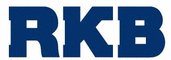

Catalog excerpts
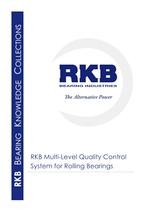
RKB BEARING KNOWLEDGE COLLECTIONS RKB Multi-Level Quality Control System for Rolling Bearings
Open the catalog to page 1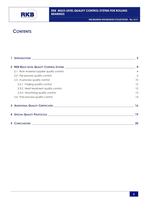
RKB MULTI-LEVEL QUALITY CONTROL SYSTEM FOR ROLLING RKB BEARING KNOWLEDGE COLLECTIONS - No. 4/11 2 RKB MULTI-LEVEL QUALITY CONTROL SYSTEM_4 2.1 Raw material supplier quality control 4 2.2 Pre-process quality control 6 2.3 In-process quality control 10 2.3.1 Forging quality control 12 2.3.2 Heat treatment quality control 12 2.3.3 Machining quality control 13 2.4 Post-process quality control 14
Open the catalog to page 2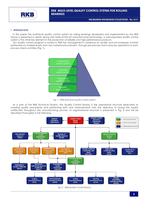
RKB MULTI-LEVEL QUALITY CONTROL SYSTEM FOR ROLLING BEARINGS RKB BEARING KNOWLEDGE COLLECTIONS - No. 4/11 3 1 INTRODUCTION In this paper the multi-level quality control system for rolling bearings developed and implemented by the RKB Group is presented in detail. Along with state-of-the-art manufacturing technology, a well-organized quality control system is the other key element in the production of reliable and high performance products. Our quality control program is rooted in RKB top management’s insistence on quality and encompasses controls performed on multiple levels, from raw...
Open the catalog to page 3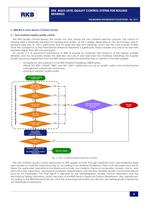
RKB MULTI-LEVEL QUALITY CONTROL SYSTEM FOR ROLLING BEARINGS RKB BEARING KNOWLEDGE COLLECTIONS - No. 4/11 4 2 RKB MULTI-LEVEL QUALITY CONTROL SYSTEM 2.1 Raw material supplier quality control The RKB Quality Control Bureau first comes into play during the raw material selection process. The choice of bearing steel is extremely important for bearing end quality, as this is largely depending on the technology used to produce steel (Fig. 3). This is particularly true for large size high-tech bearings, which are the core business of RKB, since the compliance to the international reference...
Open the catalog to page 4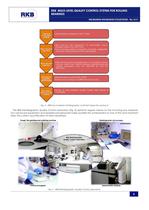
RKB MULTI-LEVEL QUALITY CONTROL SYSTEM FOR ROLLING BEARINGS RKB BEARING KNOWLEDGE COLLECTIONS - No. 4/11 5 Fig. 4 – RKB raw material metallographic multi-test inspection protocol The RKB Metallographic Quality Control Laboratory (Fig. 5) performs regular checks on the incoming raw materials. Our advanced equipment and experienced personnel make possible the achievement of one of the most important tasks: the correct quantification of steel cleanliness. Fig. 5 – RKB Metallographic Quality Control Laboratory
Open the catalog to page 5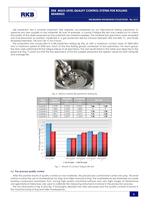
RKB MULTI-LEVEL QUALITY CONTROL SYSTEM FOR ROLLING BEARINGS RKB BEARING KNOWLEDGE COLLECTIONS - No. 4/11 6 Life prediction test is another important task regularly accomplished by our Mechanical Testing Laboratory to approve any new supplier of raw materials. By way of example, a contact fatigue life test was carried out to check the quality of the steels proposed by five potential raw material suppliers. The material test specimens were annealed and manufactured as washers, hardened in a gas protected electro-furnace between 835 and 845 „aC, and finally tempered between 150 and 160 „aC for...
Open the catalog to page 6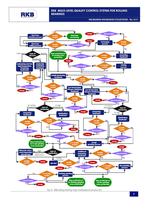
RKB MULTI-LEVEL QUALITY CONTROL SYSTEM FOR ROLLING BEARINGS RKB BEARING KNOWLEDGE COLLECTIONS - No. 4/11 7 Fig. 8 – RKB rolling bearing rings masterpieces production
Open the catalog to page 7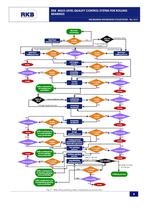
RKB MULTI-LEVEL QUALITY CONTROL SYSTEM FOR ROLLING BEARINGS RKB BEARING KNOWLEDGE COLLECTIONS - No. 4/11 8 Fig. 9 – RKB rolling bearing rollers masterpieces production
Open the catalog to page 8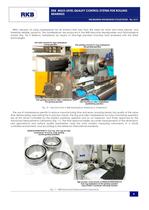
RKB MULTI-LEVEL QUALITY CONTROL SYSTEM FOR ROLLING BEARINGS RKB BEARING KNOWLEDGE COLLECTIONS - No. 4/11 9 RKB’s decision of using masterpieces for all product lines rises from the need for more and more precise, and therefore reliable, products. The masterpieces are produced in the RKB Executive Headquarters and Technological Center (Fig. 10) in Balerna, Switzerland, by means of ultra-high precision machine tools endowed with the latest technologies. Fig. 10 – Machine tools in RKB Masterpiece Workshop in Switzerland The use of masterpieces permits to reduce manufacturing time and errors,...
