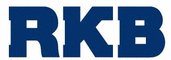

RKB Pressures Distributions and Depth Stresses Developed in Concentrated Contacts Between Elements with Non-Gaussian Rough Surfaces
1 /
8Pages
Catalog excerpts
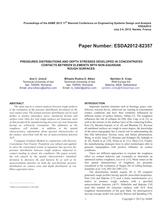
th Proceedings of the ASME 2012 11 Biennial Conference on Engineering Systems Design and Analysis ESDA2012 July 2-4, 2012, Nantes, France Paper Number: ESDA2012-82357 PRESSURES DISTRIBUTIONS AND DEPTH STRESSES DEVELOPED IN CONCENTRATED CONTACTS BETWEEN ELEMENTS WITH NON-GAUSSIAN ROUGH SURFACES * Ana C. Urzică Technical University of Iasi Iasi, 700050, Romania Email: ana.tufescu@yahoo.com Mihaela Rodica D. Bălan Technical University of Iasi Iasi, 700050, Romania Email: ro_balan@yahoo.com ABSTRACT The main step in a contact analysis between rough surfaces is the evaluation of the pressure distribution developed on the real contact area. The normal pressure distribution can be used further to predict subsurface stress, interfacial friction and surface wear. Only few real rough surfaces are Gaussian, most of that produced by manufacturing processes are non-Gaussian having an arbitrarily orientation. The definition of the roughness will include, in addition to the spatial characteristics, information about spectral characteristics of the surface, described with the use of autocorrelation function ACF. Conjugate Gradient Method in conjunction with Discrete Convolution Fast Fourier Transform was refined and applied to solve the constrained system of equations that governs the pressure distribution between rough surfaces subjected to contact loading in elastic dry conditions. The paper reveals the role played by the spatial characteristics (standard deviation σ, skewness Sk, and kurtosis K) as well as by autocorrelation function on both the non-Hertzian pressure distribution on contact area and depth distribution of von Mises equivalent stress. ___________________ *Address all correspondence to this author Spiridon S. Creţu RKB Europe SA Balerna, 6828, Switzerland spiridon.cretu@rkbbearings.com INTRODUCTION Important machine elements such as bearings, gears, camfollower, traction drives, wheel-rail are running in concentrated contact conditions and have their reliability influenced by different modes of surface failures, Tallian [1]. The roughness influences the risk of collapse for EHL film, Lugt, et al. [2], as well as the stresses in the shallow layer of the contacting bodies, Kim [3], Morales-Espejel, et al. [4] and Bhushan [5]. Because all machined surfaces are rough to some degree, the knowledge of the micro-topography has a crucial role in understanding the thin film lubrication, friction, wear, and failure phenomenon, Wang, et al.[6], Jeng [7], Bosman and Schipper [8], Sadeghi et al. [9], Paulin et al. [10], Nélias et al. [11], Zhou [12]. Finally, the manufacturing strategies have to select technologies able to generate topographies with positive influence on contact conditions. There are different approaches to examine the roughness effect on contact behavior and eventually to determine an optimized surface roughness, Liu et al. [13]. Mean values as the first spatial characteristics of roughness are presently considered in the evaluation of fatigue life of rolling bearings, Ioannides et al. [14], ISO 281:2007 [15]. The deterministic models require 2D or 3D computer generated rough profiles having specific prescribed proprieties. Patir [16] and Bakolas [17] used a linear transformation of a matrix to produce rough surfaces with a specified autocorrelation function (ACF). Mihailidis and Bakolas [18] used this method for Gaussian surfaces with ACF from roughness measurements of the gear flank. An autoregressive moving average model was used by Watson and Spedding [19]. 1 Copyright © 2012 by ASME
Open the catalog to page 1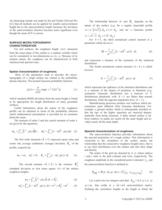
An interesting remark was made by Hu and Tonder [20] and Wu [21] that all methods can be applied for smaller autocorrelation length but as the autocorrelation length increases the deviation of the autocorrelation function becomes more significant even though the mean ACF is correct. SURFACE MICRO-TOPOGRAPHY CHARACTERIZATION For real surfaces, the roughness height z (x) measured from the mean plane of the surface is a random variable which can be considered in two-dimensions as z(x, y). Because of its random nature, the roughness can be characterized in both statistical and spectral ways....
Open the catalog to page 2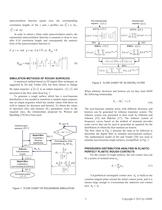
autocorrelation function equals zero, the corresponding correlation lengths of the x and y profiles are: λ0 = n ⋅ ∆x , x λ0 = m ⋅ ∆y . y In order to obtain a finite order autocorrelation matrix, the exponential autocorrelation function is assumed to drop to zero after 0.10 correlation length, and consequently the numeric form of the autocorrelation function is: if p < n and q < m; if p ≥ 0 , or, R pq = 0 1/ 2 p 2 q 2 R pq = exp− 2.3 + n − 1 m − 1 (9) SIMULATION METHODS OF ROUGH SURFACES A numerical method based on 2D digital filter technique, as suggested by Hu and Tonder [20], has been...
