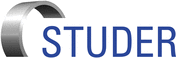
Group: UNITED GRINDING Group

Catalog excerpts
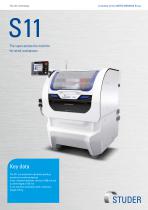
S11 The super-productive machine for small workpieces. Key data The S11 is a production cylindrical grinding machine for small workpieces. It has a distance between centres of 200 mm and a centre height of 125 mm. It can machine workpieces with a maximum weight of 3 kg. A member of the UNITED GRINDING Group
Open the catalog to page 1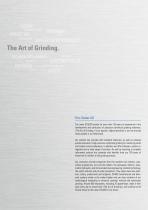
TECHNOLOGY LEADER CUSTOMER FOCUS SOPHISTICATED PROCESSES The Art of Grinding. TECHNOLOGY LEADER EFFICIENCY PRECISION GLOBAL CUSTOMER FOCUS SOPHISTICATED PROCESSES Fritz Studer AG The name STUDER stands for more than 100 years of experience in the development and production of precision cylindrical grinding machines. «The Art of Grinding.» is our passion, highest precision is our aim and top Swiss quality is our benchmark. Our product line includes both standard machines, as well as complex system solutions in high-precision cylindrical grinding for machining small and medium-sized...
Open the catalog to page 2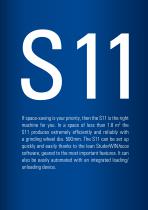
S11 If space-saving is your priority, then the S11 is the right machine for you. In a space of less than 1.8 m2 the S11 produces extremely efficiently and reliably with a grinding wheel dia. 500 mm. The S11 can be set up quickly and easily thanks to the lean StuderWINfocus software, geared to the most important features. It can also be easily automated with an integrated loading/ unloading device.
Open the catalog to page 3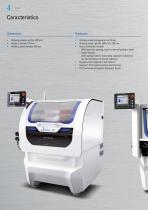
Caracteristics Dimensions • Distance between centres 200 mm • Grinding wheel arrangement 0 or 20 deg • Grinding wheel right dia. 500 x 63 x 203 mm • Grinding wheel diameter 500 mm • wo full enclosure variants T - With large door opening, ideal for manual loading or small loader systems - With loading hatch for top loading, especially suitable for the interconnection of several machines • axis cover (telescopic and bellows) Dual • Granitan® S103 mineral casting machine base • touchscreen (Projective Capac
Open the catalog to page 4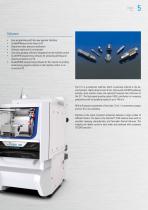
Software • programming with the new operator interface Easy • StuderWINfocus on the Fanuc 0i-TF • Simple and clear process visualization • Software optimized for touchscreen • In-process gauging software integrated into the machine control • StuderWIN programming software for producing grinding and dressing programs on a PC • StuderGRIND programming software for the creation of grinding and dressing programs directly on the machine control, or on an external PC The S11 is a production machine, which is precisely tailored to the desired process. Highly dynamic axis drives, high-quality...
Open the catalog to page 5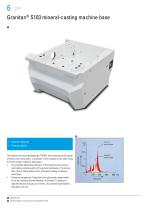
Granitan® S103 mineral-casting machine base 1 Cast iron machine base • Thermal stability 1 Machine base 2 Vibration behavior of gray cast iron and Granitan® S103 Granitan® machine base The material structure developed by STUDER, which has proved its superb efficiency over many years, is produced in the company’s own plant using the most modern industrial techniques. • The excellent dampening behavior of the machine base ensures outstanding surface quality of the ground workpieces. The service life of the grinding wheel is also increased, leading to reduced downtimes. • Temporary temperature...
Open the catalog to page 6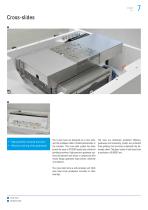
• High geometric traverse precision • Effective covering of the guideways The X and Z-axis are designed as a cross slide, and the workpiece table is bolted permanently to the machine. This cross-slide system has been proven for years in STUDER production cylindrical grinding machines. High-precision guideway systems and dynamic axis drives in conjunction with robust design guarantee high process reliability in production. The cross slide forms a self-contained unit. Both axes have linear guideways mounted on roller bearings. 1 Cross-slides 2 Workpiece table The axes are effectively...
