

Catalog excerpts
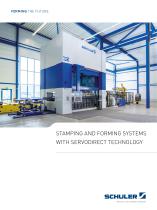
STAMPING AND FORMING SYSTEMS WITH SERVODIRECT TECHNOLOGY Member of the ANDRITZ GROUP
Open the catalog to page 1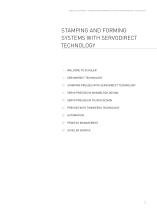
TABLE OF CONTENTS / STAMPING AND FORMING SYSTEMS WITH SERVODIRECT TECHNOLOGY STAMPING AND FORMING SYSTEMS WITH SERVODIRECT TECHNOLOGY 4 WELCOME TO SCHULER 6 SERVODIRECT TECHNOLOGY 10 STAMPING PRESSES WITH SERVODIRECT TECHNOLOGY 14 SERVO PRESSES IN MONOBLOCK DESIGN 18 SERVO PRESSES IN TIE ROD DESIGN 22 PRESSES WITH TWINSERVO TECHNOLOGY 26 AUTOMATION 28 PROCESS MANAGEMENT 30 SCHULER SERVICE
Open the catalog to page 3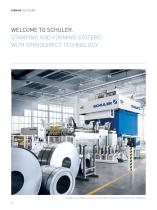
WELCOME TO SCHULER. STAMPING AND FORMING SYSTEMS WITH SERVODIRECT TECHNOLOGY. Production of double parts at an automobile manufacturer. Press force: 16,000 kN. 4
Open the catalog to page 4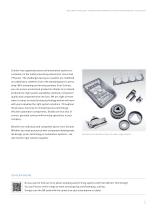
WELCOME TO SCHULER / STAMPING AND FORMING SYSTEMS WITH SERVODIRECT TECHNOLOGY Schuler has supplied presses and automation systems to customers in the metal processing industry for more than 175 years. The challenges facing our systems are redefined on a daily basis, whether it be in the stamping plant or press shop. With stamping and forming systems from Schuler, you can ensure economical production thanks to increased productivity, high system availability, optimum component quality and comprehensive services. We are right at home when it comes to metal forming technology and we will work...
Open the catalog to page 5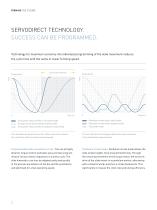
SERVODIRECT TECHNOLOGY. SUCCESS CAN BE PROGRAMMED. Technology for maximum economy: the individual programming of the slide movement reduces the cycle time with the same or lower forming speed. Cycle time reduction Servo press motion profile in full stroke mode Eccentric press (conventional) motion profile Servo press motion profile in pendulum stroke mode Pendulum stroke mode, small stroke Pendulum stroke mode, medium stroke Full stroke mode The individual programming of the slide movement reduces the cycle time with the same forming speed. The ServoDirect technology...
Open the catalog to page 6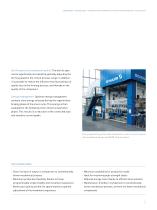
SERVODIRECT TECHNOLOGY / STAMPING AND FORMING SYSTEMS WITH SERVODIRECT TECHNOLOGY Die life spans and component quality. The die life span can be significantly increased by optimally adjusting the forming speed in the critical process range. In addition, it is possible to reduce the influence that fluctuating coil quality has on the forming process, and thereby on the quality of the component. Energy management. Optional energy management systems store energy released during the regenerative braking phase of the press cycle. This energy is then available for the following motor-driven...
Open the catalog to page 7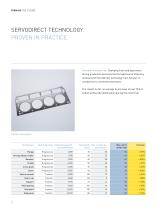
SERVODIRECT TECHNOLOGY. PROVEN IN PRACTICE. Increase in output rate. Stamping trials and experience during production demonstrate the high level of efficiency achieved with ServoDirect technology from Schuler, in comparison to conventional presses. The results so far: on average an increase of over 70 % in output without die optimisation during the initial trial. Cylinder head gasket. Formed part Operating mode Component-specific press force [kN] Draw depth Max. stroke rate, [mm] conventional Max. servo stroke rate Cross plate Centre console Tank opening Seat shell Side panel
Open the catalog to page 8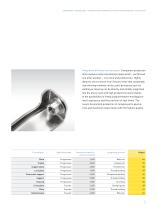
SERVODIRECT TECHNOLOGY / STAMPING AND FORMING SYSTEMS WITH SERVODIRECT TECHNOLOGY Integration of follow-on processes. Component production often involves several production steps which - performed one after another - cost time and productivity. Highly dynamic servo motors from Schuler mean that completely new working methods can be used: processes such as welding or lasering can be directly and reliably integrated into the press cycle with high productivity levels thanks to the possibilities of freely programmable time/displace- ment sequences and the provision of rest times. The result:...
