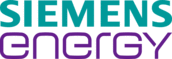

Catalog excerpts
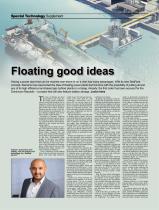
Special Technology Supplement Having a power plant that can be moored near-shore or on a river has many advantages. With its new SeaFloat concept, Siemens has resurrected the idea of floating power plants but this time with the possibility of putting almost any of its high efficiency land-based gas turbine plants on a barge. Already, the first order has been secured for the Dominican Republic - a project that will also feature battery storage. Junior Isles Hossain: Customers were asking, ‘can you supply your technology on a floating device?' The idea of floating gas fired power plants is not a new one. But rising global population, many of which are moving to live in megacities, where land is limited and expensive, could see the resurgence of these mobile power plants. Certainly Siemens sees this as one of the key drivers behind the development of a new floating combined cycle power plant concept it calls SeaFloat. According to Siemens, SeaFloat technology combines state-of-the-art combined cycle power plant technology with the mobility and flexibility required by the current and future energy market. Explaining why he thinks the market is now right for SeaFloat, Hamed Hossain, Business Owner SeaFloat Power Plants, Siemens Gas and Power, said: “In the mid 90s, floating power plants were becoming popular. At the time, Westinghouse (later bought by Siemens) was building floating power plants with gas turbines operating in open cycle. However, we saw an increase in oil and gas prices, which meant it was not worth building these plants anymore because of their low efficiency.” “Now it’s different. We are building state-of-the-art combined cycle power plants with really high efficiency, which means if oil and gas prices increase even more then it’s still worthwhile, economically. And if prices fall, we can use open cycle plants. So we have all the technology that’s available for land-based power plants on a floating structure. This allows flexibility on plant configuration, since installations are less affected by fuel price.” The real impetus to re-boot the idea of floating power plants, however, came about three or four years ago in response to market demand. Hossain said: “Customers were asking: ‘can you supply your technology on a floating device?’ So we decided to do it again. Two and a half years ago, when we saw that the market was really pushing for it, we set up an entity within Siemens to specifically focus on it.” Hossain sees SeaFloat as a technology that essentially gives customers more options when it comes to locating power plants, i.e. they can be built on water when land is too expensive or unavailable, and in locations where there is a high country risk. The technology has numerous applications, such as: powering up remote areas like islands; development of industrial areas on shorelines or major rivers (for example, chemical and desalination plants); the replacement of out-dated plants, allowing the existing plant to continue operating until the new one is in place and ready to be connected to the grid. SeaFloat power plants, which can provide from 145 MW up to 1.3 GW, can also be used as emergency backup for existing power plants during peak loads or outages and to provide power supply in the event of a humanitarian disaster. Another area where Siemens anticipates great demand is in the oil and gas sector. “We are in contact with all the oil and gas majors. Our portfolio is to put our power plants on FSRUs (floating storage regasification units),” said Hossain. “Looking at FPSOs (Floating Production Storage and Offloading vessels), traditionally they all use open cycle plants, which have higher emissions relative to power output compared to combined cycle plants. Installing a power plant for this application has its challenges, however. Although the SeaFloat power plant is compact and has a high power density, for an oil and gas platform, the weight and footprint has to be reduced even further. For a platform it should also be easy to install and have a high degree of modularisation. “This is how we came up with the ultra-light floating combined cycle power plant, which is part of the SeaFloat portfolio,” said Hossain. “It’s a major game changer; we have reduced the weight and footprint of the power plant by more than 50 per cent compared to combined cycle power plants already installed on existing platforms.” Installing a SeaFloat plant would certainly help oil and gas majors improve their green credentials and lower the cost of emitting carbon. In a country or industry where CO2 prices are high, of the order of €50/t, the savings can be significant. “Putting a combined cycle plant on an oil and gas platform or FPSO could reduce CO2 footprint by 80 000-110 000 t/annum. This translates to high single digit millions of euros in savings from CO2 taxes and certificates each year,” said Hossain. Siemens currently offers SeaFloat power plants based on three main gas turbine technologies - the SGT-800, SGT-A65 and the SGT-8000H series - but says it is not limited to these machines. “In addition to these, we also have the SGT-750, SGT-A35 (formerly the RB211), which will be for the oil and gas market,” noted Hossain. With the three initial technologies on offer, Siemens says it can address the majority of the market requirements it has seen so far. The turbines were selected following careful market analysis, an examination of the advantages of each turbine and according to feedback from customers and developers that have contacted Siemens. Each of the three gas turbine solutions has its own benefits. Hossain explained: “The SGT-800 solution is our frontrunner. Two thirds of the market is desperately screaming for the SGT-800, not only because it is a technology frontrunner but because of the various configurations that are possible. You can use it for new power generation installations based on LNG, and expansion of industrial applications in remote coastal areas. “For a peaker, or fast-start plant; i.e. start-up in less than five minutes in cold conditions or less than two minutes under hot conditions, the SGT-A65 is the right solution.” Because of its size, the SGT-8000H would be best deployed in situations where a large amount of bulk power is needed, and space is limited but the grid is stable. Hossain said: “It’s not possible to take an H-class unit capable of 620 MW or 1.3 GW in a 2-on-1 configuration and feed it into a weak grid in a developing country but in these cases we could offer our transmission grid stability solutions. And the H-class would have advantages. If for example, you want to replace a large coal fired power plant in a region that has a more stable grid, with a more efficient, lower emissions plant, here the H-class is the right fit.” He noted that customers in countries with labour challenges or those wanting to avoid the time and effort involved in obtaining permits to install land-based plants, are interested in installing SeaFloat plants. Project risk resulting from brownfield activities such as demolition works, site levelling activities, relocation of existing structure, etc., can be avoided when replacing old plants. As the barges are built at modern shipyards, the project schedule does not depend on availability of qualified labour and infrastructure at the final location. According to Siemens, this can cut construction time by 20 per cent. Siemens believes it is the simple plug and play, connect and go, possibility that makes SeaFloat plants so attractive. The concept allows fast and easy installation at shipyards. A SeaFloat plant, with the SGT-800 in particular, has a high degree of modularisation, where delivery of pre-assembled and
Open the catalog to page 1All Siemens Energy - Power and heat generation catalogs and technical brochures
-
SGT-2000E
1 Pages
-
SGT6-5000F
1 Pages
-
SGT-8000H series
1 Pages
-
SGT-9000HL
1 Pages
-
Omnivise T3000
31 Pages
-
SGT-750
1 Pages
-
SGT-700
1 Pages
-
SGT-600
1 Pages
-
SGT-100
1 Pages
-
Gas turbines from 4 to 593 MW
68 Pages
-
Gas engines
19 Pages
-
Combined Heat and Power
8 Pages
-
Control Monitoring
6 Pages
-
SGT-A65 gas turbine
2 Pages
-
SGT-A35 (GT30) gas turbine
2 Pages
-
SGT-A05 Aeroderivate Gas Turbine
16 Pages
-
Brochure 89556
2 Pages
-
Brochure 89555
4 Pages
-
POWERGEN CASE STUDIES SUMMARY
19 Pages
-
OIL&GAS CASE STUDIES SUMMARY
9 Pages
-
CHP CASE STUDIES SUMMARY
21 Pages