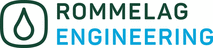

Catalog excerpts
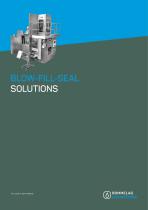
FILLING YOUR NEEDS
Open the catalog to page 1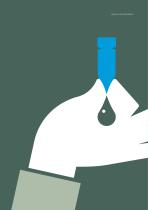
ROMMELAG ENGINEERING
Open the catalog to page 2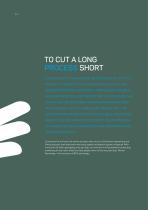
TO CUT A LONG PROCESS SHORT IT’S BEEN OVER 50 YEARS SINCE WE FIRST CAME UP WITH THE PERFECT ALTERNATIVE TO CONVENTIONAL LIQUID FILLING PROCESSES FOR OUR CUSTOMERS – PARTICULARLY THOSE IN THE PHARMACEUTICAL SECTOR. OUR AIM? TO MAKE SURE THAT EVERY LAST PRECIOUS DROP IS PACKAGED MORE RELIABLY, MORE FLEXIBLY, AND IN A MORE USER-FRIENDLY WAY. IT IS BASED ON THIS PRINCIPLE THAT BLOW-FILL-SEAL TECHNOLOGY CAME TO LIFE: THE WORLD’S FIRST ASEPTIC FILLING PROCESS OF ITS KIND FOR LIQUIDS, SEMISOLIDS, AND EVEN SOME HIGHLY SENSITIVE PRODUCTS. Customers from all over the world now place their trust in...
Open the catalog to page 3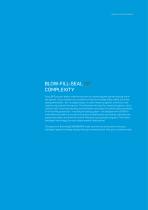
ROMMELAG ENGINEERING BLOW-FILL-SEAL OR COMPLEXITY Every BFS process begins with the extrusion of a sterile polymer parison directly within the system. Once complete, the container can then be moulded, filled, sealed, and immediately demoulded – all in a single process, in a self-contained system, and without the need for any external intervention. This eliminates the need for expensive logistics, not to mention time-consuming cleaning and sterilization processes for prefabricated containers. All of the filling processes – including the dosing system – are designed with CIP/SIP in mind. What...
Open the catalog to page 4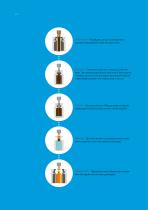
EXTRUDING – The polymer parison is extruded from granulate and positioned inside the open mould. BLOWING – The mould closes and, in doing so, welds the base. The mandrel is positioned on the neck of the container and blows sterile air into the parison to create the desired shape. Small containers are created using a vacuum. FILLING – The exact amount of filling as measured by the dosing system is fed into the container via the mandrel. SEALING – Once the mandrel is removed, the head mould comes together to form the desired closure type. DEMOULDING – Opening the mould releases the container...
Open the catalog to page 5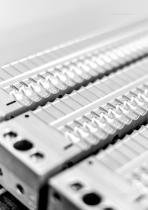
ROMMELAG ENGINEERING
Open the catalog to page 6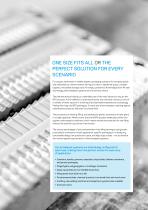
ONE SIZE FITS ALL OR THE PERFECT SOLUTION FOR EVERY SCENARIO For anyone interested in reliable aseptic packaging solutions for bringing liquids and semisolids to market without having to invest in additional space, complex logistics, and added storage costs for empty containers, Rommelag’s blow-fill-seal technology and bottelpack systems are the obvious choice. The pharmaceutical industry is undeniably one of the main sectors to rely on the BFS process. And in addition to pharmaceuticals, the chemical industry is one of a number of other sectors in which liquid and semisolid materials are...
Open the catalog to page 7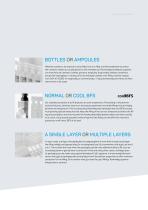
ROMMELAG ENGINEERING BOTTLES OR AMPOULES Whether a bottle or an ampoule is to be filled, how it is filled, and what additional functions the container needs are usually based on the intended use. Rommelag’s bottelpack systems can manufacture canisters, bottles, parisons, ampoules, drop bottles, bellows containers, and portion packaging in a variety of forms and plastic blends, with filling volumes ranging from 0.04 to 10,000 ml, aseptically or conventionally – fully automatically and without human intervention in all cases. NORMAL OR COOL BFS Our standard procedure is to fill products at...
