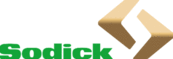

Catalog excerpts
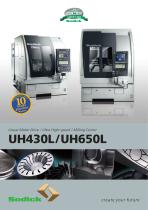
Linear Motor Drive / Ultra High-speed / Milling Center create your future
Open the catalog to page 1
UH430L UH650L Linear Motor Drive / Ultra High-speed / Milling Center Sodick started manufacturing high-speed milling machine to respond the customers’ demands to realise high-precision electrodes. After Sodick developed the world‘s first linear motor drive EDM, the company developed the MC180L, a machining center with linear motor drive, in 2001. In 2007, Sodick launched the best selling linear motor drive milling machine range „HS Series“ which specialized in high-speed milling, aiming to achieve an unrivaled high accuracy and advanced surface quality. NC Electrode Milling Machine APM...
Open the catalog to page 2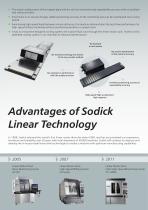
The simple configuration of the magnet plate and the coil unit maintains high repeatability accuracy with no backlash and without friction. Since there is no secular change, stable positioning accuracy of the machining axes can be maintained over a long period. Even during high-speed feeds between minute distances, this machine demonstrates the best drive performance for high-speed milling machining without positioning deviation or speed errors. It has an innovative designed cooling system; the coolant fluid runs through the linear motor coils. Thanks to this patented cooling system, it can...
Open the catalog to page 3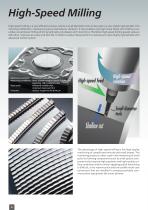
High-Speed Milling High speed milling is a very efficient process, where a small diameter tool can be used in a very stable rigid spindle. This minimizes deflection, improves accuracy and reduces vibration. It also enables very high linear feeds with shallow cuts, unlike conventional milling which dynamically cuts deeper with more force. Therefore high speed milling greatly reduces distortion, improves accuracy and tool life. In order to realise these points it is necessary to have highly rigid spindle with advanced control system. Machining material: Cemented carbide Machining conditions:...
Open the catalog to page 4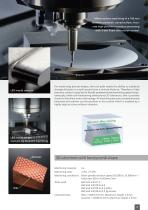
Mirror surface machining of a 100 mm diameter parabolic curved surface. Accurate high-precision curvature processing with 3-axis linear and motion control. For machining precise shapes, the tool path needs the ability to suddenly change direction in a split second over a minute distance. Therefore a high precision control is required to handle predetermined machining speed instantaneously, while still maintaining dimensional 3D tolerances, that is possible thanks to the linear motor technology. All machining axes are comprehensively balanced with perfect synchronization in the control which...
Open the catalog to page 5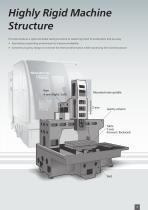
Highly Rigid Machine Structure UH series features a rigid and stable casting structure to realise high level of acceleration and accuracy Spontaneous operating environment to improve workability Symmetrical gantry design to minimise the thermal deformation while maximising the machine posture Ram X-axis (Right / Left) Mounted main spindle Gantry column Table Y-axis (Forward / Backward)
Open the catalog to page 7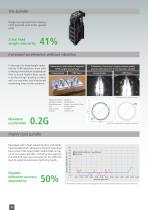
Unique Unique cooling system that cooling system The Spindle system that Unique cooling system that Unique cooling that suppress heat generation suppress heat generation suppress heat generation suppress heat generation Suppresses Suppresses heat generation linear motor with a with a heat generation of the of the linear motor Suppresses heat generation of of the linear motor with a Suppresses heat generation the linear motor with a employs proprietary Weight method ofof directlythat unit.coil unit. unit. Thermal method of saving head cooling theThermal Thermal proprietary directly cooling...
Open the catalog to page 8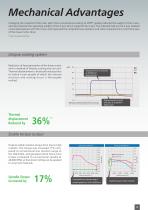
Changing the material of the main parts from conventional casting to CFRP* greatly reduced the weight of the Z-axis, and also reduced the operating weight of the X-axis which supports the Z-axis. The reduced load on the X-axis realized a favorable balance with the Y-axis, and improved the comprehensive dynamic and static characteristics of all three axes of the linear motor drive. *Carbon Fibre Reinforced Plastic Unique cooling system Changing the material of the main parts from conventional casting to CFRP greatly reduced the weight of the Z-axis, and of the Reduction cooling system...
