

Catalog excerpts
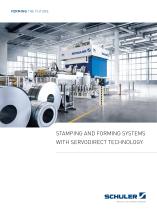
STAMPING AND FORMING SYSTEMS WITH SERVODIRECT TECHNOLOGY Member of the ANDRITZ GROUP
Open the catalog to page 1
TABLE OF CONTENTS / Stamping and forming SYSTEMS WITH SERVODIRECT TECHNOLOGY Stamping and forming SYSTEMS WITH SERVODIRECT TECHNOLOGY 4 WELCOME TO SCHULER Stamping and forming systems with ServoDirect Technology 8 SERVODIRECT TECHNOLOGY Success can be programmed 14 SERVO PRESSES IN MONOBLOCK DESIGN Perfection down to the last detail 18 SERVO PRESSES IN TIE ROD DESIGN Flexibility and efficiency for greater productivity 22 KNUCKLE-JOINT PRESSES WITH SERVO DRIVE Precise, versatile and durable 30 AUTOMATION BY SCHULER Automatically greater flexibility 32 PROCESS MANAGEMENT Efficiency along the...
Open the catalog to page 3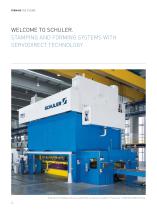
WELCOME TO SCHULER. Stamping and forming SYSTEMS WITH SERVODIRECT TECHNOLOGY. Production of double parts at an automotive components supplier. Press force: 16,000 kN (1,800 US tons). 4
Open the catalog to page 4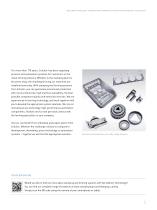
WELCOME TO SCHULER / Stamping and forming SYSTEMS WITH SERVODIRECT TECHNOLOGY For more than 170 years, Schuler has been supplying presses and automation systems for customers in the metal forming industry. Whether in the stamping plant or the press shop, the challenges facing our machines are redefined every day. With stamping and forming systems from Schuler, you can guarantee economical production with more productivity, high machine availability, the best possible component quality and extensive services. We are experienced in forming technology, and work together with you to develop...
Open the catalog to page 5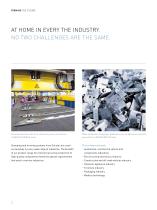
AT HOME IN EVERY THE INDUSTRY. NO TWO CHALLENGES ARE THE SAME. Series production with a tie rod servo press, press force: 16,000 kN (1,800 US tons). Mass-production stampings, produced on a monoblock servo press, press force: 2,500 kN (280 US tons). Stamping and forming systems from Schuler are used This is where we exel: successfully in a very wide range of industries. The breadth Automotive, commercial vehicle and of our product range for economical series production of components industries high-quality components meets the special requirements Electrical and electronics industry that...
Open the catalog to page 6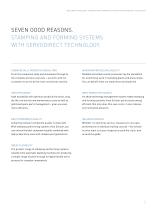
WELCOME TO SCHULER / Stamping and forming SYSTEMS WITH SERVODIRECT TECHNOLOGY SEVEN GOOD REASONS. Stamping and forming SYSTEMS WITH SERVODIRECT TECHNOLOGY. COMMERCIALLY ORIENTED CONSULTING MAXIMUM PROCESS RELIABILITY From the component study and simulations through to Reliable and stable overall processes lay the foundation the complete process overview – we work with our for economical work in stamping plants and press shops. customers to arrive at the most economical solution. You can benefit from our experience and expertise. HIGH EFFICIENCY BEST ENERGY EFFICIENCY High availability with...
Open the catalog to page 7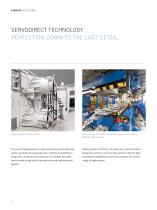
SERVODIRECT TECHNOLOGY. PERFECTION DOWN TO THE LAST DETAIL. Highly dynamic torque motors. Series production with a tie rod servo press, press force: 8,000 kN (900 US tons). The use of highly dynamic torque motors for press operation Highly dynamic Schuler roll feed units, coil feed lines, opens up totally new perspectives: maximum flexibility in destackers and tri-axis transfer systems deliver fully production, economical production of complex part geo- automated stamping and forming systems for a wide metries and a high level of productivity with optimum part
Open the catalog to page 8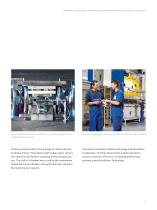
SERVODIRECT TECHNOLOGY / Stamping and forming SYSTEMS WITH SERVODIRECT TECHNOLOGY Series production with a monoblock servo press, press force: 6,300 kN (700 US tons). Process consulting for maximum output with optimum parts quality. Presses with ServoDirect Technology are driven directly Precise harmonization of press technology with automation by torque motors. They deliver high torque values and are components, forming requirements and die operations the right drive for dynamic stamping and forming proces- ensures maximum efficiency in stamping and forming ses. The lack of a flywheel and...
