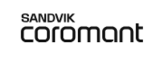

Catalog excerpts
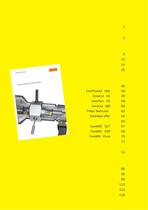
2 3 9 10 14 35 46 48 56 58 60 62 64 65 67 69 70 72 76 86 92 96 112 114 118 Contents Introduction 1 Basics in threads 2 Applications Threading methods Thread turning vs thread milling Thread Turning Thread Milling 3 Products Thread Turning CoroThread® 266 CoroCut® XS CoroTurn® XS CoroCut® MB T-Max Twin-Lock® Extended offer Thread Milling CoroMill® 327 CoroMill® 328 CoroMill® Plura Grade information 4 Troubleshooting 5 Technical reference Cutting data Programming Thread turning infeed recommendations External thread milling recommendations Formulas Inch/mm conversion table APPLICATION GUIDE Threading Thread turning and thread milling
Open the catalog to page 1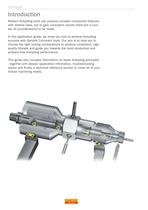
2 Introduction Introduction Modern threading tools can produce complex component features with relative ease, but to gain consistent results there are a number of considerations to be made. In this application guide, we show you how to achieve threading success with Sandvik Coromant tools. Our aim is to help you to choose the right tooling combinations to produce consistent, high quality threads and guide you towards the most productive and problem-free threading performance. This guide also includes information on basic threading principles - together with deeper application information,...
Open the catalog to page 2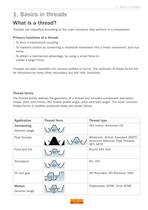
3 1. Basic in threads 1. Basics in threads What is a thread? Threads are classifi ed according to the main functions they perform in a component. Primary functions of a thread: • To form a mechanical coupling • To transmit motion by converting a rotational movement into a linear movement, and vice versa. • To obtain a mechanical advantage, by using a small force to create a larger force. Threads are also classifi ed into various profi les or forms. The selection of these forms will be infl uenced by many other secondary, but still vital, functions. Thread forms The thread profi le defi nes...
Open the catalog to page 3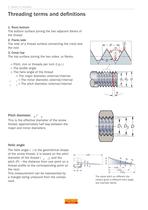
4 1. Basic in threads Threading terms and defi nitions 1. Root/bottom The bottom surface joining the two adjacent fl anks of the thread 2. Flank/side The side of a thread surface connecting the crest and the root 3. Crest/top The top surface joining the two sides, or fl anks. P = Pitch, mm or threads per inch (t.p.i.) ƒÒƒn= The profi le angle ƒÚƒn= The helix angle of the thread d / D = The major diameter, external/internal d1 / D1 = The minor diameter, external/internal d2 / D2 = The pitch diameter, external/internal Pitch diameter, d2 / D2 This is the effective diameter of the screw...
Open the catalog to page 4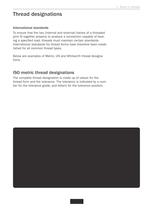
5 M10 x 1.25 5g6g M16 - 6h 1. Basic in threads Thread designations International standards To ensure that the two (internal and external) halves of a threaded joint fi t together properly to produce a connection capable of bearing a specifi ed load, threads must maintain certain standards. International standards for thread forms have therefore been established for all common thread types. Below are examples of Metric, UN and Whitworth thread designations. ISO metric thread designations The complete thread designation is made up of values for the thread form and the tolerance. The tolerance...
Open the catalog to page 5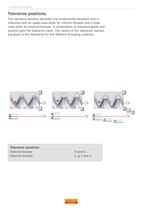
6 1. Basic in threads Tolerance positions The tolerance position identifi es the fundamental deviation and is indicated with an upper-case letter for internal threads and a lower case letter for external threads. A combination of tolerance grade and position give the tolerance class. The values of the tolerance classes are given in the standards for the different threading systems. Tolerance positions Internal threads H and G External threads h, g, f and e
Open the catalog to page 6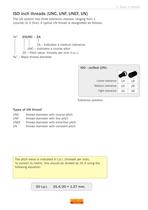
7 1A 1B 2A 2B 3A 3B ¼” 20UNC – 2A 1. Basic in threads The pitch value is indicated in t.p.i. (threads per inch). To convert to metric, this should be divided by 25.4 using the following equation: 20 t.p.i. „± 25.4/20 = 1.27 mm. ISO - unifi ed (UN): ISO inch threads (UNC, UNF, UNEF, UN) The UN system has three tolerance classes, ranging from 1 (course) to 3 (fi ne). A typical UN thread is designated as follows: Tolerance position Types of UN thread UNC thread diameter with course pitch UNF thread diameter with fi ne pitch UNEF thread diameter with extra-fi ne pitch UN thread diameter with...
