Catalog excerpts
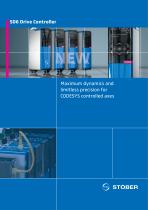
Maximum dynamics and limitless precision for CODESYS controlled axes
Open the catalog to page 1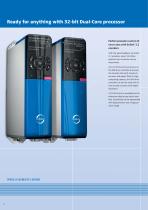
Ready for anything with 32-bit Dual-Core processor Perfect precision control of servo axes with EnDat® 2.2 encoders With the speed feedback via EnDat® 2.2 encoders, about 33 million positions per revolution can be determined. The 32-bit Dual-Core processor on the SD6 drive controller processes the encoder data with maximum accuracy and speed. With its high computing capacity, the SD6 drive controller can also be used with future encoder systems with higher resolution. A 32-bit format is available for the reference value/actual value interface. So positions can be represented with high...
Open the catalog to page 2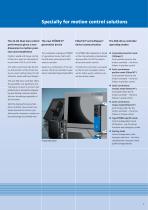
Specially for motion control solutions The 32-bit Dual-Core control The new STÖBER 6th performance gives a new generation device dimension to motion precision and smoothness The completely redesigned STÖBER Position, speed and torque control of the servo axes are calculated at a cycle time of 62.5 μs (16 kHz). 6 generation device starts with the SD6 drive controller and MC6 motion controller. This allows extremely high dynamics and precision of the drives due to very short settling times for fast reference values and load changes. Based on a combination of the two devices, the drive...
Open the catalog to page 3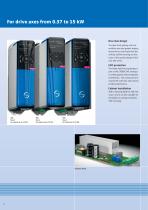
For drive axes from 0.37 to 15 kW New look design The dark front glazing with the multiline text and graphic display, operation by control pad and the striking Softline housing are features of the quality design of the new SD6 series. EMC protection The sheet steel housing design is part of the STÖBER EMC strategy to shield against electromagnetic interference. This construction increases RFI immunity and reduces emitted interference. Cabinet installation With a housing depth of 280 mm, sizes 1 and 2 are also suitable for installation in compact cabinets 300 mm deep.
Open the catalog to page 4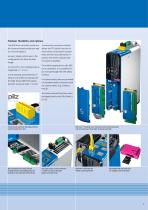
Modular flexibility and options The SD6 drive controller stands out for its proven board architecture and its universal options. So every single system axis in the configuration can have the best design. A control for a 24V holding brake is integrated (< = 2.5 A) A non-wearing, fully electronic interface is provided as standard for the Safe Torque Off (STO) safety function (response time < 10 ms). A technically innovative solution allows the STO safety function to work without interruptive system tests and their documentation. In practice this means impressively increased availability. On...
Open the catalog to page 5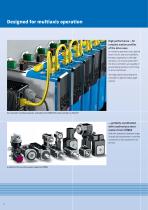
Designed for multiaxis operation High performance – for complex motion profiles of the drive axes In multiaxis operation every geared motor has its task and conditions. Multiaxis applications with high dynamics can only be achieved if the drive controllers are capable of guaranteeing precision and timing in all circumstances. The high performance SD6 drive controller is ideal for these applications. Drive controller in multiaxis operation, controlled by the STÖBER MC6 motion controller via EtherCAT® ... perfectly coordinated with synchronous servo motors from STÖBER With this extensive...
Open the catalog to page 6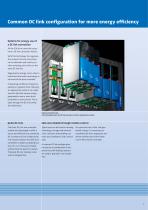
Common DC link configuration for more energy efficiency Options for energy use of a DC link connection All the SD6 drive controller series have a DC link connection facility. With this technology the regenerative energy from one servo drive can be absorbed and used by another motoring servo drive on the same DC link line. Regenerative energy occurs when a load drives the motor and energy is returned to the drive controller. If operating conditions change frequently or regularly from motoring to regenerative mode, it can make sense to feed the surplus energy generated to one or more drive...
