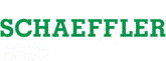

Catalog excerpts
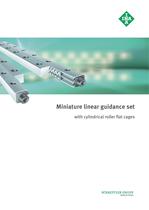
with cylindrical roller flat cages >
Open the catalog to page 1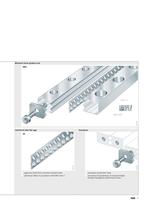
Miniature linear guidance set RWS > 172 746 Cylindrical roller flat cage > cage strip made from corrosion-resistant steel > end pieces made from steel > cylindrical rollers in accordance with DIN 5402-1 > end pieces for guideways of unequal length; fixing by hexagonal socket head screws >
Open the catalog to page 3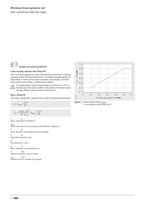
1,20,80,60,40,20 Design and safety guidelinesLoad carrying capacity and rating life > 1,0 The size of the guidance unit is determined by the load carrying capacity of the individual elements. The load carrying capacity is described in terms of the basic dynamic load rating C and the basic static load rating C > (dimension tables). For applications with temperatures in excess of +120 C, factors must be used to reflect reductions in the basic load ratings. Please ask for further information. > KHV k Basic rating life > 00,20,40,60,81,21,0 The basic rating life is determined using the...
Open the catalog to page 4
Static load safety factor Basic static moment rating M > 0x The static load safety factor S > indicates the security with regard to permissible permanent deformation in the bearing without affecting the guidance accuracy and smooth running of the bearing. It can be determined using the following formula:If high demands are placed on accuracy and smoothness of running, the static load safety factor should not be less than S The moments for rolling elements in an O arrangement can be determined using the following formulae: a > k = a > i + B C S ------= > > M = k +a ⋅ W P > > M k M 0x a k...
Open the catalog to page 5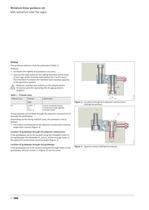
Preload The guidance systems must be preloaded (Table 1). Preload: ■ increases the rigidity and guidance accuracy ■ reduces the high loads on the rolling elements at the ends ofthe cage under moment load (about the Z and Y axes). Thistherefore increases the moment load carrying capacity ofthe guidance system.However, preload also influences the displacement resistance and the operating life of cage guidance systems. The guideways can be fixed through the adjacent construction or through the guideways. Depending on the fixing method used, the preload is set as follows: > d Table 1 Preload...
Open the catalog to page 6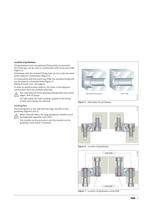
Location of guideways The guideways have counterbored fixing holes as standard. Thishole type can be used in combination with insert nuts ESM (Figure 5).Guideways with the standard fixing hole can be screw mounted to the adjacent construction (Figure 6).In combination with the insert nuts ESM, the standard fixing hole can be used as a threaded hole (Figure 7). Fitting of insert nuts: see page 8.In order to avoid location defects, the holes in the adjacent construction must be carefully deburred.The counterbores of the guideway fixing holes have sharp edges. Risk of injury!For high loads,...
Open the catalog to page 7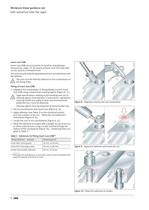
Insert nuts ESM Insert nuts ESM are accessories for location of guideways ( > 156 227 Accessories , page 13). By means of these nuts, this hole type can be used as a threaded hole. The nuts must be ordered separately and are included loose with the delivery.The nuts must be fixed by adhesive in the counterbores of the fixing holes. Fitting of insert nuts ESM ■ Degrease the counterbores in the guideway and the insert nuts ESM using conventional cleaning agents (Figure 8, ). Legal specifications relating to the handling and use of cleaning agents (manufacturers instructions, regulations...
Open the catalog to page 8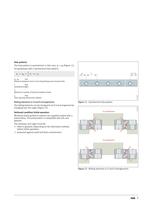
Hole patterns The hole pattern is symmetrical: In this case, a > L = a > R (Figure 11).For guideways with a symmetrical hole pattern: a == 12 > a L j L RL = aa L a > R --- L nj ֢˅() > L a L , a R mmDistance between start or end of guideway and nearest holeLmmGuideway lengthnMaximum number of pitches between holesj L mmHole spacing ( dimension tables ). 156 200 Rolling elements in O and X arrangements Figure 11 ַ Symmetrical hole pattern The rolling elements can be changed to an O or X arrangement by changing over the cages (Figure 12). > 156 201 Delivered condition/initial operation > O...
