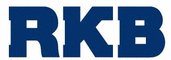

Catalog excerpts
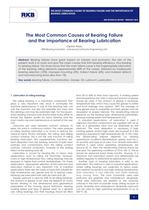
THE MOST COMMON CAUSES OF BEARING FAILURE AND THE IMPORTANCE OF BEARING LUBRICATION RKB TECHNICAL REVIEW - FEBRUARY 2010 1 The Most Common Causes of Bearing Failure and the Importance of Bearing Lubrication Ciprian Radu RKB Bearing Industries - Advanced Software Engineering Unit Abstract: Bearing failures have great impact on industry and economy. The aim of the present work is to study and spot the major causes that limit bearing efficiency, thus leading to bearing failure. This study shows that the main failure cause is the inappropriate lubrication of the bearing rolling elements (approximately 80% of the cases), followed by inadequate bearing selection (10%), improper mounting (5%), indirect failure (4%), and material defects and manufacturing errors (less than 1%). Key words: Bearing failure, Contamination, Grease, Oil, Lubricant, Lubrication 1. Lubrication of rolling bearings The rolling bearing is a machinery component that plays a very important role, since it dominates the machine performance. If one of the bearings fails, not only the machine, but also the assembly line stops and the deriving costs may be extremely high. For this reason, every bearing manufacturer should make every effort to ensure the highest quality for each bearing and the most careful use and maintenance on behalf of the user [10]. Lubricants are used between contact surfaces to keep the parts in continuous motion. The main purpose of rolling bearing lubrication is to avoid or reduce the metal-to-metal friction between the rolling and sliding contact surfaces. This is not the only function of rolling bearing lubrication. The supplementary functions are: heat dissipation from the bearing, removal of solid wear particles and contaminants from the rolling contact surfaces, corrosion protection, increase of the sealing effect of the bearing seals [4]. Lubrication is crucial for bearing life. In heavy duty applications, such as rolling mill machines, furnaces, ovens or high temperature fans, rolling bearings may be exposed to higher-than-normal temperatures. For these applications, appropriate selection of the lubricant and lubrication method is very important [13]. In industrial applications there are two types of lubricants suitable for high temperature use: grease and oil. In special cases, bearings are lubricated with solid dry lubricants [4]. Grease lubricant is used for 90% of all rolling bearings. The amount of grease to be used will depend on many factors relating to the dimensional and geometrical parameters of the housing, space limitations, bearing working speed and type of grease used. As a general rule, rolling bearings and their housings should be filled from 30 to 60% of their total capacity. If working speed and temperature rise, then a reduced amount of grease should be used. If the amount of grease is excessive, temperature rises, which may cause the grease to soften and local leakage may appear. With the passage of time grease loses its properties and fresh grease must be resupplied at proper intervals. The relubricating interval depends on the bearing type, dimensional parameters, bearing working speed and temperature [10]. In industrial applications, oil lubrication is used if adjacent machine components are supplied with oil as well, or if generated heat must be dissipated by the lubricant. The heat dissipation is necessary if high rotating speeds and/or high loads are involved or if the bearing is exposed to high temperatures [4]. In this case, the relubricating interval depends on bearing operational conditions (temperature, speed, load etc.), oil quantity and type of oil used. If an oil bath lubrication method is used when operating temperatures are around 50 „aC, then the relubricating interval should be one year. For operating conditions of 70 to 100 „aC, the oil should be replaced every three months. Anyway, it is important that lubrication system and deterioration be verified regularly to determine oil replacement [10]. Another type of bearing lubrication is solid or dry lