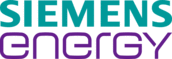

Catalog excerpts
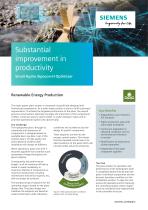
Substantial improvement in productivity Small Hydro Sipocon-H Optimizer Renewable Energy Production The hydro power plant system is composed of specifically designed and harmonized components. As a tailor-made solution it aims to fulfill customers’ requirements. To achieve the targeted performance of the plant, the overall process control system optimally manages the interaction of the components. It offers numerous ways to select modes, to switch between states and to prioritize operational aspects also dynamically. Consequently, key performance targets, such as maximum efficiency based on water availability or maximum lifetime of components or maximum productivity including maintenance and service aspects, etc., will not always be achieved. The standard array of setpoints for the operating range is based on the plant design data. The plant design and therefore the setpoints are based on scaled model tests under laboratory These setpoints are fed into the process control system. This means that the standard control loop is for ideal conditions of the plant which will not exist under actual circumstances. • Adaptability to your Siemens PLC hardware • Higher production rates with same water availability • Continuous adaptation to changing conditions such as environmental influences or erosion • Identification of weak points of plant operation • Independent from plant component suppliers When operating a plant over time it becomes apparent that conditions and parameters change throughout the plant’s lifetime. conditions and rounded out by the design of specific components. The Challenge The hydropower plant, through its complexity and interaction of components, is designed based on available basic raw data. Even if this original data is of high quality, the actual physical situation after installation will always be different. Your Benefits / Op e r a ti o n S etp oints (C o D e sig n D a t a y) l mpon ent Su pp Figure 1: Real physical plant conditions deviate from the ideal design The Task The precondition for operation and performance of the hydropower plant is completely determined by both the plant’s individual components and the dynamic boundary conditions at the installation location. To take this into account for operation and for improving the controlling quality, these insights must be considered and implemented in the controller structure.
Open the catalog to page 1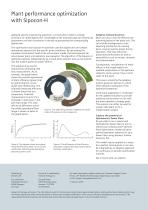
Plant performance optimization with Sipocon-H Applying specific engineering expertise, a virtual plant model is created, forming a so-called digital twin. Knowledge of the essential physical influencing parameters and their correlation is the key to generating the corresponding digital twin. The optimization tool Sipocon-H optimizer uses the digital twin and creates operational setpoints for the specific given conditions. By calculating the complete characteristic field of the virtual plant model, the best setpoints for actual power plant unit operation are evaluated. The algorithm of the...
Open the catalog to page 2All Siemens Energy - Power and heat generation catalogs and technical brochures
-
SGT-2000E
1 Pages
-
SGT6-5000F
1 Pages
-
SGT-8000H series
1 Pages
-
SGT-9000HL
1 Pages
-
Omnivise T3000
31 Pages
-
SGT-750
1 Pages
-
SGT-700
1 Pages
-
SGT-600
1 Pages
-
SGT-100
1 Pages
-
Gas turbines from 4 to 593 MW
68 Pages
-
Gas engines
19 Pages
-
Combined Heat and Power
8 Pages
-
SeaFloat Power Plants
4 Pages
-
Control Monitoring
6 Pages
-
SGT-A65 gas turbine
2 Pages
-
SGT-A35 (GT30) gas turbine
2 Pages
-
SGT-A05 Aeroderivate Gas Turbine
16 Pages
-
Brochure 89556
2 Pages
-
Brochure 89555
4 Pages
-
POWERGEN CASE STUDIES SUMMARY
19 Pages
-
OIL&GAS CASE STUDIES SUMMARY
9 Pages
-
CHP CASE STUDIES SUMMARY
21 Pages