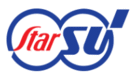
Catalog excerpts
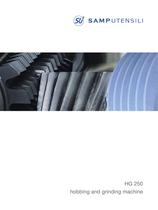
hobbing and grinding machine
Open the catalog to page 1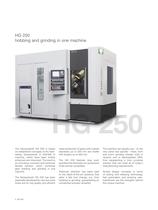
hobbing and grinding in one machine on established concepts of the best- machine, which have been further enhanced and improved. The result is an innovative, compact and extremely flexible solution, which combines gear hobbing and grinding in one especially developed for very low cycle times and for top-quality and efficient mass production of gears with outside The HG 250 features dual work spindles that eliminate non-productive times almost completely. Particular attention has been paid to the state-of-the-art solutions that allow a fast tool change, e.g. from hobbing to grinding,...
Open the catalog to page 2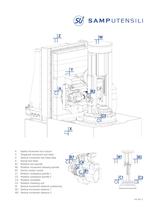
X Radial movement tool column Y Tangential movement tool head Z Vertical movement tool head slide A Swivel tool head B1 Rotation tool spindle B2 Rotation movement dressing spindle B7 Swivel coolant nozzle C1 Rotation workpiece spindle 1 C2 Rotation workpiece spindle 2 C4 Rotation checking unit W Vertical movement tailstock positioning W1 Vertical movement tailstock 1 W2 Vertical movement tailstock 2
Open the catalog to page 3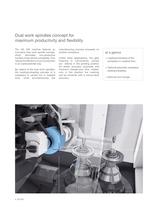
Dual work spindles concept for maximum productivity and flexibility innovative dual work spindle concept, which eliminates non-productive auxiliary times almost completely, thus raising the efficiency of your production By means of the dual work spindles, workpiece is carried out in masked time, while simultaneously the manufacturing process proceeds on another workpiece. Unlike other applications, the gear meshing is conveniently carried out directly in the grinding position for better accuracy purposes and minimum change-over time. Indeed, only in this position the meshing can be achieved...
Open the catalog to page 4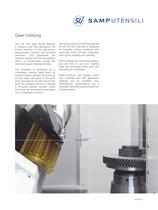
Gear hobbing The HG 250 gear centre features a machine bed that represents the further evolution of the well-known Samputensili hobbing and grinding machines. This guarantees the machine rigidity and thermal stability, which is fundamental during the demanding gear hobbing process. completely internal, steel shell. Its inclined planes prevent the build-up of chip nests and swarf in the work area, and special nozzles ensure that even the smallest amount of residue is removed without contact. Chips and swarf are evacuated immediately The very powerful and stiff tool spindle for toughest...
Open the catalog to page 5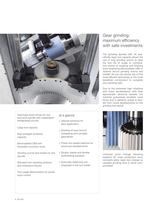
Gear grinding: maximum efficiency with safe investments The grinding spindle with its spe- cifically large tool capacity allows the use of long grinding worms to raise the tool life of single or combina- tion worms of roughing and finishing tools employing electroplated CBN or ceramic bound grinding worms and wheels. So you can always rely on the most efficient technology or the most beneficial combination to complete your grinding task. Due to the extremely high rotational and linear accelerations with their appropriate absolute speeds the machine guarantees excellent cycle times and is...
Open the catalog to page 6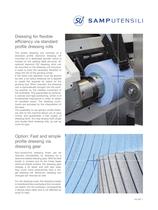
profile dressing rolls The profile dressing unit consists of a standard profile diamond dressing roll mounted on a dedicated spindle, which is located on the rotating table structure. An optional diamond OD dressing stick can be mounted on the dressing unit structure, in order to have the necessary flexibility to dress the OD of the grinding wheel. If the tooth root diameter must be ground as well, a tip radius dressing roll is applied to create the required tip radius on the grinding tool. When required, the dressing unit is automatically brought into the work- ing position by the rotating...
Open the catalog to page 7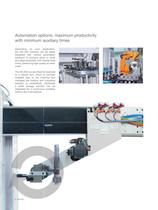
Automation options: maximum productivity with minimum auxiliary times Depending on your application, equipped with various automation solutions to produce parts in small and large quantities, with shorter lead times, preserving high quality at lower to a robotic arm, which is normally installed next to the machine and manages the loading and unloading process of workpieces. Optionally a pallet storage solution can be integrated for a continuous workflow
Open the catalog to page 8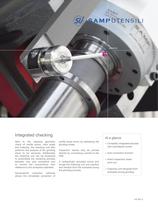
Integrated checking Next to the classical geometry check of profile errors, helix angle and indexing, the checking unit also performs the analysis of the grinding stock to be removed. Additionally the checking unit can be employed to automatize the centering process between tool and workpiece and to control the concentricity with reference to the workpiece diameter. Samputensili correction software allows the immediate correction of profile slope errors by redressing the grinding wheel. Inspection results may be printed directly by connecting a printer to the A hydraulically actuated swivel...
Open the catalog to page 9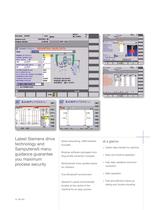
Latest Siemens drive Samputensili menu guidance guarantee process security Direct networking, USB interface Modular software packages inclu- ding profile correction modules Samputensili menu-guided opera- True Windows® environment + Faster data transfer to machine + Easy and intuitive operation + Fast data validation and error Operator's panel convenientely + Fast and efficient online UP" located at the centre of the datin9 and trouble-shooting machine for an easy access.
Open the catalog to page 10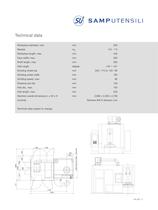
Technical data Helix angle Grinding wheel width Machine overall dimensions L x W x H Siemens 840 D Solution Line
Open the catalog to page 11
Samputensili Beijing Room 1801/1802, Jing Tai Tower 5200 Prairie Stone Parkway, Suite 100 Samputensili GmbH 4 MA- 319 Sihwa Industrial Complex 703-12, Sung-Gok Dong An-San City Samputensili do Brasil Ltda. Samputensili France S.a.r.l. 42000 Saint Etienne Cedex SSS^ft Maccaferri
Open the catalog to page 12All SAMPUTENSILI catalogs and technical brochures
Archived catalogs
-
SU_Mfg-prg
8 Pages
-
Samputensili_Tools
24 Pages
-
Tool
24 Pages
-
G-H-series
24 Pages
-
G 250 / G 450
12 Pages
-
GS 400
8 Pages
-
HRG 350
4 Pages
-
S 375 G
4 Pages
-
ASB 400
6 Pages
-
HG1200-2400
20 Pages
-
BK_H-series
12 Pages
-
S_800_S_1200_S_1600_S_2000
6 Pages
-
H80-200
20 Pages
-
H250-800CD
28 Pages
-
Master gears
6 Pages
-
CBN-plated grinding tools
6 Pages
-
Shaper Cutters
8 Pages
-
Solid-Steel and Carbide Hobs
8 Pages