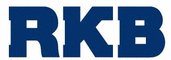

Catalog excerpts
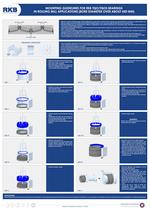
MOUNTING GUIDELINES FOR RKB TQO/TQOS BEARINGS IN ROLLING MILL APPLICATIONS (BORE DIAMETER OVER ABOUT 450 MM) DD spacer width E D BB spacer width D B E C B A C A CC spacer width PRELIMINARY OPERATIONS 1 2 a b c d 3 4 • RKB four-row taper roller bearings in TQO configuration are generally composed of two double cone assemblies (AC and CE), one central double cup (BD), two single cups (AB and DE) and three factory adjusted spacers: two cup spacers (BB and DD) and one cone spacer (CC). • RKB TQO bearings may be manufactured in different configurations: with cylindrical/tapered bore, with/without seals, with/without helical grooves on cone bores and with/without spacers. • The spacers are face ground after accurate measurements of the gaps between adjacent cups and cones to obtain the required initial axial clearance (B.E.P. - Bench End Play). • Due to the special operating conditions (contaminated environments, high temperatures, presence of vibrations and shocks), adequate lubrication is required and the use of an effective sealing system is highly recommended. • The TQOS version has seals fitted on both sides of the bearing, one cone seal set and O-type seal rings on the outer surfaces of the single cups. • The mounting of the bearing onto the roll neck has to be in accordance with the mounting instructions supplied with the rolling mill machinery design. • For bore diameters over about 450 mm, the mounting has to be performed with the bearing assembled as shown in the below procedure. • Prior to mounting, measure the chock bore diameter in four equally spaced planes normal to the bore axis of symmetry (a, b, c, d) and in each plane in four directions offset at 45° (1, 2, 3, 4). These measurements have to be properly recorded. • Carry out the same procedure for the shaft. • Bore and shaft shape deviations are highly recommended to be measured as well. • Properly lubricate bearing components according to the lubricant suggested in the rolling mill machinery design. • For easy mounting, be sure that the chock and the shaft are clean and lubricated; this will reduce the wear and corrosion of the assembly elements during operation. • Fasten the roll-side cover onto the chock. • Place the chock on level supports with bore axis in vertical position. • Place the single cup DE into the chock and check the seating of the cup against the cover shoulder with a feeler gauge. STEP I • Add the cup spacer BB, which is provided with lubrication holes. STEP VI • Add the double cone AC with side C facing down. • Handle the cone with care: do not place it on (or hang it from) the cage, but only on (or hang it from) the inner ring. • Rotate the cone to seat the rollers in proper position. • Add the cup spacer DD, which is provided with lubrication holes. • Take care not to cause nicks on the chock bore surface or burrs on the spacer. STEP II STEP VII • Insert the double cone CE with side E facing down. • Handle the cone with care: do not place it on (or hang it from) the cage, but only on (or hang it from) the inner ring. • Rotate the cone to seat the rollers in proper position. STEP III • Add the single cup AB. WARNING! All the cups need to be placed so that the marked zones are aligned. STEP VIII • Add the cone spacer CC. The cone spacer has a special design with equally spaced lubrication slots, whose purpose is to let lubricant go through the bearing to the roll neck. G STEP IV STEP IX • Insert the double cup BD. CBA STEP V • Mount the chock cover without gasket. • Tighten evenly four equally spaced cap screws, until the cover is uniformly seated against the side face of the chock, and cups and cup spacers abut each other. • Measure the width of the gap (G) between the cover and the chock and establish the gasket or metallic shim set final thickness. • Remove the cover, insert the gasket or metallic shim set of required thickness and mount the cover. STEP X • Push the labyrinth ring (heated in an oil bath) onto the roll neck. • Align the chock with the shaft. • Mount the seal neighboring the shaft shoulder and push the chock onto the roll neck with side E forward until side E of the double cone abuts the labyrinth ring. • Mount the remaining seal, spacer (A), nut (B) and split clamping ring (C) into position. • Tighten the nut until it abuts the clamping ring and the spacer abuts the bearing cone. • Loosen the nut in order to leave an appropriate axial clearance, which enables free cone rotation and prevents wear to the cone faces. DISMOUNTING If the bearing has to be dismounted for inspection and maintenance, dismounting will be performed in the reverse order of mounting. It is important to use appropriate tools and follow the above instructions and recommendations to avoid bearing damage. W W W. R K B B E A R I N G S . C O M ENGINEERED IN SWITZERLAND TECHNOLOGICAL BEARINGS
Open the catalog to page 1All RKB Europe catalogs and technical brochures
-
Company Business Card - T3
1 Pages
-
Cylindrical rolelr bearings
2 Pages
-
Technological bearings
2 Pages
-
Project S12
2 Pages
-
RKB Product Table
2 Pages
-
This Is RKB
24 Pages
-
RKB Phosphate Treatment
2 Pages
-
RKB General Information Form
12 Pages
-
Project "241 KPP VL"
2 Pages
-
Project "EPB"
2 Pages
-
Project "MDU"
2 Pages
-
Project "ABI"
2 Pages
-
TQOS Maintenance
3 Pages
-
AF2D Multiroll Cage Design
2 Pages
-
RKB_Europe_SA_ISO_9001
1 Pages
-
RKB_Europe_SA_ISO_14001
1 Pages
-
RKB_Europe_SA_OHSAS_18001
1 Pages
-
RKB_Europe_SA_ISO_27001
1 Pages
-
RKB_Europe_SA_ISO_10002
1 Pages
-
RKB_Europe_SA_ISO-TS_16949
1 Pages
-
RKB General Quality Program
50 Pages
-
RKB Special Projects
68 Pages
-
RKB Metals Industry Leaflet
2 Pages
-
RKB Company Snapshot
2 Pages
-
RKB Brief Company Profile
2 Pages
-
RKB_Taper_Roller_Bearings_Assy
39 Pages
-
RKB Bearings Production Range
34 Pages
-
RKB Bearings Catalogue
168 Pages
-
RKB Taper Roller Bearings Assy
39 Pages
-
Made in RKB
1 Pages
-
RKB Basic Load Ratings
14 Pages
-
Why RKB
1 Pages
-
Bearing Industry Matrix
2 Pages
-
RKB Basic Information Form
1 Pages
-
RKB_Business_Card_T3
1 Pages
-
RKB_Business_Card_T2
1 Pages
-
RKB Message of the President
2 Pages
-
RKB Brief Introduction
2 Pages
-
RKB Digital Presentation
50 Pages
-
RKB PRODUCTION FLOW CHART
1 Pages
-
Company name and motto
6 Pages