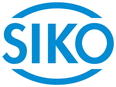

Catalog excerpts
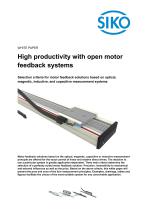
WHITE PAPER High productivity with open motor feedback systems Selection criteria for motor feedback solutions based on optical, magnetic, inductive, and capacitive measurement systems Motor feedback solutions based on the optical, magnetic, capacitive or inductive measurement principle are offered for the exact control of linear and rotative direct drives. The decision to use a particular system is greatly application-dependent. Three main criteria determine the selection of a perfectly suited motor feedback solution: Precision, insensitivity to mechanical and external influences as well as the price. Based on the above criteria, this white paper will present the pros and cons of the four measurement principles. Examples, drawings, tables and figures facilitate the choice of the most suitable system for any conceivable application.
Open the catalog to page 1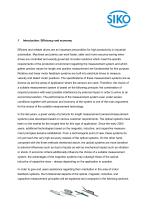
Introduction: Efficiency and economy Efficient and reliable drives are an important precondition for high productivity in industrial automation. Machines and plants can work faster, safer and more resource-saving when drives are controlled and exactly governed. Encoder solutions which meet the specific requirements of the production environment regarding the measurement system and which gather precise values for length and position measurement are fundamental for this purpose. Rotative and linear motor feedback systems are built into electrical drives to measure velocity and detect motor...
Open the catalog to page 4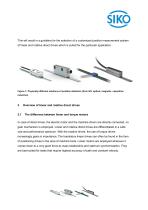
This will result in a guideline for the selection of a customized position measurement system of linear and rotative direct drives which is suited for the particular application. Figure 1: Physically different solutions of position detection (from left: optical, magnetic, capacitive, inductive) Overview of linear and rotative direct drives The difference between linear and torque motors In case of direct drives, the electric motor and the machine driven are directly connected, no gear mechanism is employed. Linear and rotative direct drives are differentiated in a wide size and performance...
Open the catalog to page 5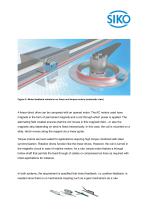
Figure 2: Motor feedback solutions on linear and torque motors (schematic view) A linear direct drive can be compared with an opened motor. The AC motors used have magnets in the form of permanent magnets and a coil through which power is applied. The alternating field created ensures that the coil moves in this magnetic field – or also the magnetic strip depending on what is fixed mechanically. In this case, the coil is mounted on a slide, which moves along the magnet via a linear guide. Torque motors are best suited for applications requiring high torque combined with ideal...
Open the catalog to page 6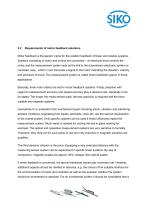
Requirements of motor feedback solutions Motor feedback is the generic name for the position feedback of linear and rotative systems. Systems consisting of motor and control are concerned – an electrical drive controls the motor and the measurement system acts as the link to the downstream electronic system or controller, resp., which in turn transmits a signal to the motor indicating the direction, velocity and precision of travel. The measurement system is called motor feedback system in these applications. Basically, three main criteria are set for motor feedback systems: Firstly,...
Open the catalog to page 7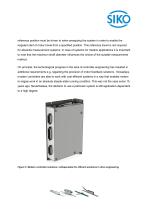
reference position must be driven to when energizing the system in order to enable the targeted start of motor travel from a specified position. This reference travel is not required for absolute measurement systems. In case of systems for rotative applications it is important to note that the maximum shaft diameter influences the choice of the suitable measurement method. On principle, the technological progress in the area of controller engineering has resulted in additional requirements e.g. regarding the precision of motor feedback solutions. Nowadays, modern controllers are able to...
Open the catalog to page 8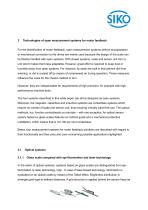
Technologies of open measurement systems for motor feedback For the identification of motor feedback, open measurement systems without encapsulation or mechanical connection to the drives are mainly used because the design of the scale can be flexibly handled with open systems. With closed systems, scale and sensor unit form a unit which makes them less adaptable. However, great effort is required to keep dust or humidity away from open systems. For instance, lip seals are built in that prevent dirt from entering or dirt is sucked off by means of compressed air during operation. These...
Open the catalog to page 9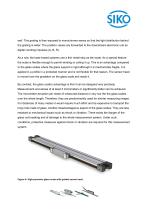
well. This grating is then exposed to monochrome waves so that the light distribution behind the grating is wider. The position values are forwarded to the downstream electronic unit as digital counting impulses (A, B, R). As a rule, the laser-based systems use a thin metal strip as the scale. As a special feature the scale is flexible enough to permit winding or coiling it up. This is an advantage compared to the glass scales where the glass support is rigid although it is mechanically fragile. It is applied in a profile in a protected manner and is not flexible for that reason. The sensor...
Open the catalog to page 10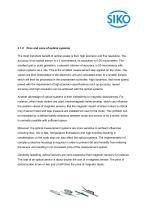
Pros and cons of optical systems The most important benefit of optical scales is their high precision and fine resolution. The accuracy of an optical sensor is ± 5 micrometers, its resolution is 0.05 micrometers. The smallest grid or scale gradation, a relevant criterion of accuracy, is 20 micrometers with optical systems as a rule. This is the smallest measurement step applied on the scale. The values are then interpolated in the electronic unit and calculated down to a smaller division which will then be processed in the downstream controller. High dynamics, fast travel speed, paired with...
Open the catalog to page 11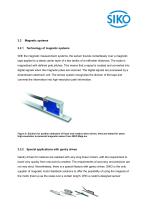
Magnetic systems Technology of magnetic systems With the magnetic measurement systems, the sensor travels contactlessly over a magnetic tape applied to a steely carrier layer of a few tenths of a millimeter thickness. The scale is magnetized with defined pole pitches. This means that a signal is created and converted into digital signals when the magnetic poles are scanned. The digital signals are processed by a downstream electronic unit. The sensor system recognizes the division of the tape and converts the information into high-resolution path information. Figure 5: Solution for position...
Open the catalog to page 12All SIKO GmbH catalogs and technical brochures
-
MSAC200
5 Pages
-
Absolute encoder WV5800M
4 Pages
-
Quick Size Changeover
8 Pages
-
Reduction sleeve RH
2 Pages
-
DriveLine | Actuators
88 Pages
-
MagLine | Product Overview
20 Pages
-
SIKO | Quick Size Changeover
8 Pages
-
SIKO | Product Overview
20 Pages
-
SIKO | Mobile Automation
10 Pages
-
PositionLine | Position Indicators
152 Pages
-
SIKO | We Retrofit!
8 Pages
-
RotoLine | Rotary Encoders
118 Pages