Catalog excerpts
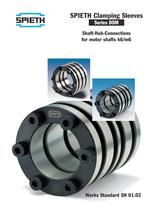
Series DSM Shaft-Hub-Connectionsfor motor shafts k6/m6 Works Standard SN 01.02 >
Open the catalog to page 1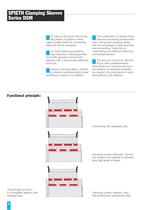
The combination of simply manu-factured connecting componentsand a low-priced clamping sleeve with the advantage of easy assembly and dismantling, make this an outstanding cost-effective shaft-hub connecting element.The amount of work for dismant-ling is often underestimated. If demands for a machine service or the question of recycling capability are present, the importance of quick dismantling is fully realized. Connecting with assembly play. Clamping screws tightened, connec-tion centred and capable of withstan- ding high levels of stress. Clamping screws released, easy dismantling with...
Open the catalog to page 2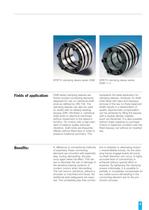
SPIETH clamping sleeve series DSM SPIETH clamping sleeve series DSM 1+2 > DSM series clamping sleeves are friction-locked connecting elements designed for use on cylindrical shaft ends as defined by DIN 748. The clamping sleeves can also be used on shafts with an already existing keyway (DIN 748/sheet 3, cylindrical shaft ends on electrical machines) without impairment to the sleeve's function. On motors with a high stan- dard of balance quality (reduced vibration), shaft ends are frequently offered without fitted keys in order to preserve rotational symmetry. This represents the ideal...
Open the catalog to page 3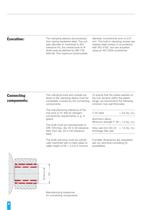
diameter concentricity error is 0.01 mm. The built-in clamping screws are cheese head screws in accordance with ISO 4762, and are actuated using an ISO 2936 screwdriver. The cylindrical bore and outside sur-faces of the clamping sleeve must be completely covered by the connecting components.The manufacturing tolerance of thehub bore is H7 (H6 for stringent concentricity requirements, e.g. in gears).The shaft must be manufactured toDIN 748 (max. dia. 50 in k6 tolerance field, from dia. 55 in m6 tolerance field).The shaft and bore must be cylindri-cally machined with a mean peak-to- valley...
Open the catalog to page 4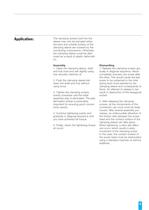
Assembly 1. Clean the clamping sleeve, shaft and hub bore and wet slightly using low-viscosity machine oil. 2. Push the clamping sleeve bet-ween the shaft and hub without using force. 3. Tighten the clamping screwsevenly crosswise until the initial assembly play is eliminated. The play elimination phase is particularly important for ensuring good concen- tricity results. 4. Continue tightening evenly andgradually in diagonal sequence until you have achieved full torque. 5. Finally, check the tightening torqueall round. > The clamping screws built into thesleeve may only be actuated when the...
Open the catalog to page 5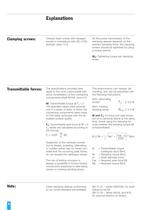
Cheese head screws with hexagonsocket in compliance with ISO 4762, strength class 12.9. As the power transmission of theclamping sleeves depends on the exerted clamping force, the clamping screws should be tightened by using a torque wrench. M > A : Tightening torque per clampingscrew > The specifications provided here apply to the most unfavourable tole- rance constellation of the connecting components (shaft k6/m6, bore H7). This phenomenon can hamper dis- mantling, and can be prevented with the following instructions: Adm. alternating torsion T M: Transmittable torque at F F > zul. <0,6...
Open the catalog to page 6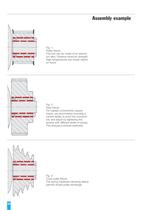
Fig. 1: Pulley fixture. The hub can be made of an alumini- um alloy. Observe minimum strength. High temperatures can impair retenti- on force! Fig. 2: Gear fixture. For highest concentricity require- ments, we recommend mounting a control facility to proof the concentri- city and adjust by tightening the screws with different levels of torque. This ensures a precise assembly. Fig. 3: Cone pulley fixture. The spring hardened clamping sleeve permits simple pulley exchange. >
Open the catalog to page 10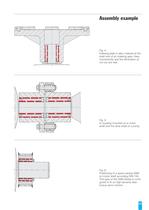
Fig. 4: Indexing plate in alloy material at the shaft end of an indexing gear. Here, concentricity and the elimination of run-out are vital. Fig. 5: A coupling mounted on a motor shaft and the drive shaft of a pump. Fig. 6: Positioning of a space saving DSM on motor shaft according DIN 748. This type of the DSM-Series is confi- gured to fit on high-dynamic less-torque servo motors. >
Open the catalog to page 11All SPIETH-MASCHINENELEMENTE GmbH & Co KG catalogs and technical brochures
-
catalogue
98 Pages
-
Application documentation
20 Pages
-
Clamping Nuts
8 Pages
-
Radial Plain Bearings
6 Pages
-
Guide Gibs
8 Pages
-
Guide Bushings
16 Pages
-
Clamping Sets
22 Pages
-
Locknut
22 Pages
-
Introduction
11 Pages
Archived catalogs
-
Product Range
8 Pages
-
Tension Nut Type AM
8 Pages
-
Precision Locknut heavy MSW
12 Pages
-
Precision Locknut MSR/MSA
12 Pages