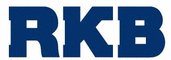

Catalog excerpts
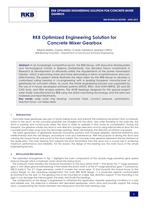
RKB OPTIMIZED ENGINEERING SOLUTION FOR CONCRETE MIXER RKB TECHNICAL REVIEW - APRIL 2012 RKB Optimized Engineering Solution for Concrete Mixer Gearbox Alberto BARILI, Ciprìan RADU, Calalin DANAI LA, Spiridon CRETU RKB Beating Industries ■ Department oí Advanced Software Engineering Abstract: in an Increasingly competitive sector, the RKB Group, with Executive Headquarters and Technological Center in Bolerna (Switzerland!, tías decided heavy investments in Reseorch & Development to efficiently satisfy the requirements of the power transmission industry, which is becoming more and more demanding in terms of performance and cost- effectiveness. The present article illustrates the steps fafcen by the RKB Group to develop a customized rolling bearing in co-engineering with a leading European manufacturer of gearboxes for concrefe mixers. As usual, the whole engineering process was supported by the use of in-house developed software systems ¡MTDS, RRLC and NON-HERTZ¡, 2D and 3D CAD tools, and EEM analysis systems. The WOR bearings designed for this special project were finally manufactured by RKB using the latest machining iechnofogy and the best raw materials and heat treatments. Key words: wide ouier ring bearing, concrete mixer, contact pressure, optimization, reaction force, von Mises sfress Concrete mixer gearboxes ore perl of transit nixing t'jeks and transmit the rotational movement from a hydraulic motor to the drum. As the concrete payloads are charged into the drum, aiso while traveling to the work site, the drum is rotating and confnuously mixes the oad in order to prepare it and avoid its consolidation. During the transport, the gearbox rotates the drum in one direction (charge direction] and by using internal helical drum tins the concrete load is kept away from the discharge opening. When discharging, the erection of rotation "s reversed. The latest generation of gearboxes features innovative solutions that increase reliability, eliminate limitations and neffecriveness from the old designs, and reduce cost; ard main"e11 eneo, '.vite ■■"e purpose of ori-.' ng the drum and carrying the torque forces and a part of the drum weight, the concrete mixer gearbox represents the key element of the application, lhe mair boeri"o rhal support; Iho loed terinilted from —e orurr hai a cucio role in achieving maximum performance and reliability. For this reason, the design of the bearing was the main focus of the whole engineering process. The exploded arrangement in Fig. 1 highlights the main components of the double stage planetary gear speed reducer through which a hydra.il c rro'or drives t"e m'xing drum. The hydraulic motor transfers the rotational movement to the input pinion shaft 1, that drives the I;l stage planetary gear 3. with deep groove ball bearing;, A Iho: re"c¡lc lhe pi-ion snef" 6 of the 2' ' s "age p anclary goor 7 sustained by SRB 8 inside it. The 2f!0 stage planetary carrier 9 couples the crown gear 10 that transmits the torque forces to the output flange 14, also absorbing misalignment. The main SRB WOR design 11 is protected against contaminated environment by the seal 1 3. The gearbox has to be mounted on a rigid, free distortion support. If the mounting is not rigid, it can damage the internal gears, the seals, and finally the bearings. The con figura ti or o: this desigr is engineered to withstand the application requisite operating conditions in a safe and reliable way. This objective is attained with described gearboxes, which drive and pivotally support the mixing CUT. ccr"ipensa"'rg -ne rr-rj-'o- ;;e"wee'" lhe mVng d'um ond the mc"n Peeing case.
Open the catalog to page 1
RKB OPTIMIZED ENGINEERING SOLUTION FOR CONCRETE MIXER GEARBOX RKB TECHNICAL REVIEW - APRIL 2012 No. 1 2 3 4 5 6 7 8 9 10 11 12 13 14 15 Component Input pinion shaft RKB deep groove ball bearing 1st stage planetary gear RKB deep groove ball bearing 1st stage planetary carrier Pinion shaft 2nd stage planetary gear RKB spherical roller bearing (SRB) 2nd stage planetary carrier Convex gear Main RKB SRB WOR design bearing Main housing Seal Output flange Rear cover Fig. 1 – Two-stage planetary gearbox explosion 3 BEARING SELECTION Due to the drum installation angle and its applied load, the main...
