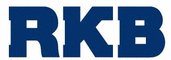

Catalog excerpts
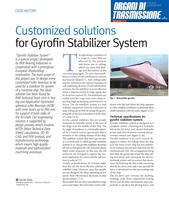
2 Organi di trasmissione - maggio 2011 CASE-HISTORY Customized solutions for Gyrofin Stabilizer System Ciprian Radu RKB Bearing Industries – Advanced Software Engineering Unit “Gyrofin Stabilizer System” is a special project developed by RKB Bearing Industries in cooperation with a prestigious European shipbuilding corporation. The main scope of this project was to design some customized roller bearings to be used for a stabilizer fin system of a maritime ship. The ideal solution has been found by RKB Technical Team Unit in two big size Application Optimized spherical roller Bearings (AOB) with inner bores up to 950 mm, for support of both sides of the fin shaft. Our engineering solution is supported by design process, which involves MTDS (Main Technical Data Sheet) calculations, 2D-3D CAD, and FEM analysis, and manufacturing technology, which means high quality materials and sophisticated machining processes. The operating economics of a cargo or cruise ship are affected by the motions and forces due to rolling, which can cause ship damage and discomfort to the crew and passengers. To solve these problems a variety of roll stabilization systems has been developed [7]. Anti-rolling tanks and fin stabilizers are typical examples of roll stabilizing devices. Of all stabilization systems, the fin stabilizer is most effective when a ship has relatively high speed, due to its active control [9]. Fin stabilizers are widely used for cargo and cruise ships requiring high seakeeping performance in waves. The fin stabilizer system is a hull stability equipment used for reduction of ship rolling up to 90% by using the generating lift of the fins extended to both sides of a ship [4; 6]. Active control stabilizer fins are usually mounted on rotatable stocks at the turn of the bilge near the middle of the ship. The fin angle of incidence is continually adjusted by a control system (gyroscope) that is sensitive to the rolling motion of the ship. The stabilizer system that uses a gyroscope, as a control unit, is called gyrofin stabilizer system [5; 2]. The gyrofin stabilizer develops lift forces that generate roll moments about ship’s center of gravity. In this way, the roll moments are arranged to oppose the moment applied by the waves and the roll motion is reduced [7]. Usually, at speeds above 10-15 knots, stabilizer fins are the most effective solution to stabilize a ship. However, since fins usually are not designed for ships operating at low speed, their effectiveness decreases as ship speed reduces [7; 3]. Retractable fins are often specified for cargo and cruise ships. The active fins can be withdrawn into the hull when the ship operates in calm weather conditions to eliminate their small resistance with the water (figure 1) [5]. Technical specifications for gyrofin stabilizer system Gyrofin stabilizer system is designed as a complete system consisting of a hydraulic driven fin, fin drive unit, electro-hydraulic power unit, electric power controls and gyroscope control unit (figure 2) [6]. Gyrofin stabilizer is an active system designed to reduce the rolling when the ship is in the water. Every ship has two stabilizer fin systems, one for port side and one for starboard side [10]. The arrangement being such that, the gyroscope senses the ship rolling movement and commands the electrohydraulic power unit to correct that movement by inclining the fins to the oncoming flow by fin drive unit, and a net upward lift force is developed on the descending side of the ship. The fin drive unit contains the shafting, bearings, seals, drive components locking device and all other mechanisms and components to produce the driving forces and Fig. 1 - Retractable gyrofin. 9 ottobre 2010
Open the catalog to page 1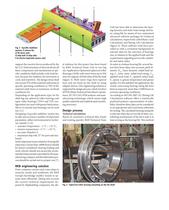
maggio 2011 - Organi di trasmissione 3 support the reactive forces produced by the fin [12]. Determination of stress levels for all these components and mechanisms at specific conditions shall include cyclic load factors, because the stabilizer fin movement is cyclic and repetitive. The design stress shall not exceed 35% of the material yield stress at specific operating conditions or 70% of the material yield stress at maximum overload conditions [6]. Depending on the application type, for fin shaft big size spherical roller bearings and taper roller bearings (TDO and TDI configuration)...
Open the catalog to page 2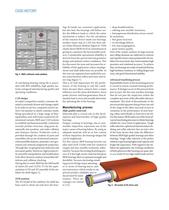
4 Organi di trasmissione - maggio 2011 CASE-HISTORY • deep desulfurization, • refi ning non-metallic inclusions, • homogeneous distribution of non-metallic inclusions, • fi ne grain structure, • no shrinkage defects, • low macrosegregation, • good surface quality. Even if the contact surfaces of rings raceway and rolling elements are subjected to extreme and repetitive heavy stress produced by the stabilizer fi n movement, they must maintain high precision and rotational accuracy. To achieve that, our bearings are made of material that has high hardness, resistance to rolling fatigue and...
Open the catalog to page 3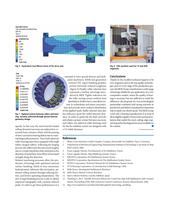
maggio 2011 - Organi di trasmissione 5 Conclusions Thanks to the excellent technical support of its own engineers and to the top quality technologies used in every stage of the production process, the RKB Group manufactures a wide range of bearings reliable for any application. In a very competitive market, where the quality of bearings is necessary but not sufficient to mark the difference, the proposal of a true technological partnership combined with strong reactivity in production and delivery has played an important role to satisfy our client’s needs. The RKB Group is not only a...
Open the catalog to page 4All RKB Europe catalogs and technical brochures
-
Company Business Card - T3
1 Pages
-
Cylindrical rolelr bearings
2 Pages
-
Technological bearings
2 Pages
-
Project S12
2 Pages
-
RKB Product Table
2 Pages
-
This Is RKB
24 Pages
-
RKB Phosphate Treatment
2 Pages
-
RKB General Information Form
12 Pages
-
Project "241 KPP VL"
2 Pages
-
Project "EPB"
2 Pages
-
Project "MDU"
2 Pages
-
Project "ABI"
2 Pages
-
TQOS Maintenance
3 Pages
-
AF2D Multiroll Cage Design
2 Pages
-
RKB_Europe_SA_ISO_9001
1 Pages
-
RKB_Europe_SA_ISO_14001
1 Pages
-
RKB_Europe_SA_OHSAS_18001
1 Pages
-
RKB_Europe_SA_ISO_27001
1 Pages
-
RKB_Europe_SA_ISO_10002
1 Pages
-
RKB_Europe_SA_ISO-TS_16949
1 Pages
-
RKB General Quality Program
50 Pages
-
RKB Special Projects
68 Pages
-
RKB Metals Industry Leaflet
2 Pages
-
RKB Company Snapshot
2 Pages
-
RKB Brief Company Profile
2 Pages
-
RKB_Taper_Roller_Bearings_Assy
39 Pages
-
RKB Bearings Production Range
34 Pages
-
RKB Bearings Catalogue
168 Pages
-
RKB Taper Roller Bearings Assy
39 Pages
-
Made in RKB
1 Pages
-
RKB Basic Load Ratings
14 Pages
-
Why RKB
1 Pages
-
Bearing Industry Matrix
2 Pages
-
RKB Basic Information Form
1 Pages
-
RKB_Business_Card_T3
1 Pages
-
RKB_Business_Card_T2
1 Pages
-
RKB Message of the President
2 Pages
-
RKB Brief Introduction
2 Pages
-
RKB Digital Presentation
50 Pages
-
RKB PRODUCTION FLOW CHART
1 Pages
-
Company name and motto
6 Pages