the pivoting dressing unit. This makes it possible to coordinate the dressing process flexibly and optimally with the characteristics specific to the workpiece, tool or materials. The grinding wheel profile and dressing parameters are easily de- fined via macros. Another STUDER...
Open the catalog to page 10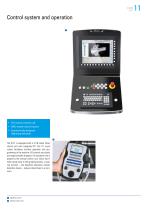
Control system and operation 1 • PCU manual control unit • EMC-tested control cabinet • Ergonomically designed Operating elements 2 The S121 is equipped with a 31i-B series Fanuc control unit with integrated PC. The 15" touch screen facilitates intuitive operation and programming of the machine. All controls are clearly and ergonomically arranged. An important role is played by the manual control unit, which facilitates setup close to the grinding process. A special function – the Sensitron electronic contact detection device – reduces downtimes to a minimum. 1 Machine control 2 Manual...
Open the catalog to page 11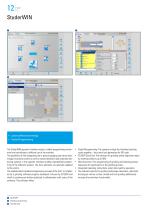
• Latest software technology • StuderPictogramming The StuderWIN operator interface creates a stable programming environment and contributes to efficient use of the machine. The possibility of fully integrating the in-process gauging and sensor technology for process control as well as contact detection and automatic balancing systems in the operator interface enables standardized programming of the different systems. The drive elements are optimally adapted to the control. The sophisticated mechanical engineering concept of the S141 is completed by a grinding software program developed...
Open the catalog to page 12All STUDER catalogs and technical brochures
-
ecoLoad
2 Pages
-
roboLoad
2 Pages
-
insertLoad
2 Pages
-
S33
13 Pages
-
easyload
2 Pages
-
favoritCNC
11 Pages
-
smartLoad
2 Pages
-
favorit
13 Pages
-
S30
9 Pages
-
S121 / S131 / S141 Radius
15 Pages
-
Customer Care STUDER
7 Pages
-
S100
11 Pages
-
Customer Care UGG
13 Pages
-
uniLoad
2 Pages
-
S36
21 Pages
-
Synchronous tailstock
2 Pages
-
roboLoad
2 Pages
-
S31
24 Pages
-
Software
20 Pages
-
S41
28 Pages
-
WireDress®
4 Pages
-
S20
16 Pages
-
S11
20 Pages
-
LaserControl™
2 Pages
-
StuderControl
4 Pages
-
Product Range
16 Pages
-
A Axis
2 Pages
-
S122
4 Pages
-
S121 / S131 / S141
20 Pages
-
S131 / S141 / S151
24 Pages
-
S22
20 Pages
-
S110 / S120
20 Pages