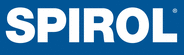

Catalog excerpts
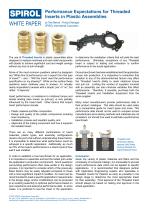
WHITE PAPER Performance Expectations for Threaded Inserts in Plastic Assemblies by Tara Meinck - Product Manager SPIROL International Corporation The use of Threaded Inserts in plastic assemblies allow designers to replace machined and cast metal components with plastic to achieve significant cost and weight savings without any loss of joint strength. to determine the installation criteria that will yield the best performance. Ultimately, acceptance of any Threaded Insert is subject to testing and evaluation to confirm performance in the actual application. Some of the most common questions asked by designers are “What kind of performance can I expect from this type of Insert?” – and – “Will this Insert meet the performance specification on my drawing?” While on the surface these questions seem relatively easy to answer, it’s actually nearly impossible to answer with a simple “yes” or “no;” but rather “it depends.” Once a benchmark has been established and the application moves into production, it is imperative to remember that variation to any of the aforementioned factors may affect the Threaded Insert’s ability to resist rotational torque and pull out. Limiting the number of suppliers involved with an assembly can also minimise variables that affect performance. Therefore, if possible, purchase both the Threaded Inserts and Installation Equipment from the same supplier. Insert performance, or resistance to rotational torque and tensile loading (also known as pull-out), is only partially influenced by the Insert itself. Other factors that impact Insert performance include: • Plastic material and filler composition, • Design and quality of the plastic components including hole consistency, • Installation process and resultant quality, and • Alignment of the mating component and how it supports the installed Insert. Many Insert manufacturers provide performance data in their product catalogue. This data should be used solely as a comparative guide for Insert types and sizes. This performance data should not be used to compare across manufacturers since testing methods and materials are not consistent, nor should it be used to estimate a performance benchmark. There are so many different combinations of Insert materials, plastic types, and assembly configurations (local to the joint) that without understanding these factors, it is impossible to determine what performance could be achieved in a specific application. Additionally, as much as 75% of the Insert’s performance is a direct result of how well it was installed. In order to establish a true benchmark for an application, it is imperative to assemble and test the bolted joint under the application’s production environment. Since questions surrounding performance often arise earlier in the design process, it is important to consider which of the previously listed factors may be easily adjusted compared to those with a more significant impact if modified. An Insert can be recommended to meet a specific application’s requirements in the design stage, and/or modifications can be proposed to an existing assembly to optimise performance based on prior experience and extensive performance data. In some cases, it is preferred to test the Insert in the application Threaded Insert performance testing methods: (left) Tensile (Pull-out) Strength and (right) Rotational Torque Conclusion: Given the variety of plastic materials and fillers and the complexity of component design, it is impossible to provide Insert performance data which can be applied to specific applications. It is recommended that designers partner with Application Engineering experts who specialise in Threaded Inserts for Plastics as early as possible in the design stage to determine the most appropriate Insert for their assembly. Final approval of the Threaded Insert should always be based on testing and approval in the actual application. © 2022 SPIROL International Corporation No part of this publication may be reproduced or transmitted in any form or by any means, electronically or mechanically, except as permitted by law, without written permissio
Open the catalog to page 1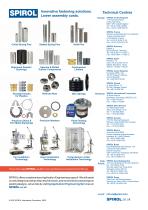
Innovative fastening solutions. Lower assembly costs. Technical Centres Europe SPIROL United Kingdom Coiled Spring Pins Alignment Dowels / Bushings Slotted Spring Pins Spacers & Rolled Tubular Components Solid Pins Compression Limiters Threaded Inserts for Plastics Railroad Nuts Disc Springs Americas SPIROL International Corporation Precision Shims & Thin Metal Stampings Precision Washers Parts Feeding Technology SPIROL Canada 3103 St. Etienne Boulevard Windsor, Ontario N8W 5B1 Canada Tel. +1 519 974 3334 Fax. +1 519 974 6550 SPIROL Mexico Avenida Avante #250 Parque Industrial Avante...
Open the catalog to page 2All SPIROL catalogs and technical brochures
-
Alignment Dowels/Bushings
12 Pages
-
Compression Limiter Design Guide
20 Pages
-
Slotted Spring Pins
16 Pages
-
Latch Pins for Plastics
2 Pages
-
Railroad Nuts - AAR Series
2 Pages
-
SPIROL Corporate Brochure
12 Pages
-
Disc Springs
20 Pages
-
Coiled Spring Pins
24 Pages
-
Series RH600 Twist-Lok™ Pins
2 Pages
-
Cosmestic Pins 550 series
2 Pages
-
Installation Technology
8 Pages
-
SPIROL Precision Shims
8 Pages
-
Medical Device Applications
2 Pages
-
SPIROL Solid Pins Catalog
12 Pages
-
Series 2000 Series 2000
4 Pages
-
Aerospace Applications Flyer
2 Pages
-
PH series PH series
2 Pages
-
HC series HC series
2 Pages
-
Tables Standard
2 Pages
-
Tables Lift and Roll
2 Pages
-
SPD, CXA, CXD, CXE CRD
2 Pages
-
880 Series
2 Pages