
Catalog excerpts
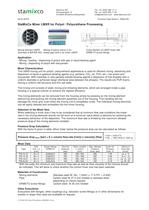
Stamixco AG Kronaustrasse 10 CH-8404 Winterthur/Switzerland Tel. +41 (0)52 338 17 11 Fax +41 (0)52 338 17 33 info@stamixco.com www.stamixco.com 09.04.30/PS Technical Data Sheet E_TB002-R2 O.D. x s StaMixCo Mixer LMXR for Polyol / Polyurethane Processing L1 L2 Mixing element LMXR Mixing of epoxy resins in an (licensee of BAYER AG) empty pipe and in an mixer LMXR Cross-Section of LMXR mixer with ERMETO screw fittings Application - Mixing / loading / dispersing of polyol with gas or liquid blowing agent - Mixing / dispersing of polyol with isocyanate Mixer Characteristics The LMXR mixing unit for polyol / polyurethane applications is used for efficient mixing, dissolving and dispersion of liquid or gaseous blowing agents (e.g. pentane, CO2, air, FCH, etc.) into polyol and isocyanate. With insoluble or only partially soluble blowing agents a dispersion of fine droplets with a uniform diameter is achieved (large interfacial area between the phases). The results are PUR foams having a uniform cell structure and thin cell walls. The mixing unit consists of static mixing and shearing elements, which are arranged inside a pipe housing in a special manner to achieve the highest efficiency. The mixing elements can be removed from the housing simply by pressing on the mixing element sleeve/ring and pushing the mixing element assembly out of the housing. This handling will not damage the mixer grid, even when the mixing unit is completely cured. The individual mixing elements can be easily cleaned and reinstalled into the mixer housing. Selection of the Mixer Size When selecting a mixer size it has to be considered that at minimum flow-rate conditions the shearrate in the mixing elements should not fall short of a minimum value which is decisive for achieving the necessary behaviour of the dispersion. The maximum flow-rate is limited by the maximum allowed pressure drop of the mixing elements installed. Pressure Drop Calculation With the factor K given in table „Mixer Data“ below the pressure drop can be calculated as follows: Pressure drop Mixer [bar] = K x volume flow-rate [l/min] x viscosity [Pas] 1 l/min = 0.06 m3/h 1 Pas = 1000 mPas or 1000 cp Mixer Data Type PM-12-18 PM-15-22 PM-18-27 PM-22-33 Pipe O.D. x s [mm] 30 x 3 38 x 4 38 x 4 42 x 3 Screw Fittings ERMETO G30SAC3 G38SAC3 G38SAC3 G42LAC3 Nominal pressure [bar] 280 280 280 160 Mixer Lengths L1 and L2 [mm] 290 / 344 330 / 388 380 / 438 480 / 522 Max. allowed Pressure Drop [bar] 280 280 280 160 Factor for Pressure Drop K 1.48 0.68 0.33 0.18 * Minimum Flow-rate [l/min] ca. 3 - 5 ca. 6 - 10 ca. 15 - 20 ca. 25 -35 * With the order the minimum and maximum flow-rate as well as thee viscosity of the mixture should be indicated. This will allow to check whether the correct mixer size has been selected. Materials of Construction - Mixing elements: - Pipe: - ERMETO screw fittings: Stainless steel W.-No.: 1.4542 (= 17-4 PH = A 630) Carbon steel St 37.4 zinc treated or stainless steel, depending on clients request Carbon steel, St 35 zinc treated Other Executions Executions with flanges, other couplings (e.g. reduction screw fittings) or in other dimensions for smaller or larger flow-rates are available on request. E_TB-002-R2_Polyol-Polyurethane_20090430_Kr.doc
Open the catalog to page 1All StaMixCo AG catalogs and technical brochures
-
GX Family of Static Mixers
1 Pages
-
SMB Extrusion Melt Blender
4 Pages
-
SMF
2 Pages