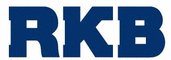

Catalog excerpts
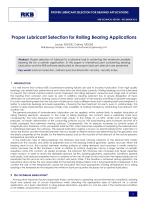
PROPER LUBRICANT SELECTION FOR BEARING APPLICATIONS RKB TECHNICAL REVIEW – DECEMBER 2013 Proper Lubricant Selection for Rolling Bearing Applications Lucian TUDOSE, Cristina TUDOSE RKB Bearing Industries – Advanced Software Engineering Unit Abstract: Proper selection of lubricant is a decisive task in achieving the maximum possible bearing life for a certain application. In this paper a theoretical part concerning bearing lubrication and the RKB software dedicated to the proper lubricant selection are presented. Key words: lubricant selection, reference/actual kinematic viscosity, viscosity index 1 INTRODUCTION It is well known that at least 60% of premature bearing failures are due to incorrect lubrication. Even high quality bearings can exhibit best performance only when they are lubricated correctly. Rolling bearings must be lubricated to prevent the harmful metal-to-metal contact between the rolling elements, raceways and cage and to protect the bearing from corrosion and wear as well. In addition, bearing lubricant has to ensure dissipation of heat, elimination of contaminants, flushing away of wear debris, lubrication of the seal lips and filling of labyrinth seal gaps. It is worth mentioning here that the function of lubricant in seals is different from that in bearing itself and therefore it is better to lubricate bearings and seals separately, choosing the best lubricant for each, even if, unfortunately, this solution is rarely implemented, because of high costs, possibility of making mistakes by substituting one lubricant with another, etc. The general principles of hydrodynamic lubrication can be applied, within certain limits, to explain lubrication of rolling bearing elements. However, in the case of rolling bearings, the contact area is extremely small and, consequently, the load pressures may reach high values, in the range of 1–3 GPa. Under such extremely high pressures, an elastic deformation of the contacting surfaces occurs, the load-bearing area increases and the oil is totally squeezed from between mating surfaces. Consequently, the oil pressure increases by several orders of magnitude and, therefore, a thin viscoelastic lubricant film, which becomes capable of supporting the external load, is maintained between the surfaces. This special lubrication regime is known as elastohydrodynamic lubrication in which the friction and film thickness between the two bodies in relative motion are determined by the geometry and the elastic properties of the bodies, by the relative speed, and by the viscosity of the lubricant at the actual pressure, temperature and rate of shear. In the particular case of rolling bearings, the thickness and load carrying capacity of the lubricant film mainly depend on the viscosity and other oil properties and on the bearing internal geometry, speed, and size. When the bearing starts to run, the contact between mating surfaces of rolling elements and raceways is mostly metal-tometal, because the oil film thickness is small, in relation to surface roughness, hence a large number of metallic asperities come into contact. As speed increases, the lubricant film thickness also increases and fewer asperities make contact. In order to reach the desirable lubricant full film, bearing geometry, application conditions (speeds and loads), and lubricant properties have to combine to form an oil layer so thick that even the highest peaks do not penetrate the film and do not come into contact with each other. If this situation is achieved during operation, the subsurface stress will be the only responsible for the bearing fatigue failure and a long bearing life is expected. In this context the role of the temperature cannot be excluded. The most appropriate working temperature for a rolling bearing is the temperature that requires the minimum lubricant quantity necessary for an optimal lubrication. 2 OIL OR GREASE LUBRICATION? Among other important factors (especially those connected to operating and environmental conditions), bearing loads and speeds are of crucial importance when selecting the appropriate type of lubricant for a certain application. As a basic orientation in using grease lubrication, equation (1) can be used. If the mentioned condition is not fulfilled, oil lubrication can be chosen.
