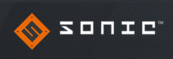

Catalog excerpts
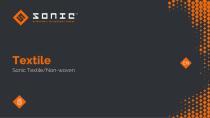
Textile Sonic Textile/Non-woven
Open the catalog to page 1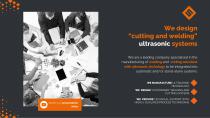
We design “cutting and welding” ultrasonic systems We are a leading company specialised in the manufacturing of welding and cutting solutions with ultrasonic techology to be integrated into automatic and/or stand-alone systems. WE MANUFACTURE ULTRASONIC TECHNOLOGY WE DESIGN “CUSTOMISED” WELDING AND CUTTING SYSTEMS Watch our presentation video WE PROVIDE TECHNICAL SUPPORT WITH HIGHLY QUALIFIED PROCESS TECHNI
Open the catalog to page 2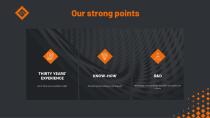
THIRTY YEARS’ EXPERIENCE Sonic Italia was founded in 1987 Producing technology is not enough We design and develop innovation alongside our clients
Open the catalog to page 3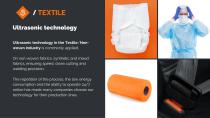
/ TEXTILEUltrasonic technology Ultrasonic technology in the Textile/Non-woven industry is commonly applied. On non-woven fabrics, synthetic and mixed fabrics, ensuring speed, clean cutting and welding precision. The repetition of the process, the low energy consumption and the ability to operate 24/7 online has made many companies choose our technology for their production lines.
Open the catalog to page 4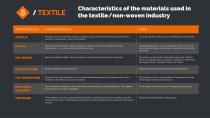
/ TEXTILE Characteristics of the materials used in the textile/non-woven industry
Open the catalog to page 5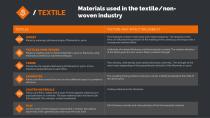
Materials used in the textile/nonwoven industry FACTORS THAT AFFECT WELDABILITY Made by weaving continuous loops of filaments or yarns. Thermoplastic content, mesh style and material elasticity. The elasticity of the links can influence the precision of the welding in the continuous technique with a consequent notched effect. Uniformity of material thickness and thermoplastic content. The random direction of the fibres gives the non-woven fabric excellent strength. Made by welding and/or intertwining fibers, yarns or filaments using mechanical, thermal or solvent techniques. YARNS Formed by...
Open the catalog to page 6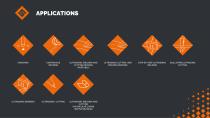
APPLICATIONS PUNCHING CONTINUOUS ULTRASONIC WELDING AND ULTRASONIC CUTTING AND STEP-BY-STEP ULTRASONIC GUILLOTINE ULTRASONIC WELDING CUTTING PROCESS WELDING PROCESS WELDING CUTTING ULTRASONIC BONDING ULTRASONIC CUTTING ULTRASONIC WELDING AND CUTTING ON CIRCULAR LOOMS (RAFFIA BIG BAGS)
Open the catalog to page 7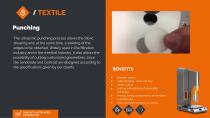
/ TEXTILE Punching The ultrasonic punching process allows the fabric shearing and, at the same time, a welding of the edges to be obtained. Widely used in the filtration industry and in the medical industry, it also allows the possibility of cutting customized geometries, since the sonotrode and contrast are designed according to the specifications given by our clients. CONTACT US FOR MORE INFORMATION process speed edge welding - does not fray clean cutting cutting and welding of any textile thickness energy saving compared to all the other technologies maximum performance
Open the catalog to page 8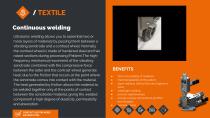
/ TEXTILE Continuous welding Ultrasonic welding allows you to assemble two or more layers of materials by passing them between a vibrating sonotrode and a contrast wheel. Normally the contrast wheel is made of hardened steel and has raised sections during processing (Pattern).The highfrequency mechanical movement of the vibrating sonotrode combined with the compressive force between the latter and the contrast wheel generate heat, due to the friction that occurs at the point where the sonotrode comes into contact with the material. The heat generated by friction allows the material to be...
Open the catalog to page 9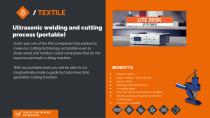
Ultrasonic welding and cutting process (portable) Sonic was one of the first companies that wanted to make our cutting technology accessible even to those small and medium-sized companies that do not need an automatic cutting machine. With our portable tools you will be able to cut longitudinally inside a guide but also have total geometric cutting freedom. • process speed • edge welding - does not fray • clean cutting • welding edge adjustment • changing angle • cuts and welds any thickness of fabric • energy savings compared to all other technologies • maximum versatility
Open the catalog to page 10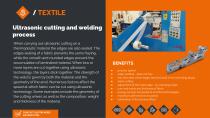
/ TEXTILE Ultrasonic cutting and welding process When carrying out ultrasonic cutting on a thermoplastic material the edges are also sealed. The edges sealing of a fabric prevents the yarns fraying, while the smooth and rounded edges prevent the accumulation of laminated material. When two or more layers are cut together using ultrasonic technology, the layers stick together. The strength of the weld is given by both the material and the geometry of the anvil. Numerous factors affect the speed at which fabric can be cut using ultrasonic technology. Some examples include the geometry of the...
Open the catalog to page 11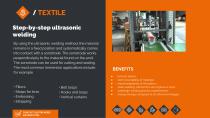
/ TEXTILE Step-by-step ultrasonic welding By using the ultrasonic welding method, the material remains in a fixed position and systematically comes into contact with a sonotrode. The sonotrode works perpendicularly to the material found on the anvil. The sonotrode can be used for cutting and sealing. The most common immersion applications include, for example • Filters • Straps for bras • Embossing • Strapping CONTACT US FOR MORE INFORMATION • Belt loops • Hooks and loops • Vertical curtains process speed 100% recyclability of materials interchangeability of the pattern clean welding,...
Open the catalog to page 12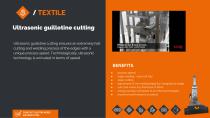
/ TEXTILE Ultrasonic guillotine cutting Ultrasonic guillotine cutting ensures an extremely fast cutting and welding process of the edges with a unique process speed. Technologically, ultrasonic technology is unrivaled in terms of speed. CONTACT US FOR MORE INFORMATION process speed edge welding - does not fray clean cutting adjustment of the welding edge by changing the angle cuts and welds any thickness of fabric energy savings compared to all other technologies maximum performanc
Open the catalog to page 13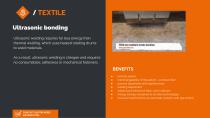
Ultrasonic bonding ULtrasonic welding requires far Less energy than thermaL weLding, which uses heated rotating drums to weld materials. As a result, ultrasonic welding is cheaper and requires no consumables, adhesives or mechanical fasteners. BENEFITS • process speed • interchangeability of the pattern - contrast roUer • process cleanliness and repetitiveness • welding adjustment • welds any thickness of fabric and multilayer • energy savings compared to aU other technologies • maximum performance on automatic systems with gap control
Open the catalog to page 14