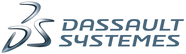
Catalog excerpts
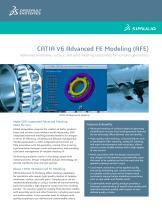
CATIA V6 Advanced FE Modeling (AFE) Advanced wireframe, surface, and solid meshing capabilities for complex geometries CATIA V6 Advanced FE Modeling Make CAD-Integrated Advanced Meshing Work for You Global competition requires the creation of better products faster and at lower costs without sacrificing quality. CADintegrated advanced meshing provides benefits for analysts in terms of efficiency, reliability and lifecycle management. Meshes generated in a CAD-integrated environment are fully associative with the geometry—saving time, ensuring synchronization between mesh and geometry, and providing consistent management of valuable meshing IP. Performing simulation earlier in the design phase with industry-proven, design-integrated analysis technology can provide significant time and cost savings. About CATIA V6 Advanced FE Modeling CATIA Advanced FE Modeling offers meshing capabilities for specialists who require high-quality meshes of complex wireframe, surface, and solid parts. Complex parts can be meshed automatically or using a number of manual meshing tools that provide a high degree of control over the meshing process. The solution supports creating finite element models with assembly joints and other fasteners, including spot seam and surface welds. It also provides tools to analyze mesh quality according to pre-defined and customizable criteria. Features & Benefits • Advanced meshing of surfaces based on geometry simplification ensures that small geometric features do not adversely affect element size and quality. • High-quality solid meshing, using techniques such as tetrahedron filler meshing, sweep 3D meshing, and mesh transformation and extrusions, allows users to create reliable meshes with a high degree of user control. • Mesh associative with the design ensures that any changes to the geometry automatically cause the mesh to be updated so that the mesh and the geometry always remain in sync. • Local mesh constraints can be applied quickly and easily facilitating user control over meshes on complex surface parts and to impose mesh constraints required when modeling connections, such as spot welds and flexible joints. • Customizable mesh quality analysis provides a thorough understanding of overall mesh quality and individual element quality with respect to userdefined quality criteria.
Open the catalog to page 1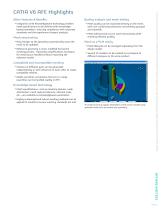
mesh specifications to be defined with knowledgebased parameters, ensuring compliance with corporate standards and the experience of expert analysts. Mesh associativity • Any changes to the geometry automatically cause the mesh to be updated. • Reference geometry is never modified during the meshing process. Geometry simplifications necessary for meshing are handled without impacting the reference model. Quality analysis and mesh editing • Mesh quality can be visualized directly on the mesh, with non-conforming elements conveniently grouped and viewable. • Mesh editing tools can be used...
Open the catalog to page 2Archived catalogs
-
Opera
12 Pages
-
ABAQUS/STANDARD 2017
3 Pages
-
ABAQUS/CAE 2017
4 Pages
-
XFlow 2019x
2 Pages
-
XFlow
6 Pages
-
CST STUDIO SUITE® 2017
32 Pages
-
SIMULIA
28 Pages
-
Isight
6 Pages
-
fe-safe
6 Pages
-
ABAQUS UNIFIED FEA
6 Pages
-
SIMULIA V5-6R2016
6 Pages
-
SIMULIA V6R2013x_2012
7 Pages
-
EN O V IA V 6R 2013x
12 Pages
-
power of CATIA
1 Pages
-
DraftSight support options
1 Pages
-
SIMULIA V6R2013x_2015
4 Pages
-
CATIA for Creative Designers
9 Pages
-
CATIA ICEM AEROEXPERT
5 Pages
-
CATIA ICEM SHAPE DESIGN
5 Pages
-
CATIA Surface FE Modeling
2 Pages
-
CATIA Structural Analysis
2 Pages
-
SIMULIA Execution Engine
2 Pages
-
Isight 5.8
3 Pages
-
SIMULIA DesignSight Thermal
2 Pages
-
SIMULIA V6R2013
6 Pages
-
Abaqus for CATIA V5
6 Pages
-
SIMULIA ExSight
2 Pages
-
CATIA ELECTRICAL SOLUTIONS
8 Pages
-
SIMULIA
6 Pages
-
Abaqus 6.8
8 Pages