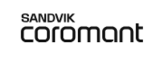

Catalog excerpts
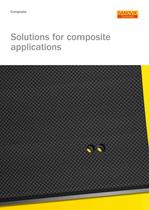
Solutions for composite applications Composite
Open the catalog to page 1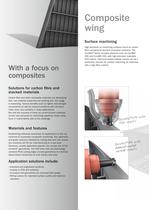
With a focus on composites Solutions for carbon fibre and stacked materials Carbon fibre and other composite materials are developing fast, new material properties are evolving and the usage is expanding. Various benefits such as lighter and stronger components as well as reduced problems with corrosion make them very suitalble in many applications. But with the success of these as constructional materials comes new demands on machining capability, where variations in machinability add to the challenge. Materials and features Establishing individual processes for applications is the...
Open the catalog to page 2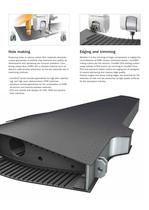
Edging and trimming Whether it is the trimming of larger components or edging the circumference of CFRP (carbon reinforced plastic), CoroMill® milling cutters are the solution. CoroMill 329 slotting cutters using carbide of PCD inserts for trimming or CoroMill Plura PCD and diamond coated cutters for edging are all designed to reduce splintering and improve edge quality. Positive angles and sharp cutting edges are essential for the reduction of heat and the production of high quality surfaces for the aerospace industry. Hole making Producing holes in various carbon fibre materials demands...
Open the catalog to page 3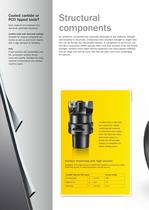
Structural componentsFor airframes, composites are especially developed to add stiffness, strength and durability to structures. Composites have excellent strength to weight ratio and can be formed into complicated shapes. In comparison to aluminium, carbon fibre composites (CFRP) typically have more than fourteen times the tensile strength; nineteen times lower thermal expansion; five times greater stiffness and yet weigh only half as much. But they are also much more challenging to machine. CoroMill®590 with PCD inserts Surface milling Cutting speed Vc m/min 300 Depth of cut ap mm 2.5...
Open the catalog to page 4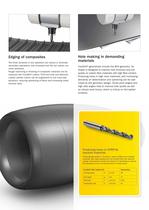
Edging of composites The finish achieved in one operation can reduce or eliminate secondary operations, and increased tool life can reduce machine downtime. Rough machining or finishing of composite materials can be improved with CoroMill®cutters. PCD end mills and diamondcoated carbide cutters can be engineered to suit most aapplications, reducing splintering of fibres and increasing metal removal rates. Producing holes in CFRP/AL stacked materials Producing high quality ¼” (6.35mm) holes in CFRP and AL stacked materials, was made possible with the CoroDrill® 854 with diamond coating....
Open the catalog to page 5
Tooling solutions A varied selection of tool geometries, designs, as well as one or two-hit process solutions can drastically improve the production process. Product solutions from Sandvik Coromant include carbide and brazed or vein type diamond drills, counter-sunk tools as well as reamers for demanding surface finish and hole tolerance. Application demandsStructural components such as composite wing - including spars, stringers and skins - are made out of variations of carbon fibre and matrix materials, which result in the need for individual tooling solutions. Other demanding structures,...
Open the catalog to page 6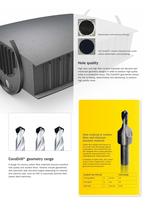
CoroDrill® Vein PCD drill Hole making Cutting speed Vc m/min 12 Drill depth ap mm 25 Feed rate fn mm/rev 0.05 Hole making in carbon fibre and titaniumstacked material Carbon fibre stacked with titanium is one of the most demanding material combinations. The CoroDrill PCD vein drill, designed with a unique geometry, was able to raise productivity in this challenging hole making application. A sandwich of carbon fibre, with a thickness of 15 mm, layered with a 10 mm sheet of titanium was machined with good security and precision. CoroDrill® geometry range A design for various carbon fibre...
Open the catalog to page 7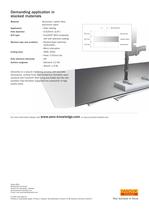
aluminium Ø 9.525 mm carbon fibre 20 mm aluminium 20 mm 20 mm Demanding application in stacked materials Material: Aluminium, carbon fibre, aluminiumstack Application: – Hole making Hole diameter: – 9.525 mm (3/8”) Drill type: – CoroDrill® 854 composite drill with diamond coating Machine type and condition: – Positive -feed machines (pneumatic) – Micro lubrication Cutting data: – RPM: 2000 – Feed: 0.03 mm/rev Hole tolerance demands: – H9 Surface rougness: – Demand: 3.2 Ra – Result: 1.6 Ra Demands on a secure machining process with accurate dimensions, surface finish and limited burr...
Open the catalog to page 8All Sandvik Coromant catalogs and technical brochures
-
Solid Round Tools
36 Pages
-
CoroDrill® DS20
8 Pages
-
S205
2 Pages
-
CoroCut® QI
4 Pages
-
CoroDrill® 462 and 862
4 Pages
-
CoroMill® MH20
8 Pages
-
CoroPlus® Tool Supply
4 Pages
-
CoroTap® T200 and T300
2 Pages
-
CoroPlus® ProcessControl
8 Pages
-
Silent ToolsTM
12 Pages
-
CoroMill® concepts
12 Pages
-
CoroDrill® 880
8 Pages
-
CoroTap™ 100 -KM
8 Pages
-
CoroBore® 826
4 Pages
-
Small part machining
58 Pages
-
A great take-off
8 Pages
Archived catalogs
-
Hydro-Grip®
4 Pages
-
CoroTurn® SL
2 Pages
-
CoroThread™ 266
4 Pages
-
CoroMill®
8 Pages
-
A great take-off
8 Pages
-
CoroMill® 790
2 Pages
-
Bevel gear solutions
8 Pages
-
Threading Application guide
118 Pages
-
High pressure coolant brochure
48 Pages
-
Supplement 10.2
456 Pages
-
Product News 10.2
2 Pages
-
CoroMill® 690
4 Pages
-
Aerospace Frame
24 Pages
-
ISO S Geometries
4 Pages