Open the catalog to page 9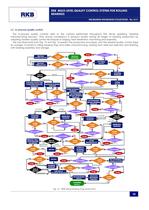
RKB MULTI-LEVEL QUALITY CONTROL SYSTEM FOR ROLLING BEARINGS RKB BEARING KNOWLEDGE COLLECTIONS - No. 4/11 10 2.3 In-process quality control The in-process quality controls refer to the controls performed throughout the strictly speaking “bearing manufacturing process”. They ensure consistency in product quality during all stages of bearing production by adopting modern quality control techniques in forging, heat treatment, machining and assembly. The two flowcharts from Fig. 12 and Fig. 13 present the production processes, and the related quality control steps (in orange), involved in...
Open the catalog to page 10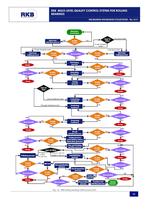
RKB MULTI-LEVEL QUALITY CONTROL SYSTEM FOR ROLLING BEARINGS RKB BEARING KNOWLEDGE COLLECTIONS - No. 4/11 11 Fig. 13 – RKB rolling bearing rollers production
Open the catalog to page 11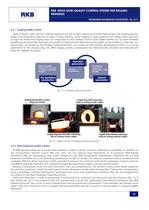
RKB MULTI-LEVEL QUALITY CONTROL SYSTEM FOR ROLLING BEARINGS RKB BEARING KNOWLEDGE COLLECTIONS - No. 4/11 12 2.3.1 Forging quality control More in depth, after the raw material approval by the Product Approval Control Department, the forging process begins, encompassing steel bar or ingot cutting, heating, upset forging or upset pressing and rolling. Every steel bar or ingot lot enters the forging area accompanied by the related Control Data Sheet emitted by our Raw Material Warehouse that specifies the type and quality of steel and the dimensions and weight of the material. In this way, our...
Open the catalog to page 12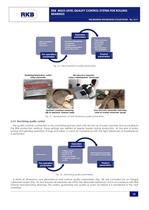
RKB MULTI-LEVEL QUALITY CONTROL SYSTEM FOR ROLLING BEARINGS RKB BEARING KNOWLEDGE COLLECTIONS - No. 4/11 13 Fig. 16 – Heat treatment quality parameters Fig. 17 – Measurement of heat treatment quality parameters 2.3.3 Machining quality control The quality controls connected to the machining process starts with the set-up of every machine tool according to the RKB production method. These settings are verified at regular breaks during production. At the end of every turning and grinding operation of rings and rollers, a check for compliance with the tight tolerances of masterpieces is...
Open the catalog to page 13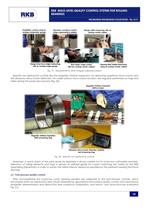
RKB MULTI-LEVEL QUALITY CONTROL SYSTEM FOR ROLLING BEARINGS RKB BEARING KNOWLEDGE COLLECTIONS - No. 4/11 14 Fig. 19 – Measurements within integral calibrated system Specific non-destructive controls like the Magnetic Particle Inspection, for detecting superficial micro-cracks, and the Ultrasonic Micro-Crack Detection, for under-surface micro-cracks location, are regularly performed on rings and rollers during the production process (Fig. 20). Fig. 20 – Specific non-destructive controls Moreover, a visual check of the parts ready for assembly is always carried out to avoid any noticeable...
Open the catalog to page 14All RKB Europe catalogs and technical brochures
-
Company Business Card - T3
1 Pages
-
Cylindrical rolelr bearings
2 Pages
-
Technological bearings
2 Pages
-
Project S12
2 Pages
-
RKB Product Table
2 Pages
-
This Is RKB
24 Pages
-
RKB Phosphate Treatment
2 Pages
-
RKB General Information Form
12 Pages
-
Project "241 KPP VL"
2 Pages
-
Project "EPB"
2 Pages
-
Project "MDU"
2 Pages
-
Project "ABI"
2 Pages
-
TQOS Maintenance
3 Pages
-
AF2D Multiroll Cage Design
2 Pages
-
RKB_Europe_SA_ISO_9001
1 Pages
-
RKB_Europe_SA_ISO_14001
1 Pages
-
RKB_Europe_SA_OHSAS_18001
1 Pages
-
RKB_Europe_SA_ISO_27001
1 Pages
-
RKB_Europe_SA_ISO_10002
1 Pages
-
RKB_Europe_SA_ISO-TS_16949
1 Pages
-
RKB General Quality Program
50 Pages
-
RKB Special Projects
68 Pages
-
RKB Metals Industry Leaflet
2 Pages
-
RKB Company Snapshot
2 Pages
-
RKB Brief Company Profile
2 Pages
-
RKB_Taper_Roller_Bearings_Assy
39 Pages
-
RKB Bearings Production Range
34 Pages
-
RKB Bearings Catalogue
168 Pages
-
RKB Taper Roller Bearings Assy
39 Pages
-
Made in RKB
1 Pages
-
RKB Basic Load Ratings
14 Pages
-
Why RKB
1 Pages
-
Bearing Industry Matrix
2 Pages
-
RKB Basic Information Form
1 Pages
-
RKB_Business_Card_T3
1 Pages
-
RKB_Business_Card_T2
1 Pages
-
RKB Message of the President
2 Pages
-
RKB Brief Introduction
2 Pages
-
RKB Digital Presentation
50 Pages
-
RKB PRODUCTION FLOW CHART
1 Pages
-
Company name and motto
6 Pages