
Catalog excerpts
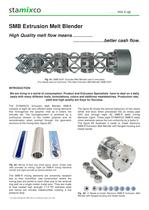
. . . mix it up SMB Extrusion Melt Blender High Quality melt flow means …………. …………..…….better cash flow. Fig. #1: SMB-GXS* Extruder Melt Blender cast in one piece (For details see our brochure:”The New Extrusion Melt Blender SMB-GXS” INTRODUCTION We are living in a world of consumption. Product and Extrusion Specialists have to deal on a daily basis with many different tools, formulations, colors and additives mastebatches. Production rate, yield and high quality are Keys for Success. The STAMIXCO Extrusion Melt Blender SMB-R consists of eight (8) very efficient static mixing elements that homogenize the polymer melt as it enters the extruder die. The homogenization is achieved by a continuous division of the molten polymer and its recombination when pushed through the geometric structure of the mixing bars (figure #2). The figure #2 shows the laminar behaviour of two resins (white and blue) when processed into an empty pipe (left) and through eight (8) SMB-R static mixing elements (right). These eight STAMIXCO SMB-R static mixer elements reduce the non-uniformity by a factor 6. The figure #3 illustrates a ready to install Stamixco SMB-R Extrusion Melt Blender with flanged housing and heater bands. Fig. #2: Mixing of blue and white epoxy resins. Empty tube (left) provides no mixing. Eight (8) SMB-R mixing elements (center and right) provide an almost perfect mix. The SMB-R mixing elements are extremely resistant due to their monolithic cast construction where the mixing bars are joined to each other and to the external ring wall via a single molten metal pour. They are made of heat treated high strength 17-4 PH stainless steel and hence are virtually indestructible creating a low pressure drop. * The Static Melt Blender SMB-GXS is not offered for sale in the USA. Fig. #3: A Ready-to-Install Stamixco SMB-R Extrusion Melt Blender with flanged housing and heater bands.
Open the catalog to page 1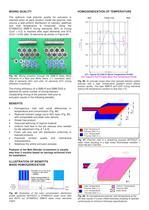
MIXING QUALITY The optimum melt polymer quality for extrusion is reached when at each location inside the polymer melt volume a well-uniform distribution of colorant, additives and melt temperature is measured. Using the STAMIXCO SMB-R mixing elements, 80% of mixing (CoV = 0.2) is reached after eight elements and 97% (CoV = 0.03) after 16 elements as shown in Figure #4. Center Line Fig. #4: Mixing evolution through the SMB-R Static Mixer Elements of a Blue and White resins (1:1 volumetric ratio). After 8 elements 80% and after 16 elements 97% mixing The mixing efficiency of a SMB-R and...
Open the catalog to page 2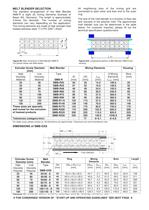
All neighboring bars of the mixing grid are connected to each other and their end to the outer ring. MELT BLENDER SELECTION The standard arrangement of the Melt Blender SMB-R is eight (8) mixing elements (licensee of Bayer AG, Germany). The length is approximately 4-times the diameter. The number of mixing elements can vary depending on the application. The mixing elements are made of high strength heat treated stainless steel 17-4 PH (DIN 1.4542). The size of the melt blender is a function of flow rate and viscosity of the polymer melt. The approximate melt blender size can be determined...
Open the catalog to page 3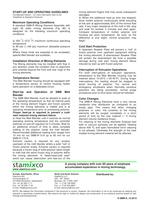
START-UP AND OPERATING GUIDELINES (Condensed Version – for more information refer to the Installation & Operation brochure) Maximum Operating Conditions A standard SMB-R Mixing Element Assembly with eight (8) static mixing elements (Fig. #6) is designed for the following maximum operating conditions: o o a) 300 C (572 F) maximum continuous operating temperature b) 80 bar (1,160 psi) maximum allowable pressure drop Where these limits are expected to be exceeded, special Melt blender are available. Installation Direction of Mixing Elements The Mixing elements may be installed with flow in any...
Open the catalog to page 4All StaMixCo AG catalogs and technical brochures
-
GX Family of Static Mixers
1 Pages
-
SMF
2 Pages