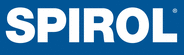

Catalog excerpts
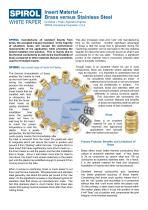
WHITE PAPER Insert Material – Brass versus Stainless Steel by Michael J. Pasko, Application Engineer SPIROL International Corporation, U.S.A. SPIROL manufactures all standard Inserts from brass, the accepted industry standard. In the majority of situations brass will exceed the performance requirements of the application while providing the lowest installed cost solution. This is mainly due to the thermal conductivity as well as the machinability of brass compared to other materials that are sometimes used for threaded Inserts. SPIROL has a broad range of Inserts for Plastics. This also increases costs and “cuts” into manufacturing time on the machine. Another significant advantage of brass is that the scrap that is generated during the machining operation can be sold back to the raw material supplier for about the same cost per pound as what it was purchased for in the raw state. Therefore, a significant portion of the material cost is recovered; whereas steel scrap is basically worthless. Though brass is an excellent choice for use in most components, there are instances where stainless steel may be required. It is important to understand that all materials possess unique characteristics that must be considered when selecting an Insert. A material that is functional in one environment may be problematic in another. For example, brass and stainless steel are both corrosion resistant, yet each will react differently to various corrosive agents. This document will summarise the most common features and benefits Self Tapping of brass and stainless steel as well as outline some of their limitations. The thermal characteristic of brass enables the Inserts to heat up and cool down quickly during the installation process into moulded plastic parts. For those Inserts that are installed with heat or ultrasonics, the Heat/Ultrasonic fact that the brass Insert heats up quickly translates into faster Moulded-In installation time since the operator Press-In does not have to wait long for the Insert to reach the proper temperature to melt the plastic. From a quality perspective, the fact that brass cools quickly means that immediately after the heat is removed from the Insert the plastic will start to coagulate which will secure the Insert in position and prevent it from “floating” within the hole. Compare this to a steel Insert that takes significantly more time to heat up — • the time it takes to melt the plastic and the total installation time is longer. Since it also takes more time for steel to cool down, the Insert must remain stationary in the plastic part until the plastic has solidified enough to prevent it from moving around in the hole. When it comes to machining, brass is much easier to cut than most ferrous materials. Whereas brass and stainless steel generally cost about the same per pound in the “raw state”, it’s the significant increase in manufacturing time for stainless steel that drives up manufacturers’ costs. The fact that stainless steel is much harder than brass also means that tooling must be replaced more often than when cutting brass. Brass Brass is an excellent material for use in most industrial and agricultural applications and typically offers the lowest cost solution: Primary Features, Benefits, and Limitations of Brass Brass offers much better thermal conductivity than carbon or austenitic stainless steel. In fact, brass is 2X as conductive as carbon steel and 15X as conductive as austenitic stainless steel. As a result, it is the optimal material for heat and ultrasonic installation of Inserts and other turned products. • Excellent thermal conductivity also translates into better positional accuracy of brass Inserts. Considering that brass cools quickly means that it can be “set” quickly and accurately in a component without fear that it will move within the plastic hole. On the contrary, a steel Insert must be braced within the molten plastic after it is put into position or else it will “float” out of position and compromise the joint integr
Open the catalog to page 1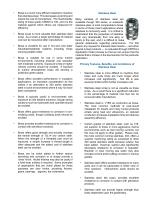
Brass is a much more efficient material to machine than stainless steel. This decreases cycle time and lowers the cost of manufacture. The machinability rating of brass grade C36000 is 100, and it is the material against which others are measured for efficiency. Brass scrap is more valuable than stainless steel scrap. As a result, a larger percentage of material cost can be recovered after manufacture. Brass is excellent for use in hot and cold water industrial/residential systems including those carrying potable water. • Brass is suitable for use in some marine environments including...
Open the catalog to page 2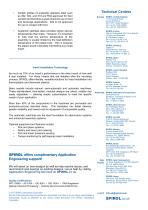
Certain grades of austenitic stainless steel such as 302, 304, and 316 are FDA approved for food contact and therefore a good choice for use in food and beverage applications. 303 is not approved for use in contact with food. Austenitic stainless steel provides higher service temperatures than brass. However, it is important to note that the service temperature of the assembly is usually limited by the heat deflection temperature of the plastic host. This is because the plastic would most likely melt before any metal Insert. Insert Installation Technology As much as 75% of an Insert’s...
Open the catalog to page 3All SPIROL catalogs and technical brochures
-
Alignment Dowels/Bushings
12 Pages
-
Compression Limiter Design Guide
20 Pages
-
Slotted Spring Pins
16 Pages
-
Latch Pins for Plastics
2 Pages
-
Railroad Nuts - AAR Series
2 Pages
-
SPIROL Corporate Brochure
12 Pages
-
Disc Springs
20 Pages
-
Coiled Spring Pins
24 Pages
-
Series RH600 Twist-Lok™ Pins
2 Pages
-
Cosmestic Pins 550 series
2 Pages
-
Installation Technology
8 Pages
-
SPIROL Precision Shims
8 Pages
-
Medical Device Applications
2 Pages
-
SPIROL Solid Pins Catalog
12 Pages
-
Series 2000 Series 2000
4 Pages
-
Aerospace Applications Flyer
2 Pages
-
PH series PH series
2 Pages
-
HC series HC series
2 Pages
-
Tables Standard
2 Pages
-
Tables Lift and Roll
2 Pages
-
SPD, CXA, CXD, CXE CRD
2 Pages
-
880 Series
2 Pages