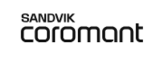

Catalog excerpts
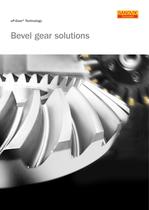
Bevel gear solutions uP-Gear®Technology
Open the catalog to page 1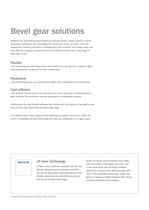
Bevel gear solutions Whether you manufacture bevel gears for printing presses, power plants or marine propulsion equipment, the challenges are usually the same: accuracy, cost and productivity. Sandvik Coromant, in collaboration with machine tool builder Heller can now offer you a flexible, productive and cost efficient solution for a wide range of bevel gear sizes. Flexible - the multi-purpose machining centre, the machine can be used for a variety of gear tooth geometries, as well as for other components. Productive - the machining time is up to three times higher with a traditional end...
Open the catalog to page 2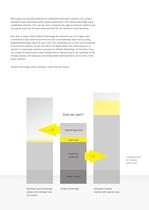
Standard 5-axis machining centers with standard end mill cutters. uP-Gear Technology machining time Dedicated hobbing machine with special tools. *example valid for medium batch sizes other costs machine write-off tool cost Cost per part* x 3 x 2 Bevel gears are typically produced in a dedicated bevel gear machine or by using a standard 5-axis machining centre, where productivity is the obvious advantage using a dedicated machine. The cost per part is however very high as both the machine and the special tools are far more expensive than for the standard 5-axis machines. Now, that is...
Open the catalog to page 3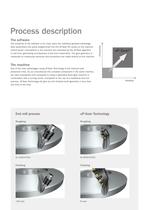
The software The simplicity of the software is for many users the individual greatest advantage. Gear parameters are easily programmed into the uP-Gear NC cycles on the machine control panel. Calculations in the machine are controlled by the uP-Gear algorithm in real time, generating simultaneous 5-axis tool movements. The gear geometry is measured on measuring machines and corrections are made directly on the machine. The machine One of the main advantages using uP-Gear Technology is the reduced total production time. As you manufacture the complete component in the same machine, you save...
Open the catalog to page 4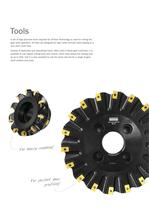
A set of high precision tools required for uP-Gear Technology is used for milling the gear tooth geometry. All tools are designed for high metal removal rates leading to a very short cycle time. Instead of dedicated and specialised tools, often used in bevel gear machines, it is possible to use regular milling tools and inserts, which help reduce the tooling cost by up to 50%. And it is also possible to use the same tool set for a range of gear tooth profiles and sizes. For heavy roughing! For perfect gear profiling! Tools
Open the catalog to page 5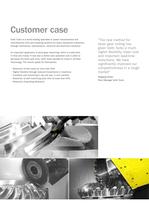
Customer case Voith Turbo is a world leading specialist in power transmissions and manufactures drive and breaking systems for heavy equipment industries, through mechanical, hydrodynamic, electrical and electronic solutions. An important application is bevel gear machining, which is costly both in time and money. It was also a bottle neck operation and in order to decrease the total cycle time, Voith Turbo decided to invest in uP-Gear Technology. The results speak for themselves: • Reduction of tool costs by more than 50% • Higher flexibility through reduced investments in machines •...
Open the catalog to page 6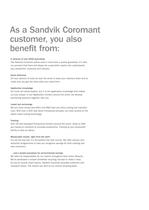
As a Sandvik Coromant customer, you also benefit from: A network of over 5000 specialists The Sandvik Coromant yellow coat is more than a quality guarantee. It’s also our promise that there will always be a specialist nearby who understands your production, business and industry. Quick deliveries 24 hour delivery of tools all over the world to keep your inventory down and to make sure you get the tools when you need them. Application knowledge Our tools are world leaders, but it is the application knowledge that makes us truly unique. In our Application Centers around the world, we develop...
Open the catalog to page 7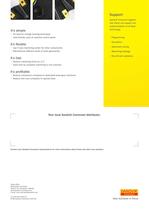
Your local Sandvik Coromant distributor: Contact your Sandvik Coromant representative for more information about these and other new solutions. It’s simple • No need to change existing processes • User-friendly input at machine control panel It’s flexible • Use 5-axis machining center for other components • Manufacture different kinds of tooth geometries It’s fast • Reduce machining times by 1/3 • Save time by complete machining in one machine It’s profitable • Reduce investment compared to dedicated bevel gear machines • Reduce tool cost compared to special tools Support Sandvik Coromant...
Open the catalog to page 8All Sandvik Coromant catalogs and technical brochures
-
Solid Round Tools
36 Pages
-
CoroDrill® DS20
8 Pages
-
S205
2 Pages
-
CoroCut® QI
4 Pages
-
CoroDrill® 462 and 862
4 Pages
-
CoroMill® MH20
8 Pages
-
CoroPlus® Tool Supply
4 Pages
-
CoroTap® T200 and T300
2 Pages
-
CoroPlus® ProcessControl
8 Pages
-
Silent ToolsTM
12 Pages
-
CoroMill® concepts
12 Pages
-
CoroDrill® 880
8 Pages
-
CoroTap™ 100 -KM
8 Pages
-
CoroBore® 826
4 Pages
-
Small part machining
58 Pages
-
A great take-off
8 Pages
Archived catalogs
-
Hydro-Grip®
4 Pages
-
CoroTurn® SL
2 Pages
-
CoroThread™ 266
4 Pages
-
Composite
8 Pages
-
CoroMill®
8 Pages
-
A great take-off
8 Pages
-
CoroMill® 790
2 Pages
-
Threading Application guide
118 Pages
-
High pressure coolant brochure
48 Pages
-
Supplement 10.2
456 Pages
-
Product News 10.2
2 Pages
-
CoroMill® 690
4 Pages
-
Aerospace Frame
24 Pages
-
ISO S Geometries
4 Pages