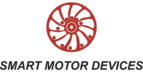

Catalog excerpts
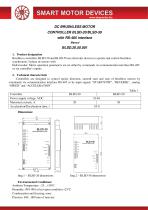
DC BRUSHLESS MOTOR CONTROLLER BLSD-20/BLSD-50 with RS-485 interface Manual BLSD.20.50.001 1. Product designation Brushless controllers BLSD-20 and BLSD-50 are electronic devices to operate and control brushless synchronous 3-phase dc motors with Hall encoder. Motor operation parameters are set either by commands via communication interface RS-485 or via controller’s inputs. 2. Technical characteristic Controllers are designed to control speed, direction, smooth start and stop of brushless motors by commands via communication interface RS-485 or by input signals “START/STOP”, “REVERSE”, .analog “SPEED” and “ACCELERATION”. Table 1 Controller Power supply voltage, VDC Maximum current, A Acceleration/Deceleration time, s Environmental Conditions: Ambient Temperature: -25…+50°C Humidity: 90% RH or less upon condition +25°C Condensation and freezing: none Pressure: 650…800 mm of mercury
Open the catalog to page 1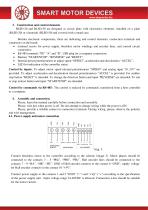
3. Construction and control elements BLSD-20 and BLSD-50 are designed as circuit plate with electronics elements, installed on a plate (BLSD-20) or a heatsink (BLSD-50) and covered with a metal case. Besides electronic components, there are indicating and control elements, connection terminals and connectors on the board: · terminal screws for power supply, brushless motor windings and encoder lines, and control circuit connection; · RS-485 terminals “PE” “A” and “B”. USB plug for a computer connection; · Buttons “START/STOP”, “REVERSE” and “RESET”; · Internal preset potentiometers to...
Open the catalog to page 2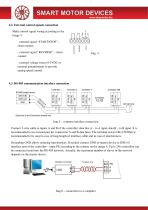
4.2. External control signals connection Make control signal wiring according to the image 4. - external signal “START/STOP” – clean contact; - external signal “REVERSE” – clean contact; - external voltage source 0-5VDC or external potentiometer to provide analog speed control. 4.3. RS-485 communication interface connection Img.5 – common interface connection Connect 2-wire cable to inputs A and B of the controller: data line A – to A input, data B – to B input. It is recommended to use twisted pair for connection A and B data lines. The terminal resistor Rt=120 Ohm is recommended to be...
Open the catalog to page 3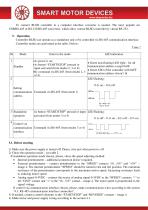
To connect BLSD controller to a computer interface converter is needed. The most popular are USB/RS-485 or RS-232/RS-485 converters, which allow control BLSD controller by virtual RS-232. 5. Operation Controller BLSD can operate as a standalone unit or be controlled via RS-485 communication interface. Controller modes are performed in the table 2 below: Table 2 № Enter to the mode · As power is on; · As button “START/STOP” pressed or input activated (from modes 2, 3 or 4); · By command via RS-485 (from modes 2, 3 or 4). LED indication · Green non-flashing LED light - for all communication...
Open the catalog to page 4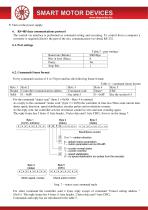
5) Turn on the power supply. 6. RS-485 data communications protocol The control via interface is performed as command setting and executing. To control from a computer a converter is required (doesn’t the part of the set), communication via virtual RS-232. 6.1. Port settings Baud rate (Bitrate) Bits in byte (Data) Parity Stop Bits Table 3 - port settings: 9600 Bps 8 No 1 6.2. Commands frame format Every command consists of 4 or 5 bytes and has the following frame format: Byte 1 Byte 2 Header Controller communication address 0xE6 0 – 0xFF Byte 3 Command code See table 5 Table 4 – command...
Open the catalog to page 5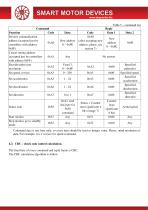
Table 5 – command list Command Function Code Set new communication address (accepted just by 0хА0 controllers with address 0xFF) Cancel setting address (accepted just by controllers 0хА1 with address 0xFF) Encoder pulses per 0хА2 revolution Set speed, rev/sec 0хА3 Code 0хА0 (after accepting new address, please, see section 7) Reply Data 1 New address 0 – 0xFE Status scan Start motion Stop motion, go to standby mode Don’t send this byte for 0x50 command Any Counter least significant 8 bits 0х00 Status + Counter most significant 4 bits (image 7) Specified pulses/rev Specified speed Specified...
Open the catalog to page 6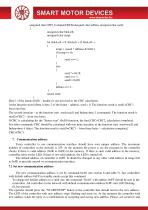
unsigned char OWI_ComputeCRC8(unsigned char inData, unsigned char seed) { unsigned char bitsLeft; unsigned char temp; for (bitsLeft = 8; bitsLeft > 0; bitsLeft--) { temp = ((seed ^ inData) & 0x01); if (temp == 0) { seed >>= 1; } else { seed ^= 0x18; seed >>= 1; seed |= 0x80; } inData >>= 1; } return seed; } Byte 1 of the frame (0xE6 – header) is not involved to the CRC calculation. At the function start inData is byte 2 of the frame – address, seed = 0. The function result is seed1=CRC1 from one byte. The second iteration – at the function start seed=seed1 and Indata=byte 3 (command). The...
Open the catalog to page 7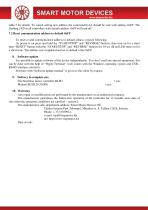
table 5 for details. To cancel setting new address the command 0xA1 should be sent with address 0xFF. The flashing LED at all controllers with default address 0xFF will turn off. 7.2 Reset communication address to default 0xFF To reset a valid communication address to default, please, execute following: As power is on press and hold the “START/STOP” and “REVERSE” buttons, then turn on for a short time “RESET” button; hold the “START/STOP” and “REVERSE” buttons for 10 sec till red LED turns on for a short time. The address rest completed and set to default value 0xFF. 8. Software update It...
Open the catalog to page 8All Smart Motor Devices catalogs and technical brochures
-
Smart Motor Devices 2021 catalog
14 Pages
Archived catalogs
-
Smart Motor Devices 2021
21 Pages
-
DC brush motors
4 Pages