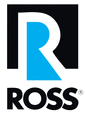
Catalog excerpts
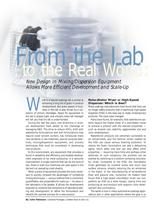
From the La > totheRealWorld: New Design in Mixing/Dispersion EquipmentAllows More Efficient Development and Scale-Up b > W ork in a typical coatings lab is aimed atachieving a long list of goals in productdevelopment. But every aspect of busi-ness in the lab is also driven by a col-lection of chronic shortages. Space for equipment inthe lab is always tight, and virtually every lab manager will tell you that his lab is under-funded.During the last few years, new directions in prod-uct development have added to the challenge ofmanaging R&D. The drive to reduce VOCs, both withwaterborne formulations and with formulations that require lower solvent content, has introduced manynew variables in raw materials, special-purpose addi-tives, mixing/dispersion equipment, and processtechniques that must be considered in developingnew products.In this environment, any equipment that provides aboost in versatility and efficiency, and enables develop-ment engineers to be more productive, is a welcomeimprovement. A single machine that can do the work oftwo, three or even four machines can save space in the lab and cut operating costs sharply.When a piece of equipment provides the tools neces-sary to quickly compare the advantages of competingmixing techniques using a method that is controlled,quantifiable, and projectable for scale-up ח its value in the laboratory is far greater. It allows the developmentengineer to combine two dimensions of laboratory test-ing and development: to refine the formulation and identify the optimal process for a new product. Rotor/Stator Mixer or High-Speed Disperser: Which is Best? Many coatings manufacturers have found that they canno longer safely presume that a traditional high-speeddisperser (HSD) is the best way to make contemporaryproducts. The rules have changed.Many have found, for example, that waterborne sys-tems require the higher shear of a rotor/stator mixer to achieve a product with the desired properties such as droplet size, stability, agglomerate size and color development.Waterborne products are extremely vulnerable toair entrainment, and the familiar vortex created by the HSD can cause serious foaming problems. Toreduce the foam, formulators can add a defoamingagent, which adds cost and can also affect otherproperties ח requiring more time and perhaps otheradditives. In such situations, the problem can be averted by switching to a bottom-vortexing rotor/sta-tor mixer. Compared to the HSD, the rotor/statormixer generates an inverted vortex and much lesssurface violence, sharply reducing the air entrainedin the batch. In the manufacturing of solventborne flexo and gravure inks, numerous ink makers havefound that a high-speed rotor/stator mixer can out-perform an HSD by a wide margin, saving time andproducing an end-product with superior color devel-opment and consistency.The same is true in many automotive-coatings appli-cations and in other applications where the goal is to By John Paterson / General Manager, Charles Ross & Son Co. size="-5">
Open the catalog to page 1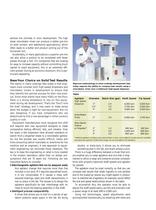
achieve the ultimate in color development. The highshear rotor/stator mixer can produce a better pre-mix (in both solvent- and waterborne applications), which often leads to a better end product coming out of the horizontal mill. Incidentally, in many applications a superior pre-mixcan also allow a product to be completed with fewerpasses through a mill. For companies that are looking for ways to increase capacity without committing muchcapital to plant equipment, this is an extremely effi- cient answer. During an economic downturn, this is par- ticularly appealing. > The reality in many...
Open the catalog to page 2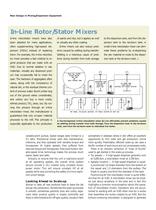
New Design in Mixing/Dispersion Equipment In-line rotor/stator mixers have alsobeen adopted for many applications,often supplementing high-speed dis-persers (HSDs) instead of replacing them. For example, the in-line rotor/sta-tor mixer provides a fast method to re- grind products that are made with an HSD. Due to normal variation in rawmaterials, virtually any dispersed prod-uct may occasionally fail to meet the spec. The hardness of aggregates often varies, along with the consistency ofnatural oils, or the residual chlorine con- tent of process water. Burnt umber dugout of the ground...
Open the catalog to page 3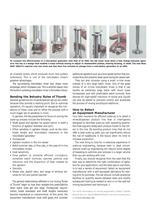
To compare the effectiveness of a rotor/stator generator with that of an HSD, the lab mixer must allow a fast change between agita-tors. The key is a design that enables a swap without having to adjust or disassemble pulleys, bearing housing, or shaft. The new RossHSM 100LH-2 requires only two tools and less than five minutes to change from a rotor/stator generator to an HSD. For more information on mixing equipment, contact CharlesRoss & Son Co., phone 800/243.ROSS; visit www.mixers.com; or Circle Number 94 . >
Open the catalog to page 4All ROSS Mixers catalogs and technical brochures
-
HSM-100LCI-T
2 Pages
-
Vertical Blender
2 Pages
-
DCB
1 Pages
-
VCB
1 Pages
-
Three Roll Mill
1 Pages
-
CDA
1 Pages
-
PVM
1 Pages
-
Series700
2 Pages
-
Series500
1 Pages
-
Series100
1 Pages
-
Series400
1 Pages
-
Discharge System
1 Pages
-
High Viscosity Disperser
2 Pages
-
Ross High Speed Disperser
2 Pages
-
High Shear Mixers
16 Pages
-
Blenders
12 Pages