Open the catalog to page 7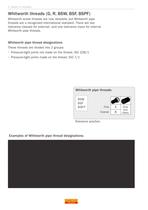
8 A B BSW BSF BSP.F ISO 228/1 G 1 ½ ISO 7/1 = Rp 1 ½ Rp 7/1 = Rc 1 ½ Rc 7/1 = R 1 ½ R 1. Basic in threads Whitworth pipe threads: Tolerance position Fine Only one Coarse class Whitworth threads (G, R, BSW, BSF, BSPF) Whitworth screw threads are now obsolete, but Whitworth pipe threads are a recognized international standard. There are two tolerance classes for external-, and one tolerance class for internal Whitworth pipe threads. Whitworth pipe thread designations These threads are divided into 2 groups: • Pressure-tight joints not made on the thread, ISO 228/1 • Pressure-tight joints made...
Open the catalog to page 8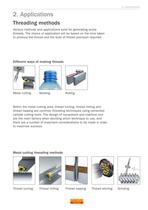
9 2. Applications 2. Applications Threading methods Various methods and applications exist for generating screw threads. The choice of application will be based on the time taken to produce the thread and the level of thread precision required. Different ways of making threads Molding Metal cutting threading methods Thread turning Thread milling Thread tapping Thread whirling Metal cutting Rolling Grinding Within the metal cutting area, thread turning, thread milling and thread tapping are common threading techniques using cemented carbide cutting tools. The design of component and machine...
Open the catalog to page 9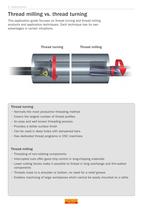
10 2. Applications Thread turning Thread milling Thread turning • Normally the most productive threading method • Covers the largest number of thread profi les • An easy and well known threading process • Provides a better surface fi nish • Can be used in deep holes with dampened bars • Has dedicated thread programs in CNC machines Thread milling • Threading of non-rotating components • Interrupted cuts offer good chip control in long-chipping materials • Lower cutting forces make it possible to thread in long overhangs and thin-walled components • Threads close to a shoulder or bottom, no...
Open the catalog to page 10All Sandvik Coromant catalogs and technical brochures
-
Solid Round Tools
36 Pages
-
CoroDrill® DS20
8 Pages
-
S205
2 Pages
-
CoroCut® QI
4 Pages
-
CoroDrill® 462 and 862
4 Pages
-
CoroMill® MH20
8 Pages
-
CoroPlus® Tool Supply
4 Pages
-
CoroTap® T200 and T300
2 Pages
-
CoroPlus® ProcessControl
8 Pages
-
Silent ToolsTM
12 Pages
-
CoroMill® concepts
12 Pages
-
CoroDrill® 880
8 Pages
-
CoroTap™ 100 -KM
8 Pages
-
CoroBore® 826
4 Pages
-
Small part machining
58 Pages
-
A great take-off
8 Pages
Archived catalogs
-
Hydro-Grip®
4 Pages
-
CoroTurn® SL
2 Pages
-
CoroThread™ 266
4 Pages
-
Composite
8 Pages
-
CoroMill®
8 Pages
-
A great take-off
8 Pages
-
CoroMill® 790
2 Pages
-
Bevel gear solutions
8 Pages
-
High pressure coolant brochure
48 Pages
-
Supplement 10.2
456 Pages
-
Product News 10.2
2 Pages
-
CoroMill® 690
4 Pages
-
Aerospace Frame
24 Pages
-
ISO S Geometries
4 Pages