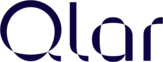

Catalog excerpts
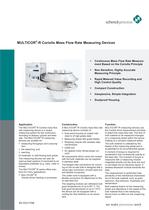
MULTICOR®-R Coriolis Mass Flow Rate Measuring Devices Continuous Mass Flow Rate Measurement Based on the Coriolis Principle Non-Sensitive, Highly Accurate Measuring Principle Rapid Metered Value Recording and High Control Quality Compact Construction Inexpensive, Simple Integration Dustproof Housing The MULTICOR -R Coriolis mass flow rate measuring device is a closed measuring system for the continuous recording of delivery volume and feed ® rate. The MULTICOR -R measuring devices are suitable for: measuring throughput and consumption; the balancing, and batching of moderate- to well-flowing bulk goods. The measuring devices can also be used as feed systems if connected to an adjustable prefeeder (e.g. valve, roller or screw). The MULTICOR®-R series offers solutions for many applications: MULTICOR®-R Gravity-driven feeding in processes A MULTICOR -R Coriolis mass flow rate measuring device consists of: Dust-proof housing of coated mild steel or of high-grade steel Measuring wheel with guide blades Weighing module with wireless data transmission Cable box AC geared motor (three-phase current) All components which come into contact with the bulk materials can be supplied in stainless steel. The flanged inlet connections for mounting on the on-site inlet is designed with a Jacob pipe connection, smooth pipe end and flexible connection. The outlet cone is equipped with a flexible connection for attachment to the on-site feed line. The weighing module can withstand bulk good temperatures of up to 60° C. For bulk good temperatures of up to 110°C the device can be equipped with a cooling fan that switches on as necessary. MULTICOR -R measuring devices use the Coriolis force measurement principle to determine mass flow rate. The flow of bulk material to be measured impinges on a measuring wheel within the device rotating at a constant rotational speed. The bulk material is collected by the blades of the measuring wheel and is accelerated to its circumferential speed. A moment of torque is required for acceleration that corresponds exactly to the feed rate. The moment of torque is measured with a measuring module integrated directly into the drive line and is converted into an electrical signal. A wireless Bluetooth module transmits the data. The measurement is performed independently of the mechanical characteristics of the bulk material, such as grain spectrum, flow behavior, moistness and temperature. Bulk material friction on the measuring wheel and alterations in the speed of the bulk material flow in the measuring device have no effect on the measuring signal.
Open the catalog to page 1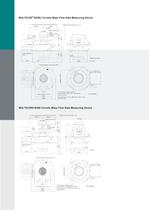
recomended space to performe maintenance height of fait over inlet: max. 7,5m rotation direction measuring wheel
Open the catalog to page 2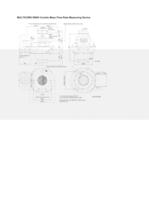
MULTICOR®-R800 Coriolis Mass Flow Rate Measuring Device
Open the catalog to page 3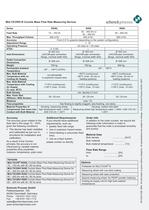
MULTICOR®-R Coriolis Mass Flow Rate Measuring Devices Series Max. Throughput Volume Accuracy Adjustment Range Operating Pressure ATEX Inlet Dimensions Outlet Connection Dimensions Weight Permissible Ambient Temperature Max. Bulk Material Temperature with no Cooling Air Supply Max. Bulk Material Temperature with Cooling Air Supply (Tk max. 45°C) Bulk Density Max. Grain Size (Without / With Screen) Moisture Flow properties Material Properties of Components that come into Contact with Bulk Material 30 – 300 t/hr or 15 – 150 t/h 60 – 600 t/hr 40 – 400 t/hr 400 m³/hr 450 m³/hr 800 m³/hr From 0.5...
Open the catalog to page 4All Schenck Process Holding GmbH catalogs and technical brochures
-
Smart Dust Collection Solution
12 Pages
-
Precise feeding solutions
4 Pages
-
FulFiller ®
8 Pages
-
MULTIBELT® Belt Weigher
8 Pages
-
CONiQ® Cloud
1 Pages
-
MULTIRAIL® BogieLoad pro
20 Pages
-
Pharmaceutical industry
10 Pages
-
MULTIRAIL®
16 Pages
-
Company overview
20 Pages
-
Your way to Schenck Process
4 Pages
-
We make processes work
20 Pages
-
Material Handling Solutions
8 Pages
-
Capabilities of Stock
8 Pages
-
LinaClass® screens
6 Pages
-
Screenex® screening media
24 Pages
-
CONiQ®
12 Pages
-
Enduro isolation springs
4 Pages
-
MCPP
12 Pages
-
ModuPlasma
8 Pages
-
Airlocks and Diverter Valves
6 Pages
-
MaxiStore®
8 Pages
-
SacMaster®
8 Pages
-
Screen Rebuild Program
4 Pages
-
Food industry
20 Pages
-
MultiTrain® Technology
4 Pages
-
Training that delivers!
38 Pages
-
Cement industry
16 Pages
-
MoveMaster® chain conveyors
8 Pages
-
TEDO Conveyors
18 Pages
-
ProPulse Industrial Air Filters
12 Pages
-
Drop forged chain
8 Pages
-
RoCon® Series 6
8 Pages
-
Sustainable Cement Production
10 Pages
-
Under the harshest conditions
16 Pages
-
SPro screen panels
12 Pages
-
LOGiQ® loading automation
10 Pages
-
Power industries
16 Pages
-
Tidal Series 5
6 Pages
-
Screen rebuilding
4 Pages
-
RotoScrew
2 Pages
-
Rotofeed Pneumatic Injector
2 Pages
-
DWB
4 Pages
-
MultiFlex
4 Pages
-
Stock Forry® ESP Products
8 Pages
-
LinaClass®
6 Pages
-
Air pollution control
4 Pages
-
Stock Valves
8 Pages
-
Product Overview
8 Pages
-
MULTIDOS® H - Weighfeeder
2 Pages
-
MULTIDOS® E - Weighfeeder
4 Pages
-
SacMaster
1 Pages
-
MULTIBELT®
1 Pages
-
MULTIDOS® VDP
1 Pages
-
Components and Standard Products
206 Pages
-
DISOCONT ®
4 Pages
-
INTECONT® PLUS
4 Pages
Archived catalogs
-
We make processes work
16 Pages
-
MULTIRAIL® WheelLoad
2 Pages
-
MULTIRAIL® WheelScan
2 Pages
-
MULTIRAIL® MultiBridge
2 Pages
-
MULTIRAIL® LiquidWeight
2 Pages
-
MULTIRAIL® LegalWeight
2 Pages
-
MULTIDOS® L
4 Pages
-
MULTIGRAV®
4 Pages
-
ProFlex® C
2 Pages
-
Mobile Touch Panel FSB
2 Pages
-
DISOMAT® Satus
4 Pages
-
DISOMAT® B plus Ex, Zone 1
4 Pages
-
INTECONT® Opus
4 Pages
-
weighing sensor
1 Pages
-
Rotary Force Exciters
4 Pages
-
Force exciters
4 Pages
-
MULTISTREAM® B
4 Pages
-
MULTICOR® R 450
4 Pages
-
MULTIDOS® E
4 Pages
-
MULTIDOS® M
4 Pages
-
Award Winning Solutions
6 Pages