Open the catalog to page 1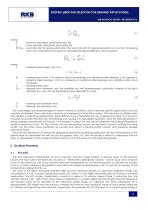
PROPER LUBRICANT SELECTION FOR BEARING APPLICATIONS RKB TECHNICAL REVIEW – DECEMBER 2013 where: P – dynamic equivalent radial/axial load, kN; C – basic dynamic radial/axial load rating, kN; (P/C)lim – load ratio limit for grease lubrication. The load ratio limit for grease lubrication is a function of bearing type, size, and speed and is given by the following approximate but useful equation: (2) – adjusted speed index, mm· min-1: (3) – bearing type factor (1 for radial or thrust ball bearings and cylindrical roller bearings, 2 for tapered or spherical roller bearings, 3 for full complement...
Open the catalog to page 2
PROPER LUBRICANT SELECTION FOR BEARING APPLICATIONS RKB TECHNICAL REVIEW – DECEMBER 2013 220 mm2/s ± 10% (at 40 °C). The ISO system is also adopted by ASTM standards [5] and since the American Gear Manufacturers Association (AGMA) has issued [3] own specifications for gear lubricants used in various types of gear application, Table 1 contains the ISO-AGMA grade equivalence also. Table 1 – ISO classification of industrial oils and AGMA/ANSI equivalence ISO 3448:1992 Viscosity Grade It is important to know that the oil kinematic viscosity decreases substantially with temperature and the...
Open the catalog to page 3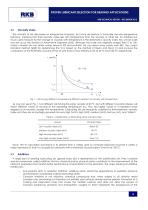
PROPER LUBRICANT SELECTION FOR BEARING APPLICATIONS RKB TECHNICAL REVIEW – DECEMBER 2013 Viscosity Index The viscosity of oils decreases as temperature increases, but some oils feature a favorable viscosity-temperature behavior, meaning that their viscosity varies less with temperature than the viscosity of other oils. An arbitrary but much used measure for the change of viscosity with temperature is the (kinematic) viscosity index (VI), whose scale was set up by the Society of Automotive Engineers (SAE). Although this scale was originally ranged from 0 to 100, today’s mineral oils can...
Open the catalog to page 4All RKB Europe catalogs and technical brochures
-
Company Business Card - T3
1 Pages
-
Cylindrical rolelr bearings
2 Pages
-
Technological bearings
2 Pages
-
Project S12
2 Pages
-
RKB Product Table
2 Pages
-
This Is RKB
24 Pages
-
RKB Phosphate Treatment
2 Pages
-
RKB General Information Form
12 Pages
-
Project "241 KPP VL"
2 Pages
-
Project "EPB"
2 Pages
-
Project "MDU"
2 Pages
-
Project "ABI"
2 Pages
-
TQOS Maintenance
3 Pages
-
AF2D Multiroll Cage Design
2 Pages
-
RKB_Europe_SA_ISO_9001
1 Pages
-
RKB_Europe_SA_ISO_14001
1 Pages
-
RKB_Europe_SA_OHSAS_18001
1 Pages
-
RKB_Europe_SA_ISO_27001
1 Pages
-
RKB_Europe_SA_ISO_10002
1 Pages
-
RKB_Europe_SA_ISO-TS_16949
1 Pages
-
RKB General Quality Program
50 Pages
-
RKB Special Projects
68 Pages
-
RKB Metals Industry Leaflet
2 Pages
-
RKB Company Snapshot
2 Pages
-
RKB Brief Company Profile
2 Pages
-
RKB_Taper_Roller_Bearings_Assy
39 Pages
-
RKB Bearings Production Range
34 Pages
-
RKB Bearings Catalogue
168 Pages
-
RKB Taper Roller Bearings Assy
39 Pages
-
Made in RKB
1 Pages
-
RKB Basic Load Ratings
14 Pages
-
Why RKB
1 Pages
-
Bearing Industry Matrix
2 Pages
-
RKB Basic Information Form
1 Pages
-
RKB_Business_Card_T3
1 Pages
-
RKB_Business_Card_T2
1 Pages
-
RKB Message of the President
2 Pages
-
RKB Brief Introduction
2 Pages
-
RKB Digital Presentation
50 Pages
-
RKB PRODUCTION FLOW CHART
1 Pages
-
Company name and motto
6 Pages