Open the catalog to page 7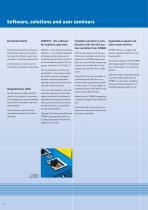
Software, solutions and user seminars CODESYS – the software for multiaxis operation The DriveControlSuite commissioning software version 6 has all the functions for efficient use of drive controllers in multiaxis applications. CODESYS – from 3S-Smart Software Solutions – is a hardware independent programming software or a complete programming system for the international standard PLC languages according to IEC 61131-3. Commissioning is made easy, for example by a multiaxis oscilloscope. The centralization of all the axis parameters in one program operation makes it easier to program...
Open the catalog to page 8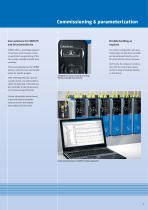
Commissioning & parameterization User seminars for CODESYS and DriveControlSuite Flexible handling as required STÖBER offers a multistage program of seminars which focuses mainly on application programming of the MC6 motion controller and SD6 drive controller. For system configuration and parameterization the SD6 drive controller can be addressed directly via the DriveControlSuite device software. And finally, the display in combination with the control pad, allows for fine-tuning of settings directly on the device. The courses take place at the STÖBER seminar centre but can also be held...
Open the catalog to page 9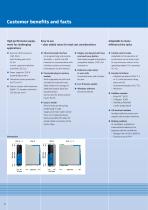
Customer benefits and facts High performance equipment for challenging applications Easy to use – clear added value for total cost considerations Adaptable to many different drive tasks b Dual-Core RISC processor (200 MHz) with floating point unit 32-bit current, speed and position controllers 62.5 μs b Ethernet-based interface For programming and parameterization – and for the IGB network for communication with multiaxis systems and remote maintenance via the internet. b Flexible control mode Adaptable to the operation of synchronous servo motors and to asynchronous motors in the operating...
Open the catalog to page 10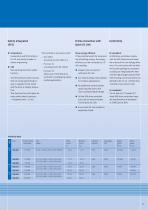
D link connection with Quick DC Link b Competence Cooperation with PILZ GmbH & Co. KG, the industry leader in safety engineering. b STO Non-wearing electronic safety function. The STO safety function ensures that no torque-generating energy is supplied to the motor and the drive is reliably torquefree. This function forms the basis for many other safety functions. – Response time < 10 ms TÜV certified in accordance with: – SIL3 (HF1) According to EN 61800-5-2 – PLe (cat. 4) According to EN ISO 13849 PLe (cat. 4) Allows use of the SD6 drive controller in challenging safetyrelated...
Open the catalog to page 11All STÖBER catalogs and technical brochures
-
Bottom brake resistor
14 Pages
-
PS Two-speed Gearbox
26 Pages
-
ServoFit Servo Gear Units
539 Pages
-
ServoFit® PE
20 Pages
-
Synchronous Servo Geared Motors
26 Pages
-
SMS PEPlanetary Geared Motors
14 Pages
-
STÖBER DIRECT 2011
12 Pages
-
ZV Rack and Pinion Drive
2 Pages
-
ZTRS Rack and Pinion Drive
6 Pages
-
Target Industry Packaging
8 Pages
-
Target Industry Machine Tools
12 Pages
-
POSIDYN® SDS 5000 Servo Inverter
14 Pages
-
PE Planetary Gear Unit
6 Pages
-
Energy Efficiency
6 Pages
-
MC6 Motion Controller
12 Pages
-
SMS Servo Geared Motors EZ
556 Pages
-
Variable speed drives
243 Pages
-
SMS/MGS Gear units
163 Pages
-
SMS Servo Geared Motors ED/EK
620 Pages
-
Rack and pinion drive ZTRS/ZTR/ZR
180 Pages
-
ServoCool Planetary gear units
88 Pages
-
MGS Modular Geared Motors System
325 Pages
-
MGS AC Geared Motors IE2
285 Pages