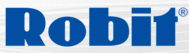
Catalog excerpts
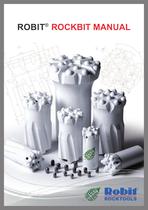
ROBIT® ROCKBIT MANUAL
Open the catalog to page 1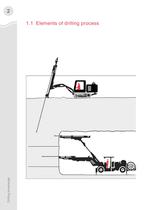
2 Drilling knowledge 1.1 Elements of drilling process
Open the catalog to page 4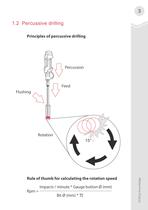
3 1.2 Percussive drilling Principles of percussive drilling Percussion Feed Flushing Rotation Rule of thumb for calculating the rotation speed Rpm = Impacts / minute * Gauge button Ø (mm) Bit Ø (mm) * Drilling knowledge 15°
Open the catalog to page 5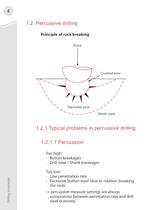
4 1.2 Percussive drilling Principle of rock breaking Force Crushed zone Fractured zone Elastic zone 1.2.1 Typical problems in percussive drilling 1.2.1.1 Percussion Drilling knowledge Too high: - Button breakages - Drill steel / Shank breakages Too low: - Low penetration rate - Excessive button wear (due to rotation breaking the rock) -> percussion measure settings are always compromise between penetration rate and drill steel economy
Open the catalog to page 6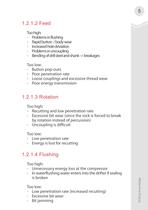
5 1.2.1.2 Feed Too high: - Problems in flushing - Rapid button / body wear - Increased hole deviation - Problems in uncoupling - Bending of drill steel and shank -> breakages Too low: - Button pop-outs - Poor penetration rate - Loose couplings and excessive thread wear - Poor energy transmission 1.2.1.3 Rotation Too high: - Recutting and low penetration rate - Excessive bit wear (since the rock is forced to break by rotation instead of percussion) - Uncoupling is difficult Too low: - Low penetration rate - Energy is lost for recutting Too high: - Unnecessary energy loss at the compressor -...
Open the catalog to page 7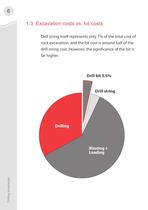
6 1.3 Excavation costs vs. bit costs Drill string itself represents only 7% of the total cost of rock excavation, and the bit cost is around half of the drill string cost. However, the significance of the bit is far higher. Drill bit 3.5% Drill string Drilling Drilling knowledge Blasting + Loading
Open the catalog to page 8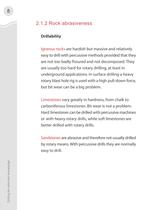
8 2.1.2 Rock abrasiveness Drillability Igneous rocks are hardish but massive and relatively easy to drill with percussive methods provided that they are not too badly fissured and not decomposed. They are usually too hard for rotary drilling, at least in underground appilcations. In surface drilling a heavy rotary blast hole rig is used with a high pull-down force, but bit wear can be a big problem. Limestones vary greatly in hardness, from chalk to carboniferous limestones. Bit wear is not a problem. Hard limestones can be drilled with percussive machines or with heavy rotary drills, while...
Open the catalog to page 10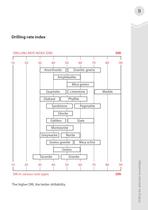
9 Drilling rate index DRI DRILLING RATE INDEX (DRI) 10 20 30 40 50 60 Anorthosite 70 80 90 Granitic gneiss Amphibolite Mica gneiss Quartzite Limestone Diabase Marble Phyllite Sandstone Pegmatite Diorite Gabbro Slate Montzonite Greywacke Norite Gneiss granite Mica schist Gneiss 10 20 30 40 Granite 50 DRI in various rock types The higher DRI, the better drillability. 60 70 80 90 DRI Drilling bit selection knowledge Taconite
Open the catalog to page 11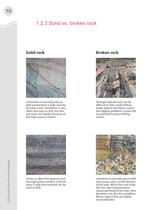
10 1.2.3 Solid vs. broken rock Broken rock Limestone is normally easy to drill; penetration is high and the bit wear is low. Sandstone is very often also easy to drill, but bits can wear out rapidly because of the high quartz content. Drilling bit selection knowledge Solid rock Strongly layered rock can be difficult to drill; small drilling angle against the layers causes the biggest problems. Correct bit is essential for good drilling results. Gneiss is often fine grained and has high quartz content, o the bit wear is high and material can be hard to drill. Limestone is normally easy to...