Open the catalog to page 3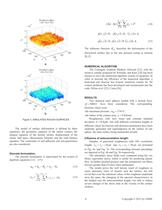
N x −1 N y −1 (∆x ⋅ ∆y ) ∑ ∑p k =0 l =0 g (x, y ) = 0, p(x, y ) > 0, ij =F (14) (x, y )∈ Ar g (x, y ) > 0, p(x, y ) = 0, (x, y )∉ Ar (15) The influence function K ij describes the deformation of the discretized surface due to the unit pressure acting in element (k, l ) . a. NUMERICAL ALGORITHM The Conjugate Gradient Method, Allwood [23], with the iterative scheme proposed by Polonsky and Keer [24] has been chosen to solve the mentioned algebraic system of equations. In order to increase the efficiency of the numerical algorithm, a dedicated real discrete fast Fourier transform routine for...
Open the catalog to page 4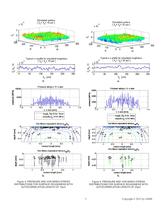
Simulated surface Simulated surface Typical x-x profile for simulated roughness Typical x-x profile far simulated roughness Pressure along x-O-x axis Von Mises equivalent stresstJ¥ti|toa Von Mises equivalent stress ovMtaQ Pressure along x-Q-x axis Von Mises equivalent stress <3vlJtsD Von Mises equivalent slresso^jg
Open the catalog to page 5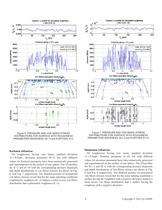
Figure 6. PRESSURE AND VON MISES STRESS DISTRIBUTIONS FOR SURFACE WITH ROUGHNESS PARAMETERS SKEWNESS Sk= 0 and KURTOSIS K=2. Figure 7. PRESSURE AND VON MISES STRESS DISTRIBUTIONS FOR SURFACE WITH ROUGHNESS PARAMETERS SKEWNESS Sk= 0 and KURTOSIS K=10. . Kurtosis influence. 3D roughnesses having zero mean, standard deviation σ = 0.4µm , skewness parameter Sk=0, but with different values for Kurtosis parameter have been numerically generated and superimposed on the surface of one sphere. The 2D profiles for K=2 and K=10 with the corresponding pressure dispersals and depth distributions of von...
Open the catalog to page 6All RKB Europe catalogs and technical brochures
-
Company Business Card - T3
1 Pages
-
Cylindrical rolelr bearings
2 Pages
-
Technological bearings
2 Pages
-
Project S12
2 Pages
-
RKB Product Table
2 Pages
-
This Is RKB
24 Pages
-
RKB Phosphate Treatment
2 Pages
-
RKB General Information Form
12 Pages
-
Project "241 KPP VL"
2 Pages
-
Project "EPB"
2 Pages
-
Project "MDU"
2 Pages
-
Project "ABI"
2 Pages
-
TQOS Maintenance
3 Pages
-
AF2D Multiroll Cage Design
2 Pages
-
RKB_Europe_SA_ISO_9001
1 Pages
-
RKB_Europe_SA_ISO_14001
1 Pages
-
RKB_Europe_SA_OHSAS_18001
1 Pages
-
RKB_Europe_SA_ISO_27001
1 Pages
-
RKB_Europe_SA_ISO_10002
1 Pages
-
RKB_Europe_SA_ISO-TS_16949
1 Pages
-
RKB General Quality Program
50 Pages
-
RKB Special Projects
68 Pages
-
RKB Metals Industry Leaflet
2 Pages
-
RKB Company Snapshot
2 Pages
-
RKB Brief Company Profile
2 Pages
-
RKB_Taper_Roller_Bearings_Assy
39 Pages
-
RKB Bearings Production Range
34 Pages
-
RKB Bearings Catalogue
168 Pages
-
RKB Taper Roller Bearings Assy
39 Pages
-
Made in RKB
1 Pages
-
RKB Basic Load Ratings
14 Pages
-
Why RKB
1 Pages
-
Bearing Industry Matrix
2 Pages
-
RKB Basic Information Form
1 Pages
-
RKB_Business_Card_T3
1 Pages
-
RKB_Business_Card_T2
1 Pages
-
RKB Message of the President
2 Pages
-
RKB Brief Introduction
2 Pages
-
RKB Digital Presentation
50 Pages
-
RKB PRODUCTION FLOW CHART
1 Pages
-
Company name and motto
6 Pages