

Catalog excerpts
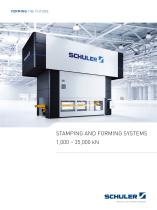
STAMPING AND FORMING SYSTEMS 1,000 - 35,000 kN Member of the ANDRITZ GROUP
Open the catalog to page 1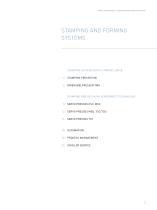
TABLE OF CONTENTS / STAMPING AND FORMING SYSTEMS STAMPING SYSTEMS WITH FLYWHEEL DRIVE 4 STAMPING PRESSES MC 6 KNIEHEBELPRESSEN TMK STAMPING PRESSES WITH SERVODIRECT TECHNOLOGY. 8 SERVO PRESSES CSC, MSC 12 SERVO PRESSES MSD, TSC/TSD 16 SERVO PRESSES TST 18 AUTOMATION 20 PROCESS MANAGEMENT 22 SCHULER SERVICE
Open the catalog to page 3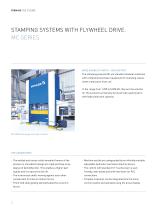
WIDE RANGE OF PARTS - HIGH OUTPUT The stamping presses MC are standard modular machines with comprehensive basic equipment for stamping classic sheet metal parts from coil. In the range from 1,250 to 5,000 kN, they are the solution for the economical manufacturing of high-quality parts with high production capacity. ■ The welded and stress-relief annealed frames of the presses in monoblock design are rigid and have a low degree of bed deflection. This enables a higher part quality and increases the die life. ■ The transversal shafts moving against each other compensate for lateral rotation...
Open the catalog to page 4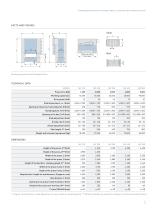
STAMPING SYSTEMS WITH FLYWHEEL DRIVE / STAMPING AND FORMING SYSTEMS Stamping presses with flywheel drive. TECHNICAL DATA * Largest stroke bottom, slide adjustment on top, without clamping plate. ** Without dampening elements. Subject to technical modifications.
Open the catalog to page 5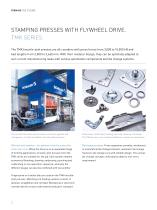
STAMPING PRESSES WITH FLYWHEEL DRIVE. TMK SERIES. The TMK knuckle-joint presses are all-rounders with press forces from 3,000 to 15,000 kN and bed lengths from 3,000 to 3,660 mm. With their modular design, they can be optimally adapted to suit current manufacturing tasks with various automation components and die change systems. The versatile knuckle-joint presses are easy to operate and changeover– for high availability and cost effectiveness. Embossing, calibrating, bending, piercing, drawing, stamping: The TMK series is universally suitable for a range of components. Efficient and...
Open the catalog to page 6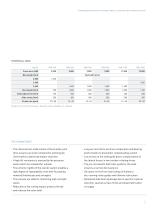
STAMPING SYSTEMS WITH FLYWHEEL DRIVE / STAMPING AND FORMING SYSTEMS TECHNICAL DATA Subject to technical changes. Special sizes available on request. ■ The characteristic slide motion of the knuckle-joint drive ensures accurate components and long die lives thanks to optimized impact velocities ■ A high tilt resistance is ensured by the pressure points which are situated far outside ■ The extreme rigidity of the overall system enables a high degree of repeatability, even with fluctuating material thicknesses and strengths ■ The presses are ideal for machining high-strength steels ■ Reduction...
Open the catalog to page 7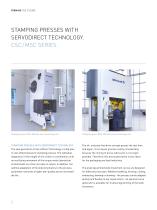
STAMPING PRESSES WITH SERVODIRECT TECHNOLOGY. CSC / MSC SERIES. Stamping press CSC 100 with one connecting rod. Stamping press MSC 200 with two connecting rods. STAMPING PRESSES WITH SERVODIRECT TECHNOLOGY. The oil- and play-free drive concept passes the test time The new generation of ServoDirect Technology is a big plus and again. It increases process safety considerably, in cost-effectiveness for stamping presses. The individual because the mixing of press lubricants is no longer adaptation of the height of the stroke in combination with possible. Therefore, this press generation is also...
Open the catalog to page 8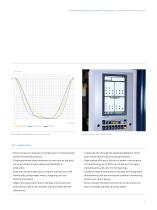
STAMPING PRESSES WITH SERVODIRECT TECHNOLOGY / STAMPING AND FORMING SYSTEMS standard Drawing ziehen Embossing prägen Crank Preprogrammed slide movement curves. Control panel with touchscreen. THE ADVANTAGES lear increase in outputs in comparison to conventionally C driven mechanical presses reprogrammed slide movement curves and an optional P curve generator ensure maximum flexibility in production asy and intuitive operation using the touchscreen with E individually configurable menu, shopping cart and favorites functions igher precision parts due to the play-free drive train H and...
