
Catalog excerpts
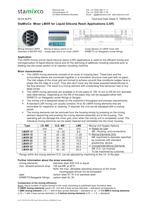
Stamixco AG Kronaustrasse 10 CH-8404 Winterthur/Schweiz 09.04.30/PS Tel. +41 (0)52 338 17 11 Fax +41 (0)52 338 17 33 Email info@stamixco.com www.stamixco.com Technical Data Sheet E_TB003-R3 StaMixCo Mixer LMXR for Liquid Silicone Resin Applications (LSR) Mixing element LMXR Mixing of epoxy resins in an (licensee of BAYER AG) empty pipe and in an mixer LMXR Cross-Section of LMXR mixer with ERMETO (or Swagelok) screw fittings Application The LMXR mixing unit for liquid silicone resins (LSR) applications is used for the efficient mixing and homogenization of liquid silicone resins and for the admixing of additives including colorants prior to feeding into the screw section of an injection moulding machine. Mixer characteristics • The LMXR mixing elements consists of an array of crossing bars. These bars and the surrounding sleeve are connected together in a monolithic structure (cast part with no gaps). The inlet edges of the mixer grid are formed to achieve smooth flow conditions (edges have a shape like the ridge of a roof). They also don’t have any flat areas exposed perpendicular to the flow direction. The result is a mixing element with outstanding flow behaviour free of any dead zones. • The LMXR mixing elements are available to fit into pipes of DN 15 mm to DN 50 mm diameter (see table below). Depending on the DN of the pipes they can be equipped either with ERMETO (or Swagelok) screw fittings or flanges. • The mixing unit is designed based on the customer's throughput and process requirements. • A standard LSR mixing unit usually contains 16 to 20 LMXR mixing elements that are removable for inspection or cleaning. If required, the unit can be equipped with a cooling jacket. • The mixing elements can be removed from the housing simply by pressing on the mixing element sleeve/ring and pushing the mixing element assembly out of the housing. This operating will not damage the mixer grid, even when the mixing unit is completely cured. The individual mixing elements can be easily cleaned and reinstalled into the mixer housing. Type I.D. ME mm 12 18 20 22 27 33 40 O.D. ME * mm 16 – 20 22 – 26 24 – 28 26 – 30 31 – 35 37 – 42 44 – 50 LME mm 8.0 11.25 12.25 13.5 16.5 20.0 24.0 Mixing Unit Supply Options a) Ready for Use ME, Housing, end connections. LMXR-12 b) Mixing Elements Only LMXR-18 ME machined to diameter specified LMXR-20 by customer with standard LMXR-22 positioning device. LMXR-27 c) Unmachined Mixing Elements LMXR-33 ME O.D. not finished. LMXR-40 To be machined by customer. * Range within the mixing element O.D. can be adjusted by machining to the I.D. of the pipe Further information about the mixer execution - mixing elements: stainless steel AISI 316 or equal - max. allowed pressure drop: 100 bar/ME at 20° C Note: the max. allowable operating pressure of the mixer housing/pipe should not be exceeded! - pipe: carbon steel ST 37.4 or stainless steel - ERMETO/Swagelok fittings: carbon steel St. 35 Comparison of the mixing efficiency Basis: Equal number of layers formed in the mixer according to published layer formation laws 2 LMXR mixing elements (each L/D ~0.6 with 8 bars across diameter = standard) corresponds to 1 SMX mixing element (L/D = 1 with 8 bars across diameter = standard) or to ~1 1/3 SMX/4 mixing elements (L/D = 1 with 4 bars across diameter) or 3 helical mixing elements (L/D = ~1.5 = standard) 6.4.E_TB-003-R3_LSR-Liquid Silicone Resins_20090430_Kr.doc
Open the catalog to page 1All StaMixCo AG catalogs and technical brochures
-
GX Family of Static Mixers
1 Pages
-
SMB Extrusion Melt Blender
4 Pages
-
SMF
2 Pages