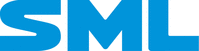
Catalog excerpts
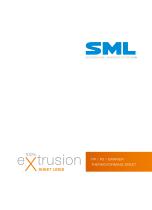
EXTRUSION LINES - ENGINEERED TO PERFORM ► SHEET LINES THERMOFORMING SHEET
Open the catalog to page 1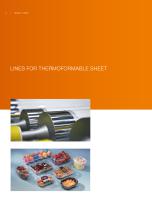
SHEET lines LINES FOR THERMOFORMABLE SHEET
Open the catalog to page 2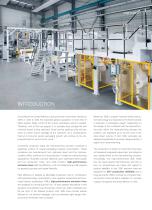
sheet lines INTRODUCTION According to the United Nations, food production must nearly double by 2050 in order to feed the expected global population of more than 9 billion people. Sadly, a third of the current worldwide output is wasted. Therefore, one of the key targets is to increase food storage life and minimize losses during shipment. Small service packing units will also serve to further reduce spoilage at the costumer. As a consequence, food and consumer goods packaging growth will continue to be disproportionate for some time to come. Containers produced using the thermoforming...
Open the catalog to page 3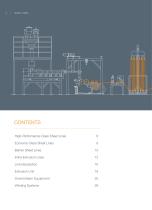
High-Performance Class Sheet Lines 6 Economy Class Sheet Lines 8 Barrier Sheet Lines 10 Inline Extrusion Lines 12
Open the catalog to page 4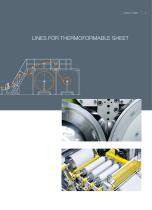
sheet lines LINES FOR THERMOFORMABLE SHEET
Open the catalog to page 5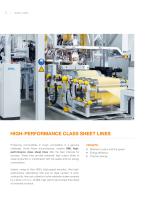
sheet lines HIGH-PERFORMANCE CLASS SHEET LINES Producing commodities in tough competition is a genuine challenge. Under these circumstances, modern SML highperformance class sheet lines offer the best chances for success. These lines provide extremely high output levels of sheet production in combination with top quality and low energy consumption. Indeed, owing to their HSE’s (high-speed extruder), their highperformance calendering rolls and an ideal number of postcooling rolls, they can outperform other relatively modern systems by a factor of 2 to 4. All SML high-performance sheet lines...
Open the catalog to page 6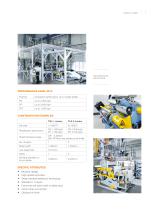
sheet lines high performance line for PP/PS Performance level 2013: Polymer production performance (at 1m sheet width) CONFIGURATION EXAMPLES: TSL-1 Jumbo Plastification perfomance Sheet thickness range 200 - 2,500µm (thin PP films may require an air knife) Sheet width Line speed limit Winding diameter on 6-inch shafts SPECIFIC ATTRIBUTES: ¡ ¡ ¡ ¡ ¡ ¡ ¡ Modular design High-speed extruders Easily handled feedblock technology Standard 1-3 layers Horizontal roll stack (with multiple nips) Quick ramp-up function Optional air kni
Open the catalog to page 7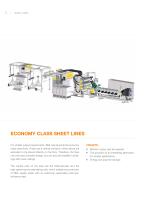
sheet lines ECONOMY CLASS SHEET LINES For smaller output requirements, SML has launched its economy class sheet lines. These use a vertical roll stack, which allows the extruders to be placed directly on the floor. Therefore, the lines not only have a simpler design, but can also be installed in buildings with lower ceilings. The central units of the lines are the HSE-extruder and the high-performance calendering rolls, which enable the production of SML quality sheet with an extremely reasonable price-performance ratio. Medium output and line speeds The provision of an interesting...