Open the catalog to page 2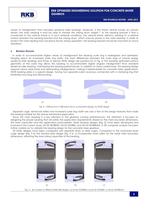
RKB OPTIMIZED ENGINEERING SOLUTION FOR CONCRETE MIXER RKB TECHNICAL REVIEW - APRIL 2012 values of misalignme-! than ; "onderei sphoriccl re er bearirgs. Moreover", il :hc transit vehicle "ravels on uneven lerrain, Ihe main bearing 4 musi be able to transfer the mixing drum weight I fo ihe bearing bracket 5 that is connected to the vehicle frame 6. In such extreme conditions, lie vehele fro no deforms, leading to a relative motion between the bearing bracket and the mixing drum, which induces shocks in the main bearing. In order to protect the main bearing from excessive shocks during...
Open the catalog to page 3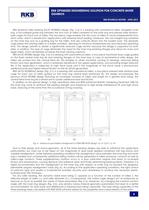
RKB OPTIMIZED ENGINEERING SOLUTION FOR CONCRETE MIXER RKB TECHNICAL REVIEW - APRIL 2012 RKB spherical re I or bocrinc 2¿ I 22 WOK S 2 A design ;>ig. 3 a) is a bearing with symmetrical rol ors. flangeless inner ring, o non-integra guide ring between the two rows ol rollers centered on the inner ring and pressed steel window- type cages for each row of rollers. The two-piece cage enables the two rows of rollers to move independently from each other, which is beneficial in applications with extreme thrust loading. Moreover, the non-integral ring centered on the inner ring acts as a guiding...
Open the catalog to page 4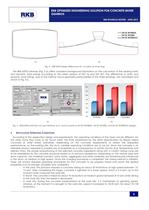
RKB OPTIMIZED ENGINEERING SOLUTION FOR CONCRETE MIXER GEARBOX RKB TECHNICAL REVIEW - APRIL 2012 24122 WOR82A 24122 WOR82 24122 WOR82AA 24122 WOR82AA a) b) Fig. 4 – SRB WOR design differences for: a) rollers; b) inner rings The RKB MTDS software (Fig. 5 a) offers consistent background information on the calculation of the bearing static and dynamic load ratings according to the latest versions of ISO 76 and ISO 281. The differences in static and dynamic load ratings, due to the internal macro-geometry particularities of the three bearings, are normalized and shown in Fig. 5 b. a) b) Fig. 5 –...
Open the catalog to page 5All RKB Europe catalogs and technical brochures
-
Company Business Card - T3
1 Pages
-
Cylindrical rolelr bearings
2 Pages
-
Technological bearings
2 Pages
-
Project S12
2 Pages
-
RKB Product Table
2 Pages
-
This Is RKB
24 Pages
-
RKB Phosphate Treatment
2 Pages
-
RKB General Information Form
12 Pages
-
Project "241 KPP VL"
2 Pages
-
Project "EPB"
2 Pages
-
Project "MDU"
2 Pages
-
Project "ABI"
2 Pages
-
TQOS Maintenance
3 Pages
-
AF2D Multiroll Cage Design
2 Pages
-
RKB_Europe_SA_ISO_9001
1 Pages
-
RKB_Europe_SA_ISO_14001
1 Pages
-
RKB_Europe_SA_OHSAS_18001
1 Pages
-
RKB_Europe_SA_ISO_27001
1 Pages
-
RKB_Europe_SA_ISO_10002
1 Pages
-
RKB_Europe_SA_ISO-TS_16949
1 Pages
-
RKB General Quality Program
50 Pages
-
RKB Special Projects
68 Pages
-
RKB Metals Industry Leaflet
2 Pages
-
RKB Company Snapshot
2 Pages
-
RKB Brief Company Profile
2 Pages
-
RKB_Taper_Roller_Bearings_Assy
39 Pages
-
RKB Bearings Production Range
34 Pages
-
RKB Bearings Catalogue
168 Pages
-
RKB Taper Roller Bearings Assy
39 Pages
-
Made in RKB
1 Pages
-
RKB Basic Load Ratings
14 Pages
-
Why RKB
1 Pages
-
Bearing Industry Matrix
2 Pages
-
RKB Basic Information Form
1 Pages
-
RKB_Business_Card_T3
1 Pages
-
RKB_Business_Card_T2
1 Pages
-
RKB Message of the President
2 Pages
-
RKB Brief Introduction
2 Pages
-
RKB Digital Presentation
50 Pages
-
RKB PRODUCTION FLOW CHART
1 Pages
-
Company name and motto
6 Pages