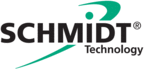
Catalog excerpts
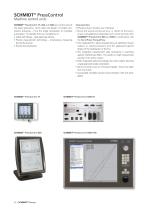
Machine control units ® SCHMIDT PressControl 75, 600 and 5000 are control units of the latest generation, which allow the design of modern production processes – from the single workstation to complete automation. You benefit from our competence in: Safety technology – type-approved devices rocess measurement technology – simultaneous measuring P during the process Process documentation Characteristics fficiency due to intuitive user interfaces E uick and secure process set-up e. g. thanks to the touch- Q screen and additional handwheel ram control function with SCHMIDT ® PressControl 600 and 5000 in combination with the ServoPress / TorquePress he integrated PLC allows programming of additional inputs T / outputs or sensors / actuators and the application-specific design of the workstation or the line he integrated measurement data processing is insensitive T against nterferences (EMC). This results in a high measurement i security of the entire system ith integrated safety technology, the entire system becomes W a type-approved single workstation ervice functions such as "Firmware Update" ensure the liabilS ity in the future uaranteed complete process documentation with full traceG ability
Open the catalog to page 1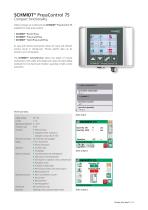
SCHMIDT® PressControl 75 Compact functionality Highly compact yet multifunctional SCHMIDT® PressControl 75 available for these press systems: ■ SCHMIDT® ElectricPress ■ SCHMIDT® PneumaticPress ■ SCHMIDT® HydroPneumaticPress Its easy and intuitive touchscreen allows for quick and efficient process set-up or change-over. Process specific data can be stored in up to 24 datasets. The SCHMIDT ® SafetyModule allows the design of manual workstations with safety technology that meets the latest global standards for two-hand cycle initiation, guarding or light-curtain protection. Data input Supply...
Open the catalog to page 2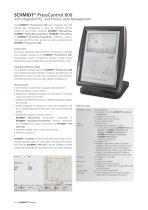
with integrated PLC and Process Data Management The SCHMIDT ® PressControl 600 with integrated PLC and process data management is made for intelligent process / control of force stroke monitored SCHMIDT ® ManualPress, SCHMIDT ® (Hydro)PneumaticPress, SCHMIDT ® ElectricPress or SCHMIDT ® ServoPress / TorquePress. Additional automation tasks around the press process can also be realized by the SCHMIDT ® PressControl 600. Control Unit All process integrated system elements and data are controlled and managed centrally by the SCHMIDT ® PressControl 600. The standard system configuration...
Open the catalog to page 3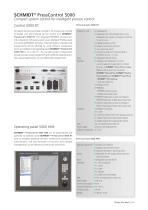
Control 5000 RT Operating panel with Screen Drive Interfaces EMC Power supply Current consumption Ambient temperature Protection class Weight All system elements and data involved in the process are centrally controlled and administrated by the control unit SCHMIDT ® PressControl 5000 RT. The integrated PROFIBUS interface permits integration of the press system as an intelligent Profibus slave into existing PROFIBUS networks. Parametrization, operation and programming will be effected by using software components which are installed on the operating panel SCHMIDT ® PressControl 5000 HMI or...
Open the catalog to page 4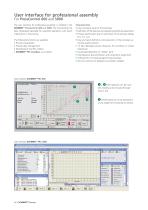
The user interface for professional assembly is installed in the SCHMIDT ® PressControl 600 and 5000. The functionality has been developed especially for assembly operations with direct intervention in the process. The following functions are available ■ Process visualization ■ Process data management ■ Development tool (PLC editor) ■ SCHMIDT® PRC DataBase as an option Characteristics ■ Easy and quick setup of the processes ■ Definition of the data sets and operating profiles by parameters ■ Process optimization due to switchover of the process display (F / s, F / t, s / t) ■ Easy and quick...
Open the catalog to page 5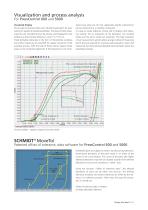
Visualized Display Force output and press stroke are important parameters for evaluating the quality of pressed assemblies. The data of these measurements are recorded during the process and displayed by the software as force / stroke behaviour curve F / s, F / t or s / t. Freely definable tolerances in the form of force/stroke windows and stroke tolerances are provided for quality assurance of the assembly process. With the help of these criteria, quality critical areas can be monitored selectively. If the tolerances in the monitored curve areas are not met, application-specific...
Open the catalog to page 6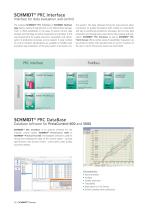
Interface for data evaluation and control The modular SCHMIDT® PRC Interface of SCHMIDT Technology meets a variety of requirements in the field of data management. It offers possibilities in the areas of system control, data storage, and exchange as well as visualization and analysis. In this way requirements for quality assurance, traceability, and optimization of production processes can be realized. A large number of current interfaces specifications are available on Fieldbus level and allow easy integration of the press system into master con- trol systems. The data obtained during the...
Open the catalog to page 7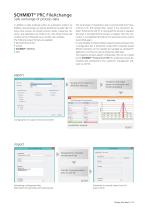
Safe exchange of process data In addition to data exchange within an automation solution via Fieldbus, data exchange can also be performed via data files. For every press process all relevant process results, tolerances, observer, and parameters are written into a file whose format and content can be configured via an intuitive user interface. The following output formats are available: Microsoft Excel (CSV) Q-DAS SCHMIDT® CRV/TOL XML The transmission of production data is synchronized from PressControl to PC (File System).That means if the connection between PressControl and PC is...
Open the catalog to page 8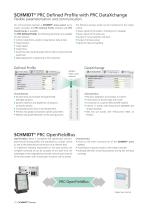
For communication between a SCHMIDT® press system and a master controller, the PRC Defined Profile interface with PRC DataXchange is available. For PRC Defined Profile, the following parameters are available for each position: ■ Control mode (force, position, slope detect, delta stroke) ■ Target position ■Target speed ■Target force ■ Dwell time after reaching target (only for self-running command sequences) ■ Speed adjustment at beginning of the movement The following process results can be transferred to the master control: ■ Status signals of the system, including error messages ■ Status...
Open the catalog to page 9All SCHMIDT Technology catalogs and technical brochures
-
SCHMIDT® ServoPress
13 Pages
-
SCHMIDT® HydroPneumaticPress
29 Pages
-
SCHMIDT® ManualPress
19 Pages
-
SCHMIDT® PneumaticPress
13 Pages
-
SCHMIDT® PressControl
12 Pages
-
Schmidt® Presses
85 Pages