Open the catalog to page 9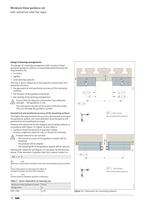
Design of bearing arrangements The design of a bearing arrangement with minature linear guidance guidance systems is essentially determined by the requirements for: ■ accuracy ■ rigidity > H ■ load carrying capacity.This has a direct influence on the adjacent construction and primarily concerns: ■ the geometrical and positional accuracy of the mounting surfaces > AAA ■ the location of the guidance elements > ttttt tt ■ the sealing of the bearing arrangement. Ensure that the adjacent construction has adequate strength VDI guideline 2230.The end pieces should not be used to limit the stroke....
Open the catalog to page 10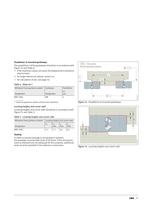
Parallelism of mounted guideways The parallelism t of the guideways should be in accordance with Figure 14 and Table 4: > t Not convex(for all machined surfaces) tC ■ If the maximum values are used, the displacement resistance may increase ■ For larger tolerances, please contact us. > b C ■ Table 4 Value for t For calculation of H, see page 10. > H Miniature linear guidance system Guideway Parallelism t 1) Designation Designation mRWS 1808RW5 Figure 14 Parallelism of mounted guideways > t 152 151 1) Value for guidance system set free from clearance. Locating heights and corner radii...
Open the catalog to page 11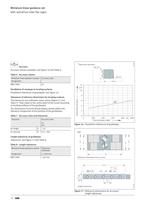
Permissible deviation 1000 Total guideway length Measured deviation > Reference dimensions for accuracy Length tolerances LC > 1 / n j > L 0,25 0,4 a j > L 152 168
Open the catalog to page 12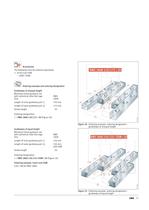
Accessories The following must be ordered separately: ■ Insert nuts ESMsuffix +ESM. Ordering example and ordering designationGuideways of unequal length 150 mmLength of outer guideway pair 175 mmStroke length20 Miniature linear guidance setwith cylindrical roller flat cageRWSSize1808Length of inner guideway pair Ordering designation:1 RWS 1808 150/175 20 (Figure 18). > 172 764 Figure 18 ַ Ordering example, ordering designation guideways of unequal length Guideways of equal length 150 mmLength of outer guideway pair 150 mmwith ESMStroke length20 Ordering designation:1 RWS 1808 150/150 +ESM...
Open the catalog to page 13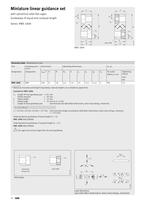
Dimension table Dimensions in mm Unit Guideway pair 1 and 2 Dimensions Mounting dimensions K > 1 , G > 1 Designation Designation L > max1) H B A > 2 h j > L a > L a > R C > 8 for screwDIN 912-12.9 Tightening torque max.Nm RWS 1808 RWT 350 8 18 3,5 7,9 25 12,5 12,5 3 M3 2,2C > 1) Maximum manufactured length of guideway. Special lengths are available by agreement. Example for RWS 1808: > 1 Length of inner guideway pair=125mmStroke required=20mmhStroke length=22mmzSafety range=10mm (4 z 10)LLength of outer guideway pair(see formula and table Main dimensions, basic load ratings, moments ).L =...
Open the catalog to page 14All Schaeffler Technologies AG & Co. KG catalogs and technical brochures
-
ProLink CMS
2 Pages
-
Always Following the Sun
12 Pages
-
Active Magnetic Bearing
4 Pages
-
RDDM Rotary Direct Drive Motors
106 Pages
-
FAG RS ? Robust and Fast
6 Pages
-
FAG Alignment Tools
36 Pages
-
Split Plummer Block Housings SNS
68 Pages
-
FAG SmartCheck
2 Pages
-
Customized Hubridization
20 Pages
-
Split plummer block housings SNV
84 Pages
-
Crossed roller bearings
67 Pages
-
Bearings for screw drives
106 Pages
-
Sealing rings
35 Pages
-
Sealed Spherical Roller Bearings
24 Pages
-
Spherical Roller Bearings E1
40 Pages
-
Tapered Roller Bearings E1
4 Pages
-
Single Row Ball Roller Bearings
18 Pages
-
Super Precision Bearings
243 Pages
-
Slewing rings
108 Pages
Archived catalogs
-
Triondur
2 Pages
-
FAG E1 Spherical Roller Bearings
28 Pages