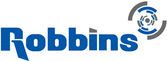

Catalog excerpts
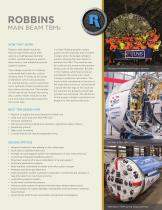
MAIN BEAM TBMs HOW THEY WORK Robbins Main Beam machines feature High Performance (HP) options including large diameter cutters, variable frequency electric drive motors, and adaptable ground support systems. Their design consists of a rotating cutterhead that holds disc cutters (ranging from 17 inches to 20 inches in diameter), which are positioned for optimal boring. As the cutterhead turns, hydraulic propel cylinders push the cutters into the rock. The transfer of this high thrust through the rolling disc cutters creates fractures in the rock and chips that break away from the tunnel face. A unique floating gripper system pushes on the sidewalls and is locked in place while the propel cylinders extend, allowing the main beam to advance the TBM. The machine can be continuously steered while gripper shoes push on the sidewalls. Buckets in the rotating cutterhead scoop up Røssåga Hydroelectric Project, Norway and deposit the muck onto a belt conveyor inside the main beam. The muck is then transferred to the rear of the machine for removal. At the end of a stroke the rear legs of the machine are lowered, the grippers and propel cylinders are retracted. The retraction of the propel cylinders repositions the gripper for the next boring cycle. Massive to slightly fractured medium to hard rock Hard rock up to and over 400 MPa UCS Abrasive conditions Non-pressurized tunneling (can operate in significant water inflows) Squeezing ground High cover tunneling Tunnels that do not require segmental lining DESIGN OPTIONS • • • • • • • • • • • • • • Abrasion-resistant wear plating on the cutterhead Roof drills to stabilize weak rock McNally Ground Support System for stabilization of very fractured rock Customized materials handling systems Ring beam erectors for quick installation of tunnel support Shotcrete application systems Back-loading cutterhead for faster and safer cutter changes Methane and other gas detectors Data acquisition system: automatic acquisition, monitoring and storage of real-time data from machine functions Automatic guidance system Cutter wear monitoring systems Advance radar system for ground monitoring to detect obstructions Special designs for rapid assembly, disassembly and movement inside the bored tunnel Grout/probe drills for pre-excavation and ground consolid
Open the catalog to page 1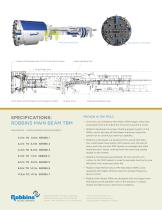
MAIN BEAM SIDE VIEW Robust Cutterhead with 17 to-20-Inch Disc Cutters MAIN BEAM CUTTERHEAD Mesh Handling Cart Roof/Probe Drill Roof Shield with McNally Ground Support System Gripper Shoe SPECIFICATIONS: ROBBINS MAIN BEAM TBM MAIN BEAM —OPEN GRIPPER DESIGN SERIES Materials Handling Crane PROVEN IN THE FIELD • Since the use of Robbins Main Beam TBMs began, they have excavated more than 2,800 km of tunnel around the world. • Robbins developed its unique floating gripper system in the 1960s, and to this day all Main Beam machines utilize the system for its continuous steering capability. •...
Open the catalog to page 2All The Robbins Company catalogs and technical brochures
-
Crossover XRE Spec Sheet
2 Pages
-
Difficult Ground Brochure
9 Pages
-
Crossover XSE
2 Pages
-
SBU-RC
2 Pages
-
DISC CUTTERS
2 Pages
-
SMALL BORING UNIT (SBU-A)
2 Pages
-
DOUBLE SHIELD TBM (SBU-DS)
2 Pages
-
SMALL BORING UNIT
2 Pages
-
AUGER BORING MACHINE (ABM)
2 Pages
-
Slurry Microtunneling [US]
2 Pages
-
Rockhead spec sheet US
2 Pages
-
SBU-A spec sheet US
2 Pages
-
ABM spec sheet US
2 Pages
-
SBU-A SPEC SHEET (METRIC
2 Pages
-
SBU Division Brochure
7 Pages
-
Robbins EPB Brochure
9 Pages
-
TBMs
9 Pages
-
ROBBINS CONVEYORS BROCHURE
9 Pages
-
ROBBIN'S PRODUCTS & SERVICES
7 Pages