Open the catalog to page 7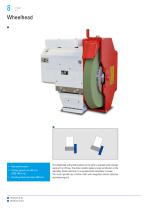
• High performance • Cutting speed up to 63 m /s (HSG 140 m / s) • Grinding wheel diameter 500 mm 1 Wheelhead 20 deg 2 Wheelhead variants The wheelhead with grinding wheel on the right is available with a plunge angle of 0 or 20 deg. The motor spindle makes a large contribution to the legendary Studer precision. It is manufactured completely in-house. The motor spindle has a hollow shaft with integrated contact detection and balanc
Open the catalog to page 8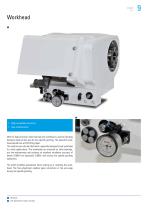
• High roundness accuracy • Low-maintenance With its high-precision roller bearings the workhead is used for grinding between fixed centres and for live spindle grinding. The powerful workhead spindle has a MT4 fitting taper. The machine can also be fitted with a specially designed chuck workhead for chuck applications. The workheads are mounted on roller bearings, are low-maintenance and possess an excellent roundness accuracy of below 0.0004 mm (optionally 0.0002 mm) during live spindle grinding operations. The airlift simplifies adjustment when setting up or resetting the workhead. The...
Open the catalog to page 9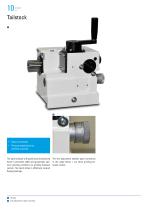
• Taper corrections • Thermal stabilization via overflow capacity The rigid tailstock with generously dimensioned The fine adjustment enables taper corrections barrel is extremely stable and guarantees opti- in the range below 1 µm when grinding bemum grinding conditions for grinding between tween centers. centres. The barrel slides in effectively covered floating bearings. 1 Tailstock 2 Fine-adjustment for taper correctio
Open the catalog to page 10
An easy-cutting grinding wheel is essential for cost- effective, high-quality grinding. In order to create a flexible and optimal dressing process that coordinates with the properties of the workpiece, tool and materials, STUDER provides a large selection of dressing units. The grinding wheel profile and dressing parameters are easily defined via macros. Another STUDER speciality is the grinding wheel reference points (T-numbers). This enables programming with normal dimensions, which considerably facilitates the development of grinding programs. A software package is available to fine tune...
Open the catalog to page 11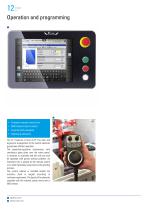
• Compact manual control unit • EMC-tested control cabinet • Ergonomically designed • Operating elements The S11 features a Fanuc 0i-TF. The clear and ergonomic arrangement of the control elements guarantees efficient operation. The projective-capacitive touchscreen, with continuous glass plate over the entire panel, is resistant to scratches and dirt and can even be operated with gloves without problem. An important role is played by the manual control unit, which facilitates setup close to the grinding process. The control cabinet is installed behind the machine, flush or angled according...
Open the catalog to page 12All STUDER catalogs and technical brochures
-
ecoLoad
2 Pages
-
roboLoad
2 Pages
-
insertLoad
2 Pages
-
S33
13 Pages
-
easyload
2 Pages
-
favoritCNC
11 Pages
-
smartLoad
2 Pages
-
favorit
13 Pages
-
S30
9 Pages
-
S121 / S131 / S141 Radius
15 Pages
-
Customer Care STUDER
7 Pages
-
S100
11 Pages
-
Customer Care UGG
13 Pages
-
uniLoad
2 Pages
-
S36
21 Pages
-
Synchronous tailstock
2 Pages
-
roboLoad
2 Pages
-
S31
24 Pages
-
Software
20 Pages
-
S41
28 Pages
-
WireDress®
4 Pages
-
S20
16 Pages
-
LaserControl™
2 Pages
-
StuderControl
4 Pages
-
Product Range
16 Pages
-
A Axis
2 Pages
-
S122
4 Pages
-
S121 / S131 / S141
20 Pages
-
S131 / S141 / S151
24 Pages
-
S121
16 Pages
-
S22
20 Pages
-
S110 / S120
20 Pages