Catalog excerpts
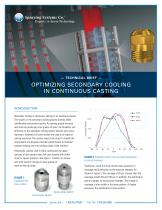
— TECHNICAL BRIEF — OPTIMIZING SECONDARY COOLING IN CONTINUOUS CASTING Figure 2: Standard FullJet ® nozzle distribution at various pressures Historically, nozzles used in billet casting and the upper sections of slab casters were full cone nozzles with either round or square patterns. See Figure 1. Casters ran slower, and mills weren’t running as many grades of steel as they do today. FIGURE 1: Traditional full cone nozzles Secondary cooling in continuous casting is an important process. The nozzles in the secondary cooling process directly affect solidification and product quality. As casting speeds increase and mills are producing more grades of steel, the flexibility and efficiency of the secondary cooling system become even more important. Hydraulic full cone nozzles are used in all types of casting machines. The nozzles need to be robust to handle the environment and provide consistent performance to maintain constant cooling over the working range of the machine. FIGURE 2: Standard FullJet® full cone nozzle distribution at various pressures Traditional, round full cone nozzles have variations in coverage and distribution as the pressure changes. As shown in Figure 2, the coverage at 20 psi is lower than the coverage at both 60 and 100 psi. In addition, the distribution profile changes as the pressure changes. The change in coverage is also visible in the spray pattern. At higher pressures, the distribution is more uniform. Square spray pattern Round spray pattern spray.com | 1.800.95.SPRAY | Intl. Tel: 1.630.665
Open the catalog to page 1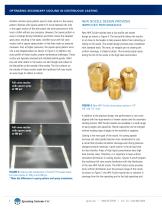
OPTIMIZING SECONDARY COOLING IN CONTINUOUS CASTING Another common spray pattern used in older casters is the square pattern. Nozzles with square patterns fit nicely between the rolls in the upper section of the slab caster and were perceived to fully cover a billet without any overspray. However, the square pattern is easy to misalign during installation and often misses the targeted spray area, resulting in hot spots. Another issue with full cone nozzles with a square spray pattern is that they rotate as pressure increases. And, at higher pressures, the square spray pattern turns into a...
Open the catalog to page 2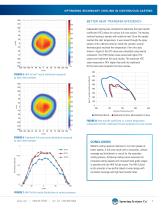
OPTIMIZING SECONDARY COOLING IN CONTINUOUS CASTING x (mm) FIGURE 5: HHX FullJet® nozzle distribution measured by laser sheet analyzer Independent testing was conducted to determine the heat transfer coefficient (HTC) values for various full cone nozzles. The testing involved heating a sample with inductive heat. Once the sample reached the start temperature, it was moved through the spray pattern with a defined velocity. Inside the cylinder, several thermocouples recorded the temperature. From this data, shown in Figure 8, the HTC value was calculated using inverse conduction. The HHX...
Open the catalog to page 3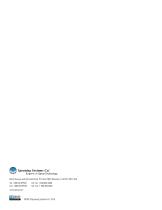
Spraying Systems Co.9 Experts in Spray Technology North Avenue and Schmale Road, PO. Box 7900, Wheaton, IL 60187-7901 USA Tel: 1.800.95.SPRAY Intl. Tel: 1.630.665.5000
Open the catalog to page 4All Spraying Systems Co. catalogs and technical brochures
-
G U N J E T® S P R AY G U N S
64 Pages
-
WindJet Air Products
28 Pages
-
Air Atomizing Nozzles
62 Pages
-
Fine Spray Nozzles
16 Pages
-
Hollow Cone Nozzles
42 Pages
-
Flat Spray Nozzles
56 Pages
-
Full Cone Nozzles
52 Pages
-
PWM Spray Control Panel
2 Pages
-
Optimizing Your Spray System
47 Pages
-
AutoJet Gas Cooling System
4 Pages
-
PWM Flow Control
2 Pages
Archived catalogs
-
CU150A GunJet Spray Gun
2 Pages