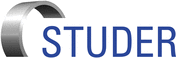
Group: UNITED GRINDING Group

Catalog excerpts
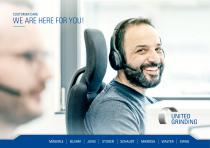
CUSTOMER CARE
Open the catalog to page 1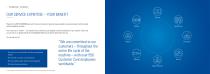
CUSTOMER CARE OUR SERVICE EXPERTISE – YOUR BENEFIT Products from UNITED GRINDING are built to meet our customers’ needs as long as possible, work economically, function reliably and be available at all times. From “start up” to “retrofit” – our Customer Care is there for you throughout the entire working life of your machine. That’s why you can rely on our global network of knowledgeable HelpLines and service technicians near you. You can count on us! We will be at your site quickly and offer uncomplicated support. We will help to increase your productivity. We work professionally, reliably...
Open the catalog to page 2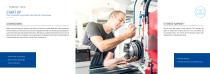
CUSTOMER CARE START UP ENSURES A SUCCESSFUL FIRST RUN FOR YOUR MACHINE. EXTENDED WARRANTY When commissioning your machine, we check all functions in great detail and, where necessary, test that options and accessories are correctly integrated. We train and provide your operating personnel with individual and detailed instructions. We take your specific requirements into account. If desired, we will grind a workpiece to your specifications. Experience from several hundred machine commissionings per year ensures a smooth start of production. You can trust the quality of your machine. This...
Open the catalog to page 3
CUSTOMER CARE THANKS TO QUALIFICATION, YOUR STAFF RECEIVES OPTIMAL TRAINING FOR THE EFFICIENT HANDLING OF THE MACHINE. PRODUCTION SUPPORT We offer customized training sessions, which can be done at your production facility and on your own machine. Our course categories range from general grinding to operation, programming, and special courses. We support you on-site with the production process. We will gladly advise you on process and cycle time optimization as well as special processes (for example integration of size control gauging, the changeover to new workpieces, or grinding wheels)....
Open the catalog to page 4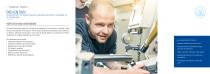
CUSTOMER CARE PREVENTION HELPS YOU PREVENT MACHINE DOWNTIMES AND EXTEND THE WORKING LIFE OF YOUR MACHINE. INSPECTION AND MAINTENANCE Our service technicians perform an on-site visual inspection of your machine to provide a clear picture of the condition of the machine. And to ensure the general maintenance of your machines, we follow a systematic servicing plan. You are free to choose whether you would like a one-time maintenance or a regular inspection of your machine. All maintenance work includes: esting and inspection of exposed parts T nspection of electrical and control systems I...
Open the catalog to page 5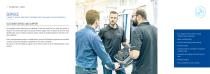
CUSTOMER CARE THANKS TO SERVICE, COMPETENT CUSTOMER CARE IS AVAILABLE ON-SITE OR REMOTELY. CUSTOMER SERVICE AND SUPPORT Our qualified service technicians are stationed all over the world and can reach you quickly if required. The service technicians can access technical support from the factory at any time. They identify faults, carry out repairs, measure, assess, restore the machine geometry, and make a condition appraisal. And if uncomplicated assistance is needed quickly: more than 50 HelpLine employees are available to assist you with any questions or problems you may have, worldwide....
Open the catalog to page 6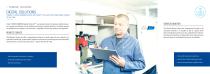
CUSTOMER CARE DIGITAL SOLUTIONS DIGITAL SOLUTIONS THANKS TO UNITED GRINDING DIGITAL SOLUTIONS™, YOU HAVE EVERYTHING UNDER CONTROL – AT ANY TIME. Under “UNITED GRINDING Digital Solutions™”, we develop solutions to help you simplify processes, increase the efficiency of your machines and improve overall productivity. Our digital services are available for the majority of our machines – regardless of when they were put into operation. REMOTE SERVICE With Remote Service we offer a comprehensive solution for ideal support of your machines. Our specialists provide fast, system-specific support to...
Open the catalog to page 7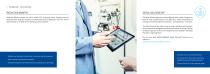
CUSTOMER CARE DIGITAL SOLUTIONS PRODUCTION MONITOR Production Monitor provides you with a reliable 24/7 monitoring service. Operating and nonproductive times, production quantities, and downtimes times are displayed in real-time. The Production Monitor is the ideal tool for optimizing machine utilization. The Digital Solutions app puts our service offerings in your pocket. The app combines the most important functions of an MES and a remote service portal and provides all relevant key figures for production – and maintenance – at all times. The Digital Solutions app makes it easy to monitor...
Open the catalog to page 8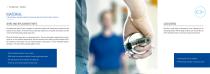
CUSTOMER CARE THE MATERIAL SERVICE ENSURES YOUR MACHINE HAS EVERYTHING IT NEEDS. SPARE AND REPLACEMENT PARTS An experienced team of parts managers is exclusively tasked with identifying and delivering the spare parts you require. To ensure that your spare part reaches you as quickly as possible, we store a few hundred thousand original spare parts. We offer a wide range of accessories, from dressing tools to measuring probes: We are happy to advise you and provide you with information about our extensive range of accessories. We treat selected spare parts as replacement parts: They are...
Open the catalog to page 9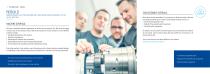
CUSTOMER CARE REBUILD ENSURES THAT YOUR MACHINE WILL ONCE AGAIN WORK AS RELIABLY AS IT DID ON THE FIRST DAY. MACHINE OVERHAUL We have a dedicated overhaul department at almost every production site. We would be happy to advise you on the overhaul of your machine and assess the current situation on-site. Machine overhaul includes: omplete dismantling of the machine C epainting the machine and components R e-building the machine and the associated geometry R e-commissioning, including functional and geometry testing R SUB-ASSEMBLY OVERHAUL We analyze the sub-assemblies of your machine in...
Open the catalog to page 10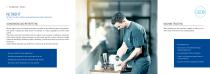
CUSTOMER CARE RETROFIT IS USED TO EQUIP YOUR MACHINE WITH NEW FUNCTIONS. MACHINE TRADE-INS We are happy to carry out complex conversions or retrofits on your machine to open up new production options or expand your range of parts. For example, it is easy to upgrade to a current control system. This process starts with consultation with our experts at your premises, including an assessment of the current situation. During conversion, we will provide you with a loaner machine as needed (subject to availability). Wherever possible, retrofitting is carried out directly on site by our service...
Open the catalog to page 11All STUDER catalogs and technical brochures
-
ecoLoad
2 Pages
-
roboLoad
2 Pages
-
insertLoad
2 Pages
-
S33
13 Pages
-
easyload
2 Pages
-
favoritCNC
11 Pages
-
smartLoad
2 Pages
-
favorit
13 Pages
-
S30
9 Pages
-
S121 / S131 / S141 Radius
15 Pages
-
Customer Care STUDER
7 Pages
-
S100
11 Pages
-
uniLoad
2 Pages
-
S36
21 Pages
-
Synchronous tailstock
2 Pages
-
roboLoad
2 Pages
-
S31
24 Pages
-
Software
20 Pages
-
S41
28 Pages
-
WireDress®
4 Pages
-
S20
16 Pages
-
S11
20 Pages
-
LaserControl™
2 Pages
-
StuderControl
4 Pages
-
Product Range
16 Pages
-
A Axis
2 Pages
-
S122
4 Pages
-
S121 / S131 / S141
20 Pages
-
S131 / S141 / S151
24 Pages
-
S121
16 Pages
-
S22
20 Pages
-
S110 / S120
20 Pages