
Catalog excerpts
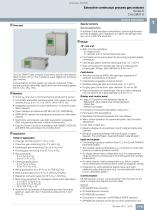
Extractive continuous process gas analysis Series 6 CALOMAT 6 General information Special versions Special applications In addition to the standard combinations, special applications are also available upon request (e.g. higher sample gas pressure up to 2 000 hPa absolute). ■ Design 19" rack unit • With 4 HU for installation - In hinged frame - In cabinets with or without telescope rails • Front plate can be swung down for servicing purposes (laptop connection) • Internal gas paths: stainless steel pipe (mat. no. 1.4571) • Gas connections for sample gas inlet and outlet and for purging gas: fittings, pipe diameter of 6 mm or ¼" The CALOMAT 6 gas analyzer is primarily used for quantitative determination of H2 or He in digital or quasi-digital non-corrosive gas mixtures. Concentrations of other gases can also be measured if their thermal conductivities differ significantly from the residual gases like Ar, CO2, CH4, NH3. ■ Benefits • Small T90 time due to micromechanical-produced Si sensor • Universally applicable hardware basis, high measuring range dynamics (e.g. 0 to 1 %, 0 to 100 %, 95 to 100 % H2) • Integrated correction of cross-interference, no external calculation required • Open interface architecture (RS 485, RS 232, PROFIBUS) • SIPROM GA network for maintenance and service information (option) • Electronics and physics: gas-tight separation, purgeable, IP65, long service life even in harsh environments • Ex(p) for Zones 1 and 2 (in accordance with 94/9/EC (ATEX 2G and ATEX 3G), and Class I Div 2 (CSA) Ex(n) ■ Application Fields of application • Pure gas monitoring (0 to 1 % H2 in Ar) • Protective gas monitoring (0 to 2 % He in N2) • Hydroargon gas monitoring (0 to 25 % H2 in Ar) • Forming gas monitoring (0 to 25 % H2 in N2) • Gas production: - 0 to 2 % He in N2 - 0 to 10 % Ar in O2 • Chemical applications: - 0 to 2 % H2 in NH3 - 50 to 70 % H2 in N2 • Wood gasification (0 to 30 % H2 in CO/CO2/CH4) • Blast furnace gas (0 to 5 % H2 in CO/CO2/CH4/N2) • Bessemer converter gas (0 to 20 % H2 in CO/CO2) • Monitoring equipment for hydrogen-cooled turbo-alternators: - 0 to 100 % CO2/Ar in air - 0 to 100 % H2 in CO2/Ar - 80 to 100 % H2 in air • Versions for the analysis of flammable and non-flammable gases or vapors for use in hazardous areas (Zone 1 and Zone 2) Field device • Two-door enclosure (IP65) with gas-tight separation of analyzer and electronics sections • Individually purgeable enclosure halves • Stainless steel gas path and stubs (mat. no. 1.4571) • Purging gas connections: pipe diameter 10 mm or 3/8" • Gas connections for sample gas inlet and outlet: clamping ring connection for a pipe diameter of 6 mm or ¼" Display and control panel • Large LCD panel for simultaneous display of: - Measured value (digital and analog displays) - Status bar - Measuring ranges • Contrast of LCD panel adjustable using menu • Permanent LED backlighting • Washable membrane keyboard with five softkeys • Menu-driven operation for parameterization, test functions, adjustment • User help in plain text • Graphic display of concentration trend; programmable time intervals • Bilingual operating software German/English, English/ Spanish, French/English, Spanish/English, Italian/English Input and outputs • One analog output per medium (from 0, 2, 4 to 20 mA; NAMUR parameterizable) • Two analog inputs configurable (e.g. correction of cross-interference or external pressure sensor) • Six digital inputs freely configurable (e.g. for measurement range switchover, processing of external signals from sample preparation) • Six relay outputs, freely configurable (e.g. failure, maintenance demanded, threshold alarm, external magnetic valves) • Expansion by eight additional digital inputs and eight additional relay outputs each (e.g. for autocalibration with up to four calibration gases) Communication RS 485 present in basic unit (connection from the rear; for the slide-in module also behind the front plate). Options • RS 485/RS 232 converter • RS 485/Ethernet converter • RS 485/USB converter • Connection to networks via PROFIBUS DP/PA i
Open the catalog to page 1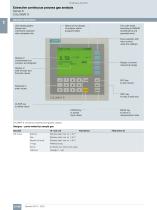
Extractive continuous process gas analysis Series 6 CALOMAT 6 General information LED backlit graphic display and membrane keyboard with noticeable click Status line for display of analyzer status (programmable) Two code levels according to NAMUR (maintenance and specialist level) Easy operation with menu control using five softkeys Display of concentrations as numbers and bargraph Display of current measuring ranges Display of start-of-scale and full-scale values ESC key to abort inputs Keyboard to enter values INFO key for help in plain text CLEAR key to delete inputs ENTER key to accept...
Open the catalog to page 2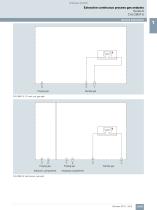
Extractive continuous process gas analysis Series 6 CALOMAT 6 General information CALOMAT 6, 19" rack unit, gas path CALOMAT 6, field device, gas path
Open the catalog to page 3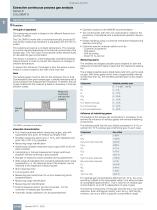
Extractive continuous process gas analysis Series 6 CALOMAT 6 General information ■ Function Principle of operation The measuring principle is based on the different thermal conductivity of gases. The CALOMAT 6 works with a micromechanically produced Si chip whose measuring membrane is equipped with thin-film resistors. The resistors are kept at a constant temperature. This requires an current intensity depending on the thermal conductivity of the sample gas. This "raw value" is processed further electronically to calculate the gas concentration. The sensor is located in a...
Open the catalog to page 4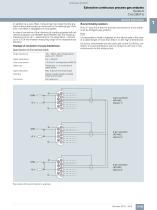
Extractive continuous process gas analysis Series 6 CALOMAT 6 General information In addition to a zero offset, it should also be noted that the gradient of the characteristic is influenced by the residual gas. However, this effect is negligible for most gases. In case of correction of the influence of interfering gases with additional analyzers (ULTRAMAT 6/ULTRAMAT 23), the resulting measuring error can – depending on the application – amount up to 5 % of the smallest measuring range of the respective application. Example of correction of cross-interference Specification for the interface...
Open the catalog to page 5All Siemens Process Analytics catalogs and technical brochures
-
Process Analytical Instruments
452 Pages
Archived catalogs
-
Process Analytical Instruments 2018
450 Pages
-
Process Analytical Instruments
470 Pages