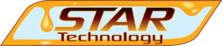
Catalog excerpts
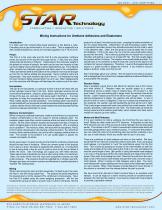
Mixing Instructions for Urethane Adhesives and Elastomers Introduction: It is often said that compounding liquid polymers is like baking a cake. Everything has to get mixed well or it's not a cake. That is especially true with urethane elastomers, which are normally supplied in an A - B mix or kit. Polyol: The Part A is the resin side and the Part B is the isocyanate. Urethane resins are cousins of the alcohol and sugar family. In fact, they are called "polyfunctional alcohols or Polyols". Depending on the molecular weight of the polyols or mixture of polyols, the resin can be very low viscosity or they can be so highly viscous that they must be melted before use. The urethane often contains any catalysts, pigments and fillers used in the composition. These sometimes settle to the bottom of the container and must be brought up into the mix before adding the isocyanate. Some urethane resins are hygroscopic - they suck moisture right out of the air. It is important to keep the resin container tightly covered when it is not in use. Often, displacing the air in the container with Nitrogen will help keep the moisture out of the resin. Isocyanates: The part B, the isocyanate, is a peculiar animal in that it will react with any active hydrogen source that it can find. Active hydrogen sources can be found almost anywhere...moisture, acids, bases, skin mucous membranes, linings of the eye, etc. and also in the resins used in the Part A. It is most important to keep the isocyanate dry and in the container when using it. Wear rubber gloves and eye protection. Any clothing which has become contaminated with an isocyanate should be laundered before wearing again. Leather articles which have been contaminated should be discarded as they cannot be cleaned sufficiently for reuse. Moisture Contamination: When mixing any urethane chemicals, make sure that there is no source for moisture contamination in the mix vessel or stirring materials used. For example, paper cups often contain moisture which can leach into the resin mixture. By the same method, wooden stirring sticks hold lots of moisture which will again leach into the resin and cause problems. Why is moisture such a problem? The moisture, water, will react with the isocyanate, Part B, to form carbon dioxide gas in the reacting urethane product. So, rather than having a hard urethane plastic, you end up with a spongy urethane foam or froth. The answer to the problem is to use coated paper or plastic mix vessels and plastic stir sticks. By the same token, the pails and drums that hold the urethane components should be kept free of moisture. When you remove some of the product from a pail or a drum, the liquid is replaced with ambient air. It is important to use a drying tube in the air vent of a pail or drum to dry the air before it enters the drum. Star Technology can supply you with these devices. These same kinds of problems can occur when using meter-mix machinery. Often, the tanks which hold the resin and isocyanate mixtures are kept under pressure. The pressure should be supplied by a nitrogen gas tank. Nitrogen gas does not contain moisture and therefore is a perfect product to "blanket” the holding tanks. Mixing When hand mixing the resin and the isocyanate, it is best to pour the resin, the Part A, into the mixing vessel first. The product should be weighed to the nearest gram or to the nearest 0.5%, whichever is more precise. Next, the Part B is added using the same weighing procedure. Mix the two components using a stir stick or a paint mixer in a drill or drill press. Mix the product for at least 3 minutes by the clock...scraping the sides and bottom of the mix vessel frequently. [Remember, it's just like baking a cake!] After the products have been mixed, they should be poured into the mold or used in the adhesive step. Often, the end product must be totally free of voids and bubbles. If this is the case, the mix must be vacuumed before being poured into the mold. This is done by putting the mix vessel into a vacuum chamber and pulling a vacuum of at least 28" Hg. This will usually degas the product within 5 minutes. The reaction mixture will bubble and froth. You should have a mix container at least 4 times the volume of the liquid in the container for vacuum degassing. Therefore, 1 quart of the liquid product will require a 1 gallon bucket to degas the mixture. If you intend to vacuum degas a product, make sure that you tell Star Technology about your wishes. We will need to formulate to product with a delayed gel time and extra air release additives to allow sufficient time to accomplish the process. Reaction Rates: Now is probably a good time to talk about the reaction rate of the mixture and what affects it. Reaction rates are usually stated at a certain temperature and at a certain mass of material [e.g.: 25 minutes in a 100 gram mass]. If you are working with a larger mass, the reaction time will be shorter. Lower masses and thin films will be much longer. If the reaction starting temperature is higher, the reaction rate will be faster. A rule of thumb is that for every 10 degrees C that you increase the temperature of the reactants, the reaction rate will double [the gel time will be cut in half]. That is why larger masses will react more quickly than small masses. As the reaction proceeds, it generates its own heat. The heat builds up inside the mixing vessel and the reaction goes faster, which makes more heat, which makes the reaction go even faster... Molds and Mold Releases: If it is your intention to mold a urethane, the first thing that you need is a mold! Molds are often made from RTV silicones. It important to note that RTV silicones are one of the sources of active hydrogen that we discussed earlier. The surface of an RTV mold is covered with reactive sites which will bond like gangbusters to your urethane casting. To overcome this problem, you can make the mold out of something else, like another urethane or you can use a mold release, which you would need to use in any case. There are a plethora of mold releases out there on the market. We have found that the non-silicone containing versions work best. If you use a spray mold release, it is important to "cure" the mold before using it for the first time. This is done by spraying an excess of the mold release on both the inside and outside of the mold, placing the mold in an oven and baking the mold for some length of time. [Be careful of using flammable mold released in an oven.] This process will thin the mold release and make it flow into the pores of the mold, thus sealing the mold. Remove the mold from the oven, wipe out all of the excess mold release and give the mold a very thin coat of mold release. When it comes to mold releases, less is best. Too much mold release will cause bubbling over the surface of the molded part and will ruin your casting. Often, mold releases must be baked to insure that all of the solvent is removed from the release before the part is poured. We have found that Johnson's Paste Furniture Wax is an excellent mold release. It can be wiped on a warm mold to provide an excellent barrier between the mold and the casting. It can also be mixed with mineral spirits to provide a sprayable release.
Open the catalog to page 1All STAR Technology catalogs and technical brochures
-
BC-28
2 Pages
-
BC-24
2 Pages
-
BC-22
2 Pages
-
Crystallization
1 Pages