Open the catalog to page 9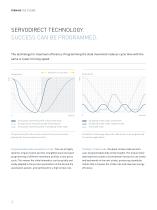
SERVODIRECT TECHNOLOGY. SUCCESS CAN BE PROGRAMMED. The technology for maximum efficiency: Programming the slide movement reduces cycle time with the same or lower forming speed. Reduction in cycle time Servo press movement profile in full stroke mode Eccentric press movement profile (conventional) Servo press movement profile in oscillating stroke mode Oscillating stroke mode, small stroke Oscillating stroke mode, medium stroke Full stroke mode Programming the slide motion reduces the cycle time while keeping the forming speed constant. ServoDirect Technology allows the...
Open the catalog to page 10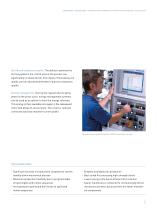
SERVODIRECT TECHNOLOGY / Stamping and forming SYSTEMS WITH SERVODIRECT TECHNOLOGY Die life and component quality. The ability to optimize the forming speed in the critical area of the process can significantly increase die life. The impact of fluctuating coil quality can be reduced and therefore improve component quality. Energy management. During the regenerative braking phase of the press cycle, energy management systems can be used as an option to store the energy released. This energy is then available once again in the subsequent motorized phase of acceleration. The result is reduced...
Open the catalog to page 11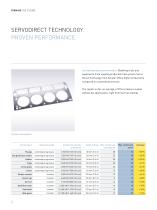
SERVODIRECT TECHNOLOGY. PROVEN PERFORMANCE. Increasing output performance. Blanking trials and experience from ongoing production have proven Servo Direct Technology from Schuler offers higher productivity compared to conventional presses. The results so far: on average, a 70 % increase in output without die optimization, right from the first attempt. Cylinder head gasket. Formed part Operating mode Component-specific press force Depth of draw Max. stroke rate conventional Max. stroke rate servo combined progressive combined progressive combined progressive combined progressive Cross plate...
Open the catalog to page 12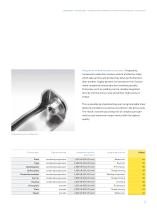
SERVODIRECT TECHNOLOGY / STAMPING AND FORMING SYSTEMS WITH SERVODIRECT TECHNOLOGY Component with welded nut. Integration of downstream processes. Frequently, component production involves several production steps which take up time and productivity when performed one after another. Highly dynamic servomotors from Schuler make completely new production methods possible. Processes such as welding can be reliably integrated directly into the press cycle and deliver high levels of This is possible by implementing user-programmable time/ distance procedures as well as rest times in the press...
Open the catalog to page 13All SCHULER - MÜLLER WEINGARTEN catalogs and technical brochures
-
THE ENTIRE WORLD OF METAL FORMING
116 Pages
-
Laser Blanking Lines
8 Pages
-
DIE AND FORMING TECHNOLOGIES
10 Pages
-
Forming the future
12 Pages
-
Forming the future
6 Pages
-
TRYOUT SYSTEMS FROM SCHULER
10 Pages
-
FORGING HAMMERS
24 Pages
-
MECHANICAL PRESSES IN FORGING
16 Pages
-
Schuler ServoLine
12 Pages
-
Stamping and cutting systems
32 Pages
-
Knucke-joint presses
20 Pages
-
The entire world of forging
84 Pages
-
Formmaster
4 Pages
-
blanking lines Catalogue 2013
16 Pages
-
Impact extrusion presses
8 Pages
-
Automation for press lines
6 Pages
-
Process Technology
8 Pages
-
Blank washers
4 Pages
-
Hydraulic press lines
14 Pages
-
Hot forming systems
8 Pages
-
Equipment for Minting Technology
24 Pages
-
LoadMaster System
12 Pages
-
TwinServo Technology
8 Pages
-
hydraulic Tryout Presses
12 Pages
-
Laser Lines
4 Pages
-
Hydraulic press systems
8 Pages
-
Blanking lines Catalogue 2011
10 Pages