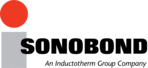
Catalog excerpts
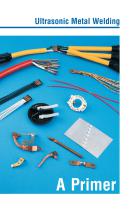
Ultrasonic Metal Welding
Open the catalog to page 1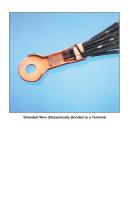
Stranded Wire Ultrasonically Bonded to a Terminal
Open the catalog to page 2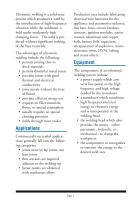
Ultrasonic welding is a solid-state process which produces a weld by the introduction of high-frequency vibration while the weldment is held under moderately high clamping forces. The weld is produced without significant melting of the base materials. The advantages of ultrasonic welding include the following: • permits joining thin to thick materials • permits dissimilar metal joints • provides joints with good thermal and electrical conductivity • joins metals without the heat of fusion • provides efficient energy use • requires no filler materials, fluxes, or special atmosphere • usually...
Open the catalog to page 3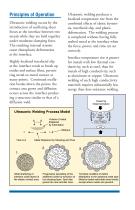
Ultrasonic welding produces a localized temperature rise from the combined effects of elastic hysteresis, interfacial slip, and plastic deformation. The welding process is completed without having fully melted metal at the interface when the force, power, and time are set correctly. Principles of Operation Ultrasonic welding occurs by the introduction of oscillating shear forces at the interface between two metals while they are held together under moderate clamping force. The resulting internal stresses cause elastoplastic deformation at the interface. Interface temperature rise is greater...
Open the catalog to page 4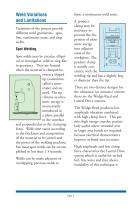
form a continuous weld joint. Weld Variations and Limitations A product clamp may be necessary to prevent the dispersion of ultrasonic energy into adjacent areas of the workpiece. The product clamp is usually concentric with the welding tip and has a slightly larger diameter than the tip. Variations of the process provide different weld geometries - spot, line, continuous seam, and ring welds. Welder Control Spot Welding Spot welds may be circular, elliptical or rectangular, solid or ring-like in geometry. They are formed when the material is clamped between a shaped tip (sometimes called a...
Open the catalog to page 5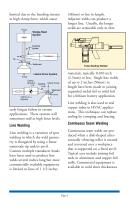
limited due to the bending stresses at high clamp force, which cause Force (38mm) or less in length. Adjacent welds can produce a longer line. Usually, the longer welds are attainable only in thin Wedge-Reed System Mass Coupling System Tube Sealing Welder Lateral Drive System Force Clamp Moment Welding Clamp Force Horn Weldment Anvil Clamp Moment early fatigue failure in certain applications. These systems will sometimes stall at high force levels. Line Welding Line welding is a variation of spot welding in which the weld geometry is elongated by using a linear sonotrode tip and/or anvil....
Open the catalog to page 6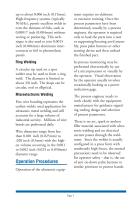
up to about 0.006 inch (0.15mm). High-frequency systems (typically 50 kHz), permit excellent welds in even the thinnest of foils, such as 0.00017 inch (0.004mm) without tearing or puckering. This technique is also used to join 0.0015 inch (0.004mm) aluminum interconnects to foil in photovoltaic panels. ment requires no elaborate or extensive training. Once the process parameters have been determined, usually by a process engineer, the operator is required only to load the parts into a nest or supporting/locating anvil assembly, press palm buttons or other starting device and then unload the...
Open the catalog to page 7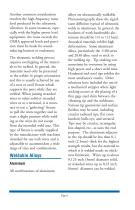
Another common consideration involves the high-frequency noise level produced by the ultrasonic vibration. In some instances, especially with the higher power level equipment, the noise exceeds the OSHA approved levels and provision must be made for soundreducing barriers or enclosures. alloys are ultrasonically weldable. Photomicrographs show the significant diffusion typical of ultrasonic welds in aluminum. In general, the hardness of work-hardenable aluminum should be 1/4 to 1/2 hard. Annealed materials exhibit high deformation. Some aluminum alloys, particularly the 1100 series and 2036...
Open the catalog to page 8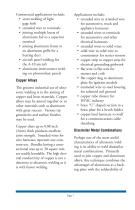
Commercial applications include: • seam welding of light gage foils • stranded wire to terminals • joining multiple layers of aluminum foil to a capacitor terminal • joining aluminum frame to an aluminum grille for a heating duct • aircraft panel welding for the A-10 aircraft • aluminum interconnect welding on photovoltaic panels Copper Alloys The greatest industrial use of ultrasonic welding is in the joining of copper and brass materials. Copper alloys may be joined together or to other materials such as aluminum with great success. Various tip geometries and surface finishes may be used....
Open the catalog to page 9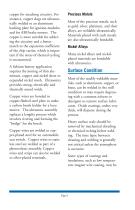
copper for attaching circuitry. For instance, copper slugs are ultrasonically welded to an aluminum backing plate for ignition modules and for ABS brake sensors. The copper is more suitable for soldering the circuitry and a better match to the expansion coefficient of the chip carrier, which is important if the stress of thermal cycling is encountered. A lithium battery application requires the joining of thin aluminum, copper and nickel sheet to expanded nickel mesh. Ultrasonics provides strong, electrically and thermally sound welds. Copper wires are bonded to copper-flashed steel plate...
Open the catalog to page 10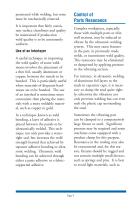
penetrated while welding, but some must be mechanically removed. It is important that fairly consistent surface cleanliness and quality be maintained if production weld quality is to be consistently uniform. Use of an Interlayer A useful technique in improving the weld quality of some weldments involves the placement of a thin foil, usually aluminum or copper, between the metals to be bonded. This is particularly useful when materials of disparate hardnesses are to be bonded. The use of an interleaf is sometimes more convenient than plating the materials with a more weldable material, such...
Open the catalog to page 11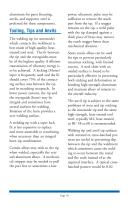
aluminum for parts fixturing, anvils, and supports; steel is preferred for these components. Tooling, Tips and Anvils The welding tip (or sonotrode) which contacts the weldment is best made of high-quality, heattreated tool steel. The fit between the tip and the waveguides must be of the highest quality if efficient transmission of vibratory energy is to be achieved. A locking (Morse) taper is frequently used and the fit should cover 75% of the contacting surface area between the tip and its matching receptacle. In lower power systems, the tip and the waveguide (horn) may be integral and...
Open the catalog to page 12All Sonobond Ultrasonics catalogs and technical brochures
-
FILTRATION NEWS
4 Pages
-
ultrasonics for metals
4 Pages
Archived catalogs
-
Ultrasonic Metal Machinery
2 Pages
-
Ultrasonic Plastic Machinery
10 Pages
-
Ultrasonic Filter Machinery
8 Pages