Open the catalog to page 8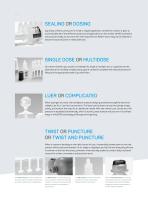
SEALING OR DOSING Eye drops, inhalers, products for rectal or vaginal application, ointments, creams, or gels: to accommodate all of the different products and applications on the market, all BFS containers are produced ready to use and in line with requirements. What’s more, they can be tailored to become functional parts in medical devices. SINGLE DOSE OR MULTIDOSE No matter whether your product is intended for single or multiple use, our systems are the ideal choice for moulding virtually every type of container complete with the precise level of filling and the appropriate seals to go...
Open the catalog to page 9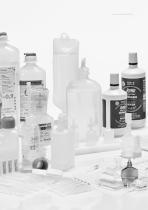
ROMMELAG ENGINEERING
Open the catalog to page 10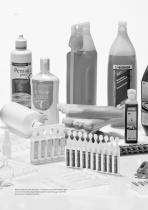
Bottles, ampoules, seals, applicators – virtually any conceivable container type can be manufactured using bottelpack systems. Just the way you want them. Just how your customers need them.
Open the catalog to page 11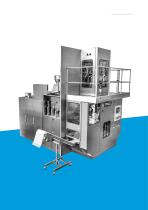
ROMMELAG ENGINEERING
Open the catalog to page 12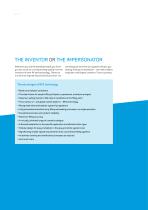
THE INVENTOR OR THE IMPERSONATOR Wherever you see the bottelpack label, you know you can count on uncompromising quality from the inventors of blow-fill-seal technology. Thanks to our German engineering and Swiss precision, we can always be sure that our systems will give you exactly what you’re looking for – from the smallest ampoule to the largest container. That’s a promise. Break-proof plastic containers The ideal choice for aseptic filling of liquids, suspensions, emulsions and gels Maximum safety thanks to ISO class 5 conditions at the filling point The inventor of – and global market...
Open the catalog to page 13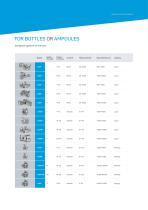
ROMMELAG ENGINEERING bottelpack systems: an overview System Number Number Container Filling volume (ml) Output (items/hour) Category
Open the catalog to page 14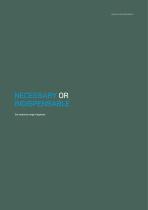
ROMMELAG ENGINEERING NECESSARY OR INDISPENSABLE Our extensive range of systems
Open the catalog to page 16
ROMMELAG ENGINEERING TOTALLY SATISFIED OR ABSOLUTELY ECSTATIC For us, there’s no doubt about it: you won’t find a better, more reliable, or cost-effective solution for packaging liquids and semisolids than a Rommelag bottelpack system. And if you’re looking for premium quality packaging that is always sure to get the job done, we have another trick up our sleeve: our bottelpack range now comes complete with a cap welding machine and various inspection systems. They can either be seamlessly integrated into the production process or installed as outstanding stand-alone solutions in their own...
Open the catalog to page 18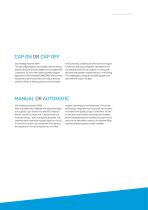
ROMMELAG ENGINEERING CAP ON OR CAP OFF Cap welding machine (SM) The specially designed cap welding machine allows plastic caps (ports) to be welded onto moulded BFS containers. To cover the widest possible range of applications, Rommelag ENGINEERING offers these machines as semi-automatic and fully automatic solutions. Both of these systems come complete with automatic unloading machines and conveyors. Customers looking to integrate a bottelpack and cap welding machines can expect a turnkey solution that has passed comprehensive in-line testing. The challenges to integrate multiple systems...
Open the catalog to page 20All Rommelag catalogs and technical brochures
-
FLEX STANDARD
12 Pages
-
FLEX PHARMA
12 Pages
-
CMO
16 Pages
-
HVLD Leak Detector
4 Pages
-
Rommelag Products & Services
13 Pages
-
SM 950, 954, 955, 965
4 Pages
-
bottelpack® type 430
2 Pages
-
bottelpack® type 364
1 Pages
-
bottelpack® type 312M
1 Pages
-
bottelpack® type 460-15
1 Pages
-
Bottelpack® type 460-20
1 Pages
-
Bottelpack® type 461-14
1 Pages
-
bottelpack® 360M
1 Pages
-
bottelpack® 324M
1 Pages
-
bottelpack® 321M
1 Pages
Archived catalogs
-
bottelpack® 4010M
1 Pages
-
bottelpack® 305M
1 Pages
-
bottelpack® type 3012M
1 Pages
-
bottelpack® type 362
1 Pages
-
bottelpack® type 360
1 Pages
-
bottelpack® type 324
1 Pages
-
bottelpack® type 321
1 Pages
-
bottelpack® type 305
1 Pages