Open the catalog to page 9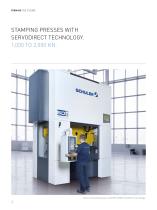
STAMPING PRESSES WITH SERVODIRECT TECHNOLOGY. 1,000 TO 2,000 KN. Dual-rod stamping press with MSC 2000 ServoDirect technology. 10
Open the catalog to page 10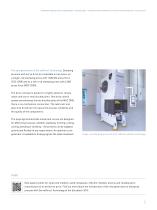
STAMPING PRESSES WITH SERVODIRECT TECHNOLOGY / STAMPING AND FORMING SYSTEMS WITH SERVODIRECT TECHNOLOGY The new generation of ServoDirect Technology. Stamping presses with servo drive are available in two sizes: as a single-rod stamping press with 1,000 kN press force (CSC 1000) and as a twin-rod stamping press with 2,000 press force (MSC 2000). The drive concept is based on a highly-dynamic torque motor and one or two knuckle joints. One drive control system synchronises the two knuckle joints of the MSC 2000, there is no mechanical connection. The lubricant and play-free drivetrain...
Open the catalog to page 11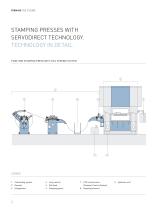
STAMPING PRESSES WITH SERVODIRECT TECHNOLOGY. TWIN-ROD STAMPING PRESSWITH COIL FEEDING SYSTEM 1 Coil feeding system 4 Loop control 7 CCS control panel 9 Hydraulic unit 2 Decoiler 5 Roll feed (Compact Control System] 3 Straightener 6 Stamping press 8 Damping element
Open the catalog to page 12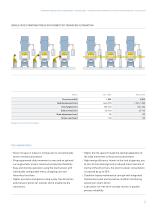
STAMPING PRESSES WITH SERVODIRECT TECHNOLOGY / STAMPING AND FORMING SYSTEMS WITH SERVODIRECT TECHNOLOGY SINGLE-ROD STAMPING PRESS WITH ROBOT OR TRANSFER AUTOMATION Subject to technical changes. THE ADVANTAGES Clear increase in output in comparison to conventionally driven mechanical presses Higher die life spans through the optimal adaptation of the slide movement to the process parameters Preprogrammed slide movement curves and an optional High energy efficiency: thanks to the lack of gearing, use curve generator ensure maximum production flexibility of anti-friction bearings and a...
Open the catalog to page 13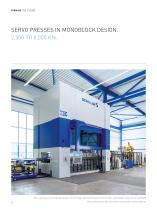
SERVO PRESSES IN MONOBLOCK DESIGN. 2,500 TO 8,000 KN. Servo presses in monoblock design in the Process and Technology Centre ProTec, Lennestadt. Press force: 6,300 kN 14 More information can be found at www.protec-lennestadt.de
Open the catalog to page 14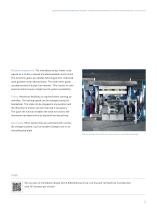
SERVO PRESSES IN MONOBLOCK DESIGN / STAMPING AND FORMING SYSTEMS WITH SERVODIRECT TECHNOLOGY Reliable components. The monoblock press frame is designed as a stress-relieved annealed welded construction. The eccentric gears are double helical gears for improved axial guidance and reduced noise. The slide roller guide is pretensioned in a play-free manner. This results in components which ensure a high level of system availability. Tryout. Maximum flexibility is required when starting up new dies. The inching speed can be changed using the handwheel. The slide can be stopped in any position...
Open the catalog to page 15All SCHULER - MÜLLER WEINGARTEN catalogs and technical brochures
-
THE ENTIRE WORLD OF METAL FORMING
116 Pages
-
Laser Blanking Lines
8 Pages
-
DIE AND FORMING TECHNOLOGIES
10 Pages
-
Forming the future
12 Pages
-
Forming the future
6 Pages
-
TRYOUT SYSTEMS FROM SCHULER
10 Pages
-
FORGING HAMMERS
24 Pages
-
MECHANICAL PRESSES IN FORGING
16 Pages
-
Schuler ServoLine
12 Pages
-
Knucke-joint presses
20 Pages
-
The entire world of forging
84 Pages
-
Formmaster
4 Pages
-
blanking lines Catalogue 2013
16 Pages
-
Impact extrusion presses
8 Pages
-
Automation for press lines
6 Pages
-
Process Technology
8 Pages
-
Blank washers
4 Pages
-
Hydraulic press lines
14 Pages
-
Hot forming systems
8 Pages
-
Equipment for Minting Technology
24 Pages
-
LoadMaster System
12 Pages
-
TwinServo Technology
8 Pages
-
hydraulic Tryout Presses
12 Pages
-
Laser Lines
4 Pages
-
Hydraulic press systems
8 Pages
-
Blanking lines Catalogue 2011
10 Pages