Open the catalog to page 9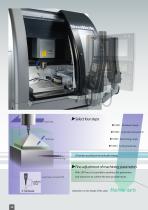
►Select four steps ► STEPI Residual margin ► STEP2 Length below tool head (L/D) ► STEP3 Machining range ► STEP4 Cutting feed rate Q Number according to the tool path strategy ►Fine adjustment of machining parameters Length below tool head (L/D) With SEPTune, it is possible to optimise the parameters and tolerances to achieve the best possible result. L: Length below the heed Q Number is in the header of NC codes
Open the catalog to page 10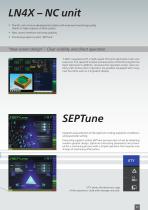
Developed and manufactured by Sodick ・ The NC unit in-house developed by Sodickby speeding up drive system servo response Improved machining quality with improved machining quality ・ ・New control interface with easy usability increased New interface with usability thanks to high response of drive system ・ ・Processing support system "SEPTune" "SEPTune" Processing support system "New screen design" “New screen design” – Clear visibility and direct operation Clear visibility and direct operation "LN 4X" equipped with a high-speed CPU and optimized "LN4X" equipped The speed of analysis and...
Open the catalog to page 11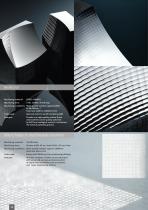
Machining time: 3 Hrs. 30 Min. (Finishing) Machining conditions: Main spindle rotation speed 20,000 to 40,000min-1 Feed rate 4,000 to 2,000mm/min Tools used: Ball end mill R1.5 to R0.5 Finishing CBN Features: Thanks to a high-quality surface finish and excellent corner quality achieved by SEPTune intelligent control, it minimises the need of polishing process. Tools used: Center drill $0.08 mm (for positioning/drilling) Features: Multiple numbers of holes can be machined with advanced accuracy and precise pitch in highly hard workpiece such as ceramics and super engineering plastics....
Open the catalog to page 12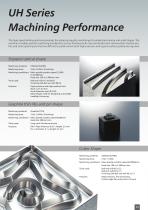
UH Series Machining Performance The high-speed milling machining realises the advanced quality machining of complicated minute and small shapes. The machine is widely used for machining mould parts such as forming multi-core connectors with narrow pitch and low profile, and small optical parts that are difficult to polish where both high precision and superb surface quality are required. Stepped optical shape Machining material: STAVAX (52HRC) Machining time: 5 Hrs. 29 Min. (Finishing) Machining conditions: Main spindle rotation speed 22,000 to 40,000min-1 Feed rate 350 to 3,000mm/min Tools...
Open the catalog to page 13All Sodick catalogs and technical brochures
-
ALC Series
24 Pages
-
Linear Product Range 2019
28 Pages
-
HS430L
2 Pages
-
HS650L
2 Pages
-
AQ1200L Premium
2 Pages
-
AQ900L Premium
2 Pages
-
OPM250L
24 Pages
-
Produkt Range Brochure
28 Pages
-
ALC600G
2 Pages
-
ALC400G
2 Pages
-
OPM350L
2 Pages
-
AP250L
2 Pages
-
AQ1500L
2 Pages
-
AQ1200L
2 Pages
-
AQ750L
2 Pages
-
SLC600G
2 Pages
-
SLC400G
2 Pages
-
AP3L
2 Pages
-
AQ15L
2 Pages
-
AG100L
2 Pages
-
AG80L LST
2 Pages
-
AG40L
2 Pages
-
AD35L
2 Pages
-
AP1L
2 Pages
-
K1C/K3HN
4 Pages
-
VL400Q/VL600Q
4 Pages
-
Linear Product Range
24 Pages
-
AG80L LST / AG100L
4 Pages
-
AQ15L / AQ20L
4 Pages
-
AG40L/AG60L/AG80L
16 Pages
-
AD35L / AD55L
4 Pages
-
ad55l
2 Pages
-
aq20l
2 Pages
-
AP250 L
6 Pages
-
SLC-G Series
8 Pages
-
VZ300L/VZ500L
6 Pages
-
Linear EDM Range
20 Pages
Archived catalogs
-
AP1L/AP3L
8 Pages
-
Linear Motor EDM AD35L
4 Pages
-
SLG
8 Pages
-
SLQ
2 Pages
-
AQ400L
8 Pages
-
VZ300L
2 Pages
-
AQ45L
6 Pages
-
AD30L
6 Pages
-
Product Range
6 Pages
-
Sodick - Linear Motor Wire EDM
13 Pages
-
Sodick - Linear Motor Sinker EDM
12 Pages
-
Sodick - High Speed Hard Milling
22 Pages
-
Sodick - Small Hole EDM
6 Pages