Open the catalog to page 9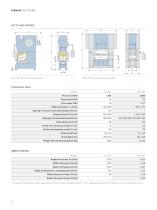
MSC 200 with two connecting rods TECHNICAL DATA MODEL Slide dimensions, L × J [mm] Opening in the press frame (backwards), M [mm] Clamping plate, N × O [mm] Stroke rate (continuous mode) [1 / min] Stroke rate (pendulum mode) [1 / min] Weight with standard equipment [kg] Height of the bed (incl. clamping plate), E [mm] Width of the press frame, F [mm] Depth of the press frame, G [mm] * Largest stroke bottom, slide adjustment on to
Open the catalog to page 10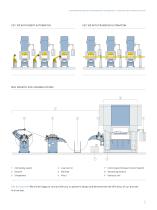
STAMPING PRESSES WITH SERVODIRECT TECHNOLOGY / STAMPING AND FORMING SYSTEMS CSC 100 WITH ROBOT AUTOMATION CSC 100 WITH TRANSFER AUTOMATION MSC 200 WITH COIL FEEDING SYSTEM 1 Coil feeding system 7 Control panel (Compact Control System) See for yourself. We will be happy to consult with you on systems design and demonstrate the efficiency of our presses in a live test.
Open the catalog to page 11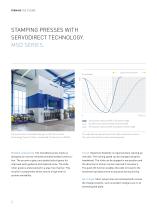
STAMPING PRESSES WITH SERVODIRECT TECHNOLOGY. MSD SERIES. Cycle time reduction Servo press motion profile in full stroke mode Eccentric press (conventional) motion profile Servo press motion profile in pendulum stroke mode Servo presses in monoblock design in the Process and Technology Centre ProTec, Lennestadt. Press force: 6,300 kN. The individual programming of the slide movement reduces the cycle time with the same forming speed. Reliable components. The monoblock press frame is Tryout. Maximum flexibility is required when starting up designed as a stress-relieved annealed...
Open the catalog to page 12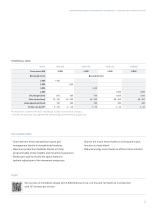
STAMPING PRESSEN WITH SERVODIRECT TECHNOLOGY / STAMPING AND FORMING SYSTEMS TECHNICAL DATA All details for systems with dual-rod design. Subject to technical changes. * Stroke rate depends on programmed stroke height and kinematic properties. ■ Short delivery times and optimum spare part ■ Shorter die tryout times thanks to inching and tryout management thanks to standardised modules function via hand wheel ■ Maximum production flexibility thanks to freely ■ Reduced energy costs thanks to efficient drive solution programmable stroke heights and movement sequences ■ Better part...
Open the catalog to page 13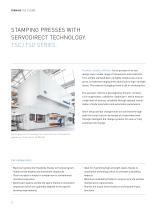
STAMPING PRESSES WITH SERVODIRECT TECHNOLOGY. TSC / TSD SERIES. Flexible, reliable, efficient. Servo presses in tie rod design cover a wide range of components and materials: from simple stamped parts to highly complex structural parts, in materials ranging from aluminium to high-strength steels. The material is supplied from a coil or via destacker. The operator interface developed by Schuler contains a curve generator, called the »Optimizer«, which ensures a high level of process reliability through optimal coordination of slide kinematics and automation parameters. Short setup and die...
Open the catalog to page 14All SCHULER - MÜLLER WEINGARTEN catalogs and technical brochures
-
THE ENTIRE WORLD OF METAL FORMING
116 Pages
-
Laser Blanking Lines
8 Pages
-
DIE AND FORMING TECHNOLOGIES
10 Pages
-
Forming the future
12 Pages
-
Forming the future
6 Pages
-
TRYOUT SYSTEMS FROM SCHULER
10 Pages
-
FORGING HAMMERS
24 Pages
-
MECHANICAL PRESSES IN FORGING
16 Pages
-
Schuler ServoLine
12 Pages
-
Stamping and cutting systems
32 Pages
-
Knucke-joint presses
20 Pages
-
The entire world of forging
84 Pages
-
Formmaster
4 Pages
-
blanking lines Catalogue 2013
16 Pages
-
Impact extrusion presses
8 Pages
-
Automation for press lines
6 Pages
-
Process Technology
8 Pages
-
Blank washers
4 Pages
-
Hydraulic press lines
14 Pages
-
Hot forming systems
8 Pages
-
Equipment for Minting Technology
24 Pages
-
LoadMaster System
12 Pages
-
TwinServo Technology
8 Pages
-
hydraulic Tryout Presses
12 Pages
-
Laser Lines
4 Pages
-
Hydraulic press systems
8 Pages
-
Blanking lines Catalogue 2011
10 Pages