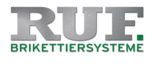

Catalog excerpts
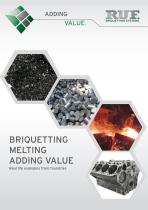
BRIOUETTING SYSTEMS ADDING VALUE Real life examples from foundries
Open the catalog to page 1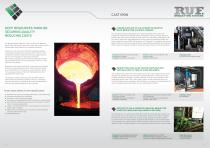
CAST IRON KEEP RESOURCES INHOUSE SECURING QUALITY REDUCING COSTS Ruf Maschinenbau GmbH & Co. KG is a family run business, which made the decision over thirty years ago to focus on the development and production of briquetting systems. Today there are more than 3,700 Ruf briquetting systems in operation, spread across more than 100 countries. They c ompress fine particle materials like chips, sludge and dust, which are the residuals of industrial processing. We roduce briquetting systems with throughputs between p 30 and 4,800 kg/hour for the briquetting of cast iron, steel, a luminium...
Open the catalog to page 2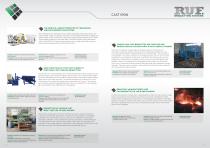
CAST IRON THE WORLD‘S LARGEST PRODUCER OF CRANKCASES USES RUF BRIQUETTING SYSTEMS The components are manufactured in a highly automated production process. The chips created, which are coated in emulsions, are briquetted and these briquettes are melted in the cupola furnace with a proportion of the charge make-up of up to 20%. The briquetting capacity in the main plant is 20,000 tons/year, and at the branch plant it is 18,000. All of the purchased systems are running successfully and have amortised themselves within a short period of time. Customer: Supplier to the automotive industry,...
Open the catalog to page 3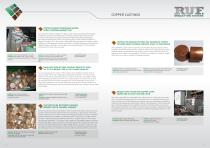
COPPER CASTINGS COPPER FOUNDRY PROCESSES IMPURE SCRAP THROUGH BRIQUETTING The customer produces copper cast alloys using various processes like horizontal continuous casting, sand casting and centrifugal casting. Chips produced from in-house mechanical processing as well as purchased chips (high percentage) have been briquetted since 2007. The starting point of 3-4% residual moisture is r educed to approx. 1% in this process. Briquettes make storage much simpler, enable p roblem-free charging and increase metal yield. An added advantage of the reduced residual moisture content is the...
Open the catalog to page 4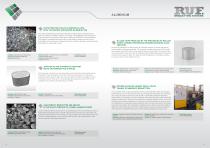
CHIPS FROM HIGH VALUE ALUMINIUM ALLOYS WITH TIN CONTENT ARE MELTED AS BRIQUETTES Dry chips created during production have been compressed to briquettes since 2011 on a system providing a capacity of 55 kg/h. The briquettes have a density of 2 kg/l and can be recycled at a rate up to a maximum of 25% of a charge make-up. The charge is complemented with ingots in the empty furnace. Decisive for the p rofitability is the economic utilisation of the tin content in the alloy, which has led to amortisation in well under a year. Customer: Automotive and mechanical engineering supplier, Middle...
Open the catalog to page 5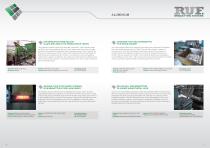
CHIP BRIQUETTES FROM DIE-CAST ALLOYS ARE USED IN THE PRODUCTION OF INGOTS The customer produces ingots from secondary Aluminium. Chip briquettes make up 30% of the charge make-up, the rest is bolt material and scrap from extruded p rofiles. After pressing the briquettes have a residual moisture level of around 3%. The level is reduced even further to about 1% through drying (just by ambient air) before they are transported to the furnace. The customer is using a briquetting system with a capacity of 450 kg/h. The system was commissioned in 2002 and has been running to the customer‘s...
Open the catalog to page 6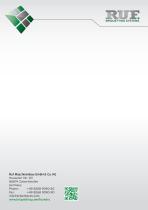
BRIQUETTING SYSTEMS
Open the catalog to page 7All RUF. BRIQUETTING SYSTEMS catalogs and technical brochures
-
FORMIKA
4 Pages
-
image-brochure
16 Pages
-
Image brochure RUF EN
16 Pages
-
Brochure en
2 Pages
-
RUF_Briquetting of Biomass
2 Pages
-
RUF Recycling Projects
8 Pages
-
RUF Briquetting Systems
8 Pages