Open the catalog to page 12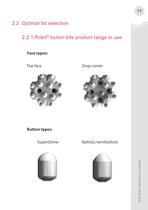
11 2.2 Optimal bit selection 2.2.1 Robit® button bits product range in use Face types: Flat face Drop center Button types: Ballistic/semiballistic Drilling bit selection knowledge SuperDome
Open the catalog to page 13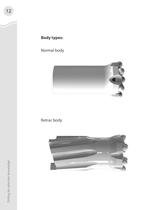
12 Body types: Normal body Drilling bit selection knowledge Retrac body
Open the catalog to page 14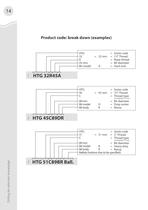
14 Product code: break down (examples) HTG 32 R 45 mm Bit model 1 A = = = = = Series code 11 4" Thread Rope thread Bit diameter Hard rock HTG 32R45A HTG 45 C 89 mm Bit model Bit body 2 = 32 mm = 45 mm = Series code = 13 4" Thread = Thread type (corresponds T, FI, etc.) D R = Bit diameter = Drop center = Retrac HTG 45C89DR HTG 51 C = 51 mm = Series code = 2" Thread = Thread type (corresponds T, FI, etc.) Drilling bit selection knowledge = Bit diameter 89 mm = Heavy duty Bit model B = Retrac Bit body R Ballistic buttons (has to be specified) 3 HTG 51C89BR Ball.
Open the catalog to page 16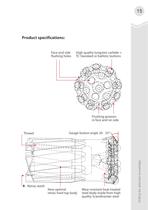
15 Product specifications: Face and side flushing holes High quality tungsten carbide = TC Standard or ballistic buttons Flushing grooves in face and on side R - Retrac teeth Gauge-button angle 30 - 35° New optimal retrac hard top body Wear resistant heat treated steel body made from high quality Scandinavian steel Drilling bit selection knowledge Thread
Open the catalog to page 17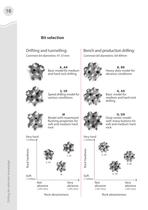
16 Bit selection Drifting and tunnelling: Bench and production drilling: Common bit diameters: 41-51mm Common bit diameters: 64-89mm A, AR Basic model for medium and hard rock drilling B, BR Heavy duty model for abrasive conditions S, SR Speed drilling model for various conditions A, AR Basic model for medium and hard rock drilling M Model with maximized flushing properties for soft and medium hard rock D, DR Drop center model with many buttons for soft and medium hard rock Very hard Very hard (>250Mpa) S, SR A, AR M Soft Rock hardness Rock hardness Drilling bit selection knowledge...
Open the catalog to page 18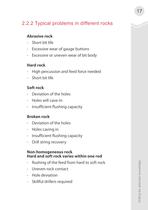
17 2.2.2 Typical problems in different rocks Abrasive rock - Short bit life - Excessive wear of gauge buttons - Excessive or uneven wear of bit body Hard rock - High percussion and feed force needed - Short bit life Soft rock - Deviation of the holes - Holes will cave-in - Insufficient flushing capacity Non-homogeneous rock Hard and soft rock varies within one rod - Rushing of the feed from hard to soft rock - Uneven rock contact - Hole deviation - Skillful drillers required Drilling bit selection knowledge Broken rock - Deviation of the holes - Holes caving in - Insufficient flushing...
Open the catalog to page 19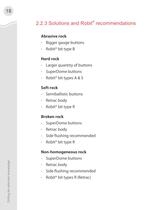
18 ® 2.2.3 Solutions and Robit recommendations Abrasive rock - Bigger gauge buttons - Robit® bit type B Hard rock - Larger quantity of buttons - SuperDome buttons - Robit® bit types A & S Soft rock - Semiballistic buttons - Retrac body - Robit® bit type R Drilling bit selection knowledge Broken rock - SuperDome buttons - Retrac body - Side flushing recommended - Robit® bit type R Non-homogeneous rock - SuperDome buttons - Retrac body - Side flushing recommended - Robit® bit types R (Retrac)
Open the catalog to page 20All Robit Rocktools catalogs and technical brochures
-
DTH-REC TECHNICAL BROCHURE
2 Pages
-
ROBIT HEAVY DUTY SERIES
2 Pages
-
Robit Drill Tubes
4 Pages
-
Robit Sense Systems
2 Pages
-
ROBIT EVOLUTION SERIES
4 Pages
-
Robit CS SERIES
2 Pages
-
Robit HTG SERIES
2 Pages
-
ROBIT® DTH PRODUCT CATALOGUE
152 Pages
-
ROBIT ®TOP HAMMER PRODUCT CATALOGUE
120 Pages
-
DTH HAMMERS
28 Pages
-
casing system
28 Pages
-
product catalogue
94 Pages
-
Casing Systems brochure
28 Pages
-
Product catalogue
44 Pages