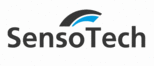
nline analytical technology for the chemical industry: concentration and density measurement, phase detection, multi-component analysis, monitoring of crystallizations and polymerizations
1 /
20Pages
Catalog excerpts
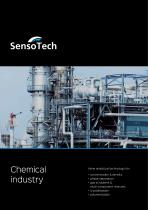
Chemical industry Inline analytical technology for: • concentration & density • phase separation • gas scrubbers & multi-component mixtures • crystallization • polymer
Open the catalog to page 1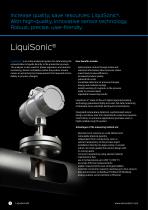
Increase quality, save resources: LiquiSonic®. With high-quality, innovative sensor technology. Robust, precise, user-friendly. LiquiSonic® LiquiSonic® is an inline analytical system for determining the concentration in liquids directly in the production process. The analyzer is also used for phase separation and reaction monitoring. Sensor installation within the product stream means an extremely fast measurement that responds immediately to process changes. User benefits include: • optimal plant control through online and real-time information about process states • maximized process...
Open the catalog to page 2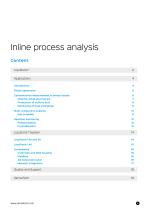
Inline process analysis Content LiquiSonic® Concentration measurement in binary liquids Chlorine-alkali electrolysis Production of sulfuric acid Monitoring of heat exchanger Multi-component analysis Gas scrubber Reaction monitoring Accessories16 Controller and field housing Network integration
Open the catalog to page 3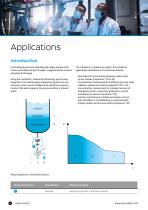
Applications Introduction Controlling the process optimally and safely requires information provided promptly through a rugged and fast process analytical technology. Using the LiquiSonic® measuring technology and its easy integration into existing plant engineering systems at relatively low project costs enables partly significant improvements of the plant capacity, the process safety or product yields. carrier phase The LiquiSonic® systems are used in many fields of application particularly in the chemical industry: • fast detection of transitions between product and carrier phases...
Open the catalog to page 4
Phase separation Different product phases must be separated safely from carrier phases during many process engineering intermediate steps. This is done both in continous and batch processes. This is often done in batch processes by changing manually valves as well as by visual observation of phase transitions. Usually, sight glasses are used to observe the transitions visually. But this procedure is characterized by a low reproducability. When using a LiquiSonic® immersion type sensor, the mentioned procedure is realized automatically. LiquiSonic® examples for application: • • • • •...
Open the catalog to page 5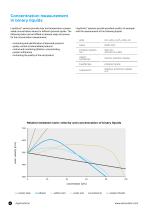
Concentration measurement in binary liquids LiquiSonic® sensors provide clear and temperature compensated concentration values for different process liquids. The following tasks can be fulfilled at relevant steps of process for the concentration measurement: • monitoring and identification of delivered products • quality control at intermediate products • control and monitoring (dilution, concentrating, product infiltration) • monitoring the quality of the end product LiquiSonic® systems provide excellent results, for example with the measurement of the following liquids: inorganic...
Open the catalog to page 6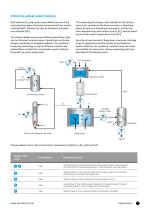
Chlorine-alkali electrolysis The measuring technology is also suitable for the salt production, for example for the brine extraction or dissolving plants, as well as in downstream processes, such as the chlor dehydrationing with sulfuric acid (H2SO4) and the blending of caustic soda or hydrochloric acid (HCl). Both chlorine (Cl2) and caustic soda (NaOH) are one of the most important basic chemicals and produced from sodium chloride (NaCl). Chlorine can also be obtained from potassium chloride (KCl). The chlorine-alkali process uses different electrolytic methods, but the most common types...
Open the catalog to page 7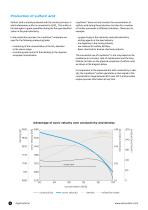
Production of sulfuric acid Sulfuric acid is mostly produced with the contact process, in which elementary sulfur is converted to H2SO4. This sulfur is formed again in great quantities during the flue gas desulfurization in the petrochemistry. LiquiSonic® does not only monitor the concentration of sulfuric acid during the production, but also for a number of further processes in different industries. These are, for example: In the production process, the LiquiSonic® analyzers are used for the following measuring tasks: • monitoring of the concentration in the SO3 absorber to the oleum range...
Open the catalog to page 8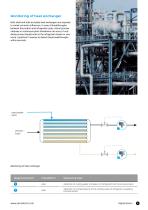
Monitoring of heat exchanger Both shell-and-tube and plate heat exchangers are exposed to varied corrosion influences. In case of breakthroughs between the product and refrigerant cycle, critical process statuses or continuous plant shutdowns can occur, if suddenly process liquids enter in the refrigerant stream or vice versa. LiquiSonic® assures to detect these breakthroughs within seconds. heat transfer liquid 2 Monitoring of heat exchanger Measuring point Measuring task detection of cooling water or break-in of refrigerant into the process liquid detection of contaminations of the...
Open the catalog to page 9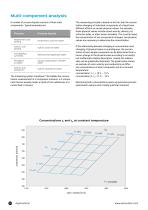
Multi-component analysis A number of process liquids consists of three main components. Typical examples are: The measuring principle is based on the fact that the concentration changing of individual components of a liquid have different effects on certain physical values. For example, these physical values include sound velocity, density, pH, refractive index, or other known variables. If in a carrier liquid, the concentration of two components changes, two physical values are necessary to determine the concentration. Process liquids Hydrochloric acid pickling Hydrochloric acid-iron-water...
Open the catalog to page 10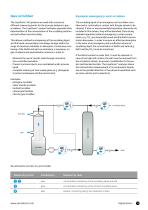
Example: emergency vent scrubber The LiquiSonic® 40 systems are used with success at different measuring points for the process analysis in gas scrubbers. The LiquiSonic® system facilitates separate inline determination of the concentration of the scrubbing solution and salt without any time delay. The scrubbing liquid of an emergency vent scrubber circulates and is continually in contact with the gas stream to be cleaned. If toxic or environmentally hazardous chemicals are included in this stream, they will be absorbed. Even during standard operation (without emergency), certain...
Open the catalog to page 11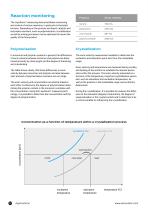
Reaction monitoring The LiquiSonic® measuring device facilitates monitoring and control of various reactions, in particular in the batch process. Depending on the process and liquid, catalytic and enzymatic reactions, such as polymerization, crystallization as well as mixing processes can be optimized to ensure the quality of the final product. Sonic velocity vinyl chloride polyvinyl chloride In monomer and polymer systems in general, the differences of sonic velocity between monomer and polymer are determined primarily by chain length and the degree of branching and crosslinking. The sonic...
Open the catalog to page 12All SensoTech catalogs and technical brochures
-
Aircraft Deicingy
3 Pages
-
Company Profile
8 Pages