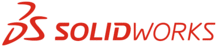

Catalog excerpts
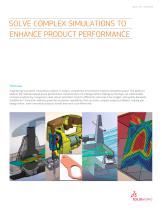
SOLVE COMPLEX SIMULATIONS TO ENHANCE PRODUCT PERFORMANCE Overview Engineering successful, innovative products in today’s competitive environment requires simulation power. The ability to analyze the multifaceted physical performance characteristics of a design before making a prototype can substantially increase productivity. Companies need robust simulation tools to efficiently overcome time, budget, and quality demands. SolidWorks® Simulation delivers powerful simulation capabilities that can solve complex analysis problems, helping you design better, more innovative products faster and more cost-effectively.
Open the catalog to page 1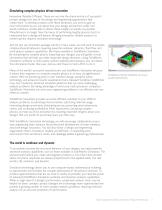
Simulating complex physics drives innovation Innovative. Reliable. Efficient. These are not only the characteristics of successful product designs but also of the design and engineering organizations that create them. To develop products with these attributes, you need to gain as much information as you can about how your design will perform under real world conditions, and be able to obtain these insights as quickly as possible. Manufacturers no longer have the luxury of performing lengthy physical tests to understand how a design will behave. Bringing innovative, reliable products to...
Open the catalog to page 2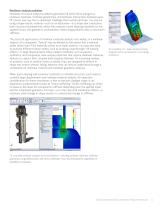
Nonlinear analysis problems Nonlinear structural analysis problems generally fall within three categories: nonlinear materials, nonlinear geometries, and nonlinear interactions between parts. Of course, you may face a simulation challenge that involves all three. You may be using a hyper-elastic material—such as an elastomer—in a shape that constitutes both structural nonlinearities, where the response varies disproportionately to the applied forces, and geometric nonlinearities, where displacements alter a structure’s stiffness. The practical applications of nonlinear materials analysis...
Open the catalog to page 3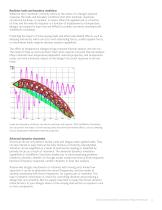
Nonlinear loads and boundary conditions While the term “nonlinear” primarily refers to the nature of a design’s physical response, the loads and boundary conditions that elicit nonlinear responses can also be nonlinear, or dynamic, in nature. When the applied load is a function of time, and the material response is a function of displacement or temperature, designs can respond in ways that are difficult to predict yet easily simulated with SolidWorks Simulation. Predicting the impact of time-varying loads and other load-related effects, such as damping and inertia, which can occur with...
Open the catalog to page 4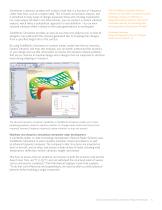
Sometimes a dynamics problem will involve a load that is a function of frequency rather than time, such as a shaker table. This is known as harmonic analysis, and is beneficial in many types of design, especially those with rotating components. For cases where the load is not deterministic, you can conduct a random vibration analysis, which takes a probabilistic approach to load definition. You can even simulate vibration effects related to the loads generated by an earthquake. “With SolidWorks Simulation Premium software, we were able to conduct structural and fatigue analyses to optimize...
Open the catalog to page 5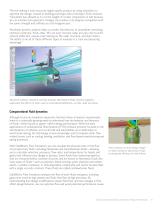
“We are making a more accurate, higher-quality product by using simulation to optimize the design, instead of building prototype after prototype,” Kriek stresses. “Simulation has allowed us to cut the weight of certain components in half because we can simulate how geometry changes can produce a 25 kilogram component with the same strength and stiffness as a 60 kilogram part. “Nonlinear dynamic analysis helps us predict the behavior of assemblies containing nonlinear materials,” Kriek adds. “We can even forecast radar accuracy due to windinduced deflection, uneven solar heating on the radar...
Open the catalog to page 6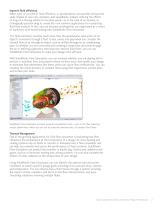
Improve fluid effieiency When most of us think of fluid efficiency, or aerodynamics, we typically envision the sleek shapes of race cars, airplanes, and speedboats. Indeed, reducing the effects of drag on a moving vehicle to increase speed—or in the case of an airplane, to strategically position drag to create lift—are common applications for conducting fluid flow analysis. In fact, you can simulate anything that you might learn as a result of expensive wind-tunnel testing with SolidWorks Flow Simulation. Yet, fluid mechanics involves much more than the aerodynamic interaction of an...
Open the catalog to page 7
The rapid growth in the development of products and appliances that leverage electronics creates an ideal scenario for using fluid flow simulation to study the effectiveness of cooling systems. With SolidWorks Flow Simulation you can evaluate how forced-air flow (fans) affects heat-producing electronic components. With this powerful tool you can apply real world heat loads and include heat sink emulators to quickly examine how you can modify the flow or the design to cool electronics more effectively. Instead of spending the time and expense required to prototype and test heating and...
Open the catalog to page 8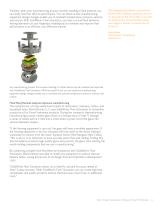
Similarly, when your manufacturing process involves handling a fluid material, you can study how flow affects performance. You can observe how manufacturing equipment design changes enable you to modulate temperature, pressure, velocity, and volume. With SolidWorks Flow Simulation, you have a virtual fluid dynamics testing laboratory at your fingertips, enabling you to simulate and improve flow performance in an efficient, cost-effective manner. “With integrated (SolidWorks software) FEA (finite element analysis) capabilities, we know our parts will not fail. This enables us to avoid the...
Open the catalog to page 9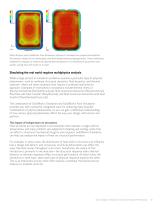
World Kitchen used SolidWorks Flow Simulation software to simulate the complex thermal/fluid flow physics related to its molten glass, thermoforming manufacturing operations. These simulations enabled the company to achieve the optimal thermal balance in its manufacturin processes more quickly, saving time and money as a result. Simulating the real world requires multiphysics analysis While a large portion of simulation problems examine a particular type of physical phenomena—such as nonlinear structural, dynamics, fluid dynamics, and thermal analyses—there are many situations that require...
Open the catalog to page 10All SOLIDWORKS Europe catalogs and technical brochures
-
SOLIDWORKS PCB CONNECTOR
2 Pages
-
BUSINESS INNOVATION
6 Pages
-
INDUSTRY INNOVATION
3 Pages
-
PROJECT PLANNER
2 Pages
-
SOLIDWORKS CAM
2 Pages
-
SOLIDWORKS Electrical 2017
6 Pages
-
SOLIDWORKS Simulation 2017
6 Pages
-
SOLIDWORKS Premium 2017
6 Pages
-
SOLIDWORKS PREMIUM
8 Pages
-
SOLIDWORKS ELECTRICAL SUITE
6 Pages
-
SOLIDWORKS PDM
4 Pages
-
SOLIDWORKS VISUALIZE
4 Pages
-
SOLIDWORKS COMPOSER 2015
4 Pages
-
SOLIDWORKS ELECTRICAL
4 Pages
-
SW2014 Datasheet Simulation
6 Pages
-
solidworks inspection
3 Pages
-
3DVIA Composer 2013
4 Pages
-
SolidWorks Premium
8 Pages
-
DESIGN TO PREVENT FATIGUE
8 Pages
-
EPDM Data Sheet
4 Pages
-
SOLIDWORKS SIMULATION
6 Pages
-
SolidWorks Plastics
4 Pages
-
3DVIA Composer - Data sheet
2 Pages