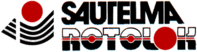
Group: ROTOLOK
Catalog excerpts
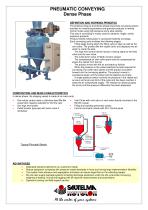
DEFINITION AND WORKING PRINCIPLE The positive pressure and dense phase pneumatic conveying system provides for transfering powdery and granular products in remote control mode using high pressure and a slow velocity. This way of conveying is mainly used for abrasive, fragile, and/or explosive products. Product transfer takes place in successive batches and plugs. Each conveying cycle includes the following stages: - Filling stage during which the filling valve is open as well as the vent valve. The product fills the vessel (tank) and displaces the air which is inside the tank. - The high level control device issues a closing signal to the feed valve and the vent valve. - The outlet pinch valve (if fitted) remains closed. - The compressed air inlet valve opens and the compressed air enters the vessel from the top. - The product mixes with the air and starts to fluidize. - When the pressure in the vessel reaches the level required for conveying, the outlet valve opens and the product is pushed forward into the conveying pipeline. The product moves in successive plugs until the vessel and the pipeline are empty. - A single pressure switch controls the pressure in the vessel and as soon as the pre-set limit of the cycle end has been reached, it stops the air compressed supply. The residual air allows purging the circuit until the pressure differential has been dispersed. COMPOSITION AND MAIN CHARACTERISTICS In dense phase, the shipping vessel is made of six main parts: • One robust carbon steel or stainless steel Blo-Bin vessel with capacity selected for the flow rate, • One high level probe • Outlet booster type pipe with pinch valve if necessary • Inlet Chute with vent valve or vent valve directly mounted to the Blo-Bin vessel. • Filling and isolating pneumatic valves • Control command cubicle with PLC Control panel Typical Principle Sketch ADVANTAGES • Dedicated solutions tailored to our customers needs. • Robust equipment complying with pressure vessel standards in force and having large implementation flexibility. • The system limits abrasion and segregation and does not require large filter on the collecting hopper. • We can also supply package systems including discharge equipment under the silo, pneumatic conveying, weighing & feeding, mixing and bagging with all required measurements and automations. • Operators training and field support service. At the center of your systems
Open the catalog to page 1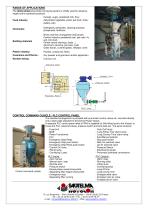
RANGE OF APPLICATIONS The dense phase pneumatic conveying system is chiefly used for abrasive, fragile and/or explosive products. Cereals, sugar, powdered milk, flour, Food industry dehydrated vegetable, pasta, pet-food, chips, pellets, salt) Chemicals: Building materials Plastic industry: Cosmetics and Pharma : Nuclear energy Detergents, pesticides, cleaning products, phosphates, fertilizers Bricks and tiles (manganese and baryte), Cement industry (powdered coal, pet coke, fly ash, kiln dust) Panels (wood shavings, loads...) Aluminium (alumina, pet coke, coal) Glass (borax, crushed...
Open the catalog to page 2All Sautelma Rotolok catalogs and technical brochures
-
Weigh belt feeder
2 Pages
-
General brochure
4 Pages
-
Double weight hoppers
1 Pages
-
Loss in weight feeder 1000
2 Pages
-
The DLF Belt weigh feeder
2 Pages
-
The DLN Belt weigh feeder
2 Pages
-
The MINI Belt weigh feeder
2 Pages
-
Bascule de circuit BCSR
2 Pages
-
TSRT
2 Pages
-
Loss in weight feeder DPP50
2 Pages
-
Loss in weight feeder DPP3J
2 Pages
-
Weighing Belt Conveyor
2 Pages