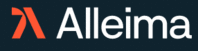
Catalog excerpts
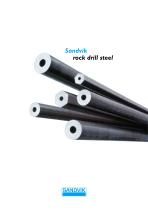
rock drill steel
Open the catalog to page 1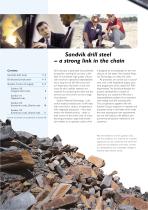
Sandvik drill steel – a strong link in the chain Contents: Sandvik drill steel Dedicated production Grades, Forms of supply Sanbar 20 Integral drill rods Sanbar 61 Tapered rods Sanbar 64 Extension rods, Shank rods Sanbar 23 Extension rods, Shank rods Sandvik and Sanbar are trademarks of Sandvik AB Drill rods take a great deal of punishment during their working life and only a drill steel of consistently high quality will provide maximum operational dependability and a long service life. We know from our experience that there is only one route for this: carefully selected raw materials for...
Open the catalog to page 2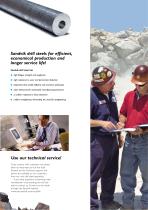
Sandvik drill steels for efficient, economical production and longer service life! Sandvik drill steel has G high fatigue strength and toughness G high resistance to wear and permanent distortion G properties that enable efficient and economic production G close tolerances for automated manufacturing processes G a uniform response to heat treatment G uniform straightness, eliminating the need for straightening Use our technical service! Close contact with customers has always been an important part of the total Sandvik service. Technical support and advice are available to our customers...
Open the catalog to page 3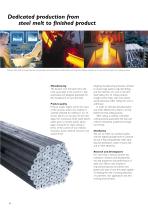
Dedicated production from steel melt to finished product Pictures from left: Scanning electron microscope, continuous bloom caster, billet mill, long-hole drilling, insertion of a core, rock drill steel mill, cooling process. Manufacturing The Sandvik rock drill steel mill is the most up-to-date in the world. It is fully automated and designed specifically for the manufacture of rock drill steel. Product quality Product quality begins at the very star t of the process, where raw material is carefully selected for melting in our 75 tonnes electric arc furnace. At the next stage, the...
Open the catalog to page 4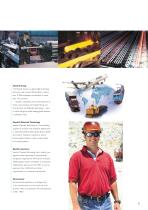
Sandvik Group The Sandvik Group is a global high technology enterprise with around 300 subsidiary companies, 37,000 employees and activities in more than 130 countries. Sandvik's operations are concentrated on its three core businesses of Tooling, Mining and Construction, and Materials Technology – areas in which the group holds leading global positions in selected niches. Sandvik Materials Technology Sandvik Materials Technology is a world-leading supplier of products with extensive added value in advanced stainless steels, special alloys, metallic and ceramic resistance materials as well...
Open the catalog to page 5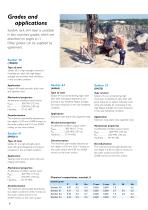
Grades and applications Sandvik rock drill steel is available in four standard grades, which are described on pages 6-11. Other grades can be supplied by agreement. Sanbar 20 (19HS20) Type of steel Sanbar 20 is a high strength chromiummolybdenum steel with high fatigue strength and excellent wear resistance in the as-rolled condition. Application Integral drill steels primarily (pilot rods and tapered rods). Mechanical properties As-delivered condition, typical values R p0.2 . . . . . . . . . 850 MPa (123 ksi) R m . . . . . . . . . . 1300 MPa (189 ksi) Hardness . . . . 37–43 HRC...
Open the catalog to page 6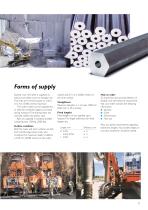
Forms of supply Sandvik rock drill steel is supplied as hollow, hot-rolled, round or hexagon bar. The ends are trimmed square to within 0.15 mm (0.006 inches) maximum. The outer surface can be supplied dry, or oiled for protection against corrosion during transport.The flushing holes are normally sealed with plastic caps. Bars are supplied in standard bundles containing max 1500 kg (3300 lbs). Surface condition Both the outer and inner surfaces are free from harmful slag marks, cracks and scratches.The maximum depth of defects is 0.20 mm (0.008 inches) on the outer surface and 0.15 mm...
Open the catalog to page 7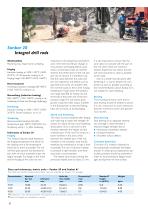
Sanbar 20 Integral drill rods Machinability Machining may require prior annealing. Forging Induction heating to 1000–1100°C (1830– 2010°F), 10–20 seconds, cooling in air. Forging range:1100–850°C (2010–1560°F). Heat treatment Annealing (induction heating) 850–900°C (1560–1650°F), cooling in air. Normalising (induction heating) 950–1050°C (1740–1920°F), cooling in air. Hardening of shank end (through hardening). Hardening Induction heating to 1000–1100°C (1830– 2010°F). Forced cooling in air or oil. Tempering Recommended hardness 50 HRC, temperature appr. 500°C (930°F)/0.5 hrs. Tempering...
Open the catalog to page 8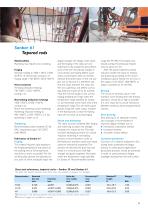
Sanbar 61 Tapered rods Machinability Machining may require prior annealing. Forging Induction heating to 1000–1100°C (1830– 2010°F), 10–20 seconds, cooling in air. Forging range: 1100–850°C (2010–560°F). Heat treatment Annealing (Induction heating). 730–780°C (1350–1440°F), cooling in air. Normalising (induction heating) 1000–1050°C, (1830–1920°F), cooling in air. Shank end hardening (case hardening) Hardening: Induction heating to 900–1000°C, (1650–1830°F ), 2–5 sec. quenching in water or oil. Tempering Recommended surface hardness 55–60 HRC, temperature appr. 150–250°C (300–480°F)....
Open the catalog to page 9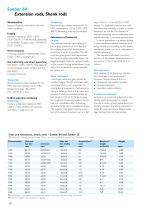
Sanbar 64 Extension rods, Shank rods Machinability Sanbar 64 can be machined in the hot rolled condition. Forging Induction heating to 1000–1100°C (1830–2010°F), 10–60 seconds, depending on dimension. Forging range: 1100–850°C (2010–1560°F). Heat treatment Annealing (induction heating) 680–720°C (1260–1330°F), cooling in air. Gas carburising and direct quenching 920–930°C (1690–1705°F).Time depends on the required carbon content and the case depth. Cooling in forced air. Tempering Recommended surface hardness 57–62 HRC and core hardness 36–44 HRC temperature appr. 180–230°C (355–450°F) for...
Open the catalog to page 10
Sanbar 23 Extension rods, Shank rods Machinability Sanbar 23 can be machined in the hot rolled condition. Forging Induction heating to 1000–1100°C (1830– 2010°F), 10–60 seconds, depending on dimension. Forging range: 1100–850°C (2010–1560°F). Heat treatment Annealing (induction heating). 720–770°C (1330–1420°F), cooling in air. Gas carburising and direct quenching 920–930°C (1690–1705°F).Time depends on the required carbon content and the case depth. Cooling in forced air. Tempering Recommended surface hardness 57–62 HRC and core hardness 36–44 HRC. Temperature appr. 180 to 230°C (355–...
Open the catalog to page 11All Sandvik Materials Technology catalogs and technical brochures
-
Sandvik 3R12
6 Pages
-
special strip steel
18 Pages
-
Sandvik diecutting products
8 Pages
-
Sandvik billets and blooms
10 Pages
-
Welding products
27 Pages
-
Solid and hollow bar
25 Pages