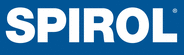

Catalog excerpts
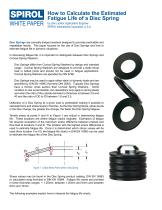
WHITE PAPER How to Calculate the Estimated Fatigue Life of a Disc Spring by John Leckfor, Applications Engineer SPIROL International Corporation, U.S.A. Disc Springs are conically shaped washers designed to provide predictable and repeatable results. This paper focuses on the use of Disc Springs and how to estimate fatigue life in dynamic situations. In discussing fatigue life, it is important to distinguish between Disc Springs and Conical Spring Washers. Disc Springs differ from Conical Spring Washers by design and intended usage. Conical Spring Washers are designed to provide a static thrust load in bolted joints and should not be used in fatigue applications. Conical Spring Washers are specified by DIN 6796. Disc Springs may be used to apply either static or dynamic loads and are specified by DIN EN 16983 (formerly DIN 2093). Typically Disc Springs have a thinner cross section than Conical Spring Washers. Some variation in size is permissible, but calculations only apply to spring steels and when the ratio of the outside diameter to thickness is between 16 and 40 and the ratio of OD to ID between 1.8 and 2.5. Deflection of a Disc Spring at a given load is predictable making it possible to calculate force and stress levels in the Disc. As the Disc Spring flexes, stress levels in the Disc change; the greater the change, the faster the Disc Spring fatigues. Tensile stress at points II and III in Figure 1 are critical in determining fatigue life. These locations are where fatigue cracks originate. Estimation of fatigue life requires evaluation of the maximum stress difference between preload and final load at locations II and III. The location with the highest stress differential is used to estimate fatigue life. Once it is determined which stress values will be used (from location II or III), the fatigue life charts in DIN EN 16983 can be used to estimate the fatigue life of the Disc Spring. III Figure 1: Critical Stress Points within a Disc Spring Stress values may be found in the Disc Spring product catalog, DIN EN 16983 or calculated using formulas in DIN EN 16984. Fatigue life charts are provided in three thickness ranges: < 1.25mm; between 1.25mm and 6mm and between 6mm and 14mm. The following examples explain how to interpret the fatigue life charts.
Open the catalog to page 1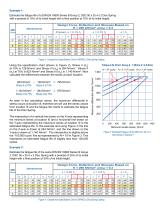
Example 1: Estimate the fatigue life of a DIN EN 16983 Series B Group 2, DSC 50 x 25.4 x 2 Disc Spring with a preload of 15% of its initial height with a final position at 75% of its initial height. Figure 4: Excerpt from Specification Chart in SPIROL's Disc Spring Catalog
Open the catalog to page 2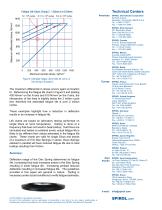
Figure 5: Estimated Fatigue Life for DSC 50 x 25.4 x 2 Disc Spring in Example 2 The maximum differential in stress occurs again at location III. Referencing the fatigue life chart in Figure 5 and plotting 430 N/mm2 on the X-axis and 810 N/mm2 on the Y-axis, the intersection of the lines is slightly below the 2 million cycle line; therefore the estimated fatigue life is over 2 million cycles. These examples highlight how a reduction in deflection results in an increase in fatigue life. Life charts are based on laboratory testing performed on single Discs at room temperature. Testing is done...
Open the catalog to page 3All SPIROL catalogs and technical brochures
-
Alignment Dowels/Bushings
12 Pages
-
Compression Limiter Design Guide
20 Pages
-
Slotted Spring Pins
16 Pages
-
Latch Pins for Plastics
2 Pages
-
Railroad Nuts - AAR Series
2 Pages
-
SPIROL Corporate Brochure
12 Pages
-
Disc Springs
20 Pages
-
Coiled Spring Pins
24 Pages
-
Series RH600 Twist-Lok™ Pins
2 Pages
-
Cosmestic Pins 550 series
2 Pages
-
Installation Technology
8 Pages
-
SPIROL Precision Shims
8 Pages
-
Medical Device Applications
2 Pages
-
SPIROL Solid Pins Catalog
12 Pages
-
Series 2000 Series 2000
4 Pages
-
Aerospace Applications Flyer
2 Pages
-
PH series PH series
2 Pages
-
HC series HC series
2 Pages
-
Tables Standard
2 Pages
-
Tables Lift and Roll
2 Pages
-
SPD, CXA, CXD, CXE CRD
2 Pages
-
880 Series
2 Pages