Open the catalog to page 8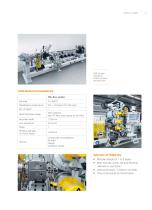
sheet lines HSE extruder module for vertical roll stack extrusion lines CONFIGURATION EXAMPLES: TSL-Eco Jumbo Extruder Plastification perfomance Sheet thickness range 200-2,500µm (thin PP films may require an air knife) Line speed limit Winding diameter on 6-inch shafts Co-extruder and feedblock Air knife Gauge Cantilever winder SPECIFIC ATTRIBUTES: ¡ Modular design for 1 to 5 layers ¡ Main extruder, pump, die and electrical cabinets on one frame ¡ Vertical roll stack, 1,200mm roll width ¡ One control panel on the rol
Open the catalog to page 9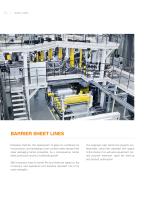
sheet lines Barrier sheet lines Extended shelf life, the replacement of glass for containers for fruit products, and spreading of pre-cooked meals demand first class packaging barrier properties. As a consequence, barrier sheet production shows a worldwide growth. SML’s extrusion lines for barrier film and sheet are based on the company’s vast experience and therefore represent one of its major strengths. Our engineers plan barrier line projects professionally, using their expertise with regard to the choice of co-extrusion equipment, correct polymer treatment, rapid line start-up and...
Open the catalog to page 10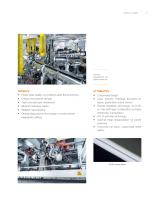
sheet lines extruder arrangement of a barrier sheet line TargetS: ¡ Finest sheet quality, no problems after thermoforming ¡ Energy and polymer savings ¡ Tight and safe layer distribution ¡ minimal multi-layer waste ¡ Skeleton reprocessing ¡ Outstanding polymer flow design to avoid polymer degradation effects Attributes: ¡ customized design ¡ Layer security: individual extruders for layers, gravimetric output control ¡ flexible feedblock technology: 5L/7L/9L or more with layer configuration and layer distribution manipulation ¡ HO-LT extruder technology ¡ Optional edge encapsulation for...
Open the catalog to page 11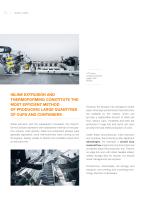
sheet lines I-TF3 inline compact extrusion system with HSE90 Inline extrusion and thermoforming constitute the most efficient method of producing large quantities of cups and containers Sheet extrusion and the subsequent conversion into thermoformed articles represent well-established methods in the plastics industry. Until recently, these two production phases were generally separated, since thermoformers were running at low throughput, beeing unable to absorb the complete output from an extrusion line. However, the situation has changed in recent years. Now high-performance thermoformers...
Open the catalog to page 12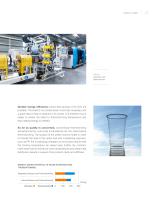
sheet lines I-TF2 in operation with thermoformer Greater energy efficiency means that savings of 20-25% are possible. The sheet is not cooled down more than necessary and a great deal of heat is retained in its center. It is therefore much easier to reheat the sheet to thermoforming temperature and less heating energy is needed. As far as quality is concerned, conventional thermoforming demands that far more heat is transferred into the sheet before thermoforming. The surface of the sheet must be hotter in order to transfer the heat to the center and with crystallizing polymers, such as PP,...
Open the catalog to page 13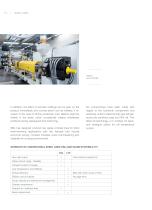
sheet lines In addition, the effect of extrusion settings can be seen on the product immediately and counter-action can be initiated, if required. In the case of off-line production such defects might be hidden in the sheet, which occasionally creates unforeseen problems during subsequent thermoforming. SML has designed a brand new series of sheet lines for inline thermoforming applications with key features that include economic pricing, compact modules, quick commissioning and suitability for a tropical environment. No compromises have been made with regard to the functional components...
Open the catalog to page 14All SML Maschinengesellschaft catalogs and technical brochures
-
HYGIENE FILM
14 Pages
-
STRETCH WRAP
18 Pages
-
PP / PE / PET BARRIER FILM
17 Pages
-
COATING LINES
2 Pages
-
AUSTROFIL - BCF MULTIFILAMENT
32 Pages
-
PET / R-PET SHEET
28 Pages
-
CAST FILM LINES
32 Pages
-
austrofil HT/MT version
2 Pages
-
SERIES W4000 CAST
2 Pages
-
SERIES ECOFLEX / POWERFLEX
2 Pages
-
CPP EXTRUSION
2 Pages
-
high performance extruder
2 Pages
-
smile control system
2 Pages
-
winder series W3000 cast
2 Pages
-
winder 2000
2 Pages
-
SML
15 Pages
-
Spinning lines
16 Pages
-
Coating lines
12 Pages
-
Sheet lines
9 Pages
-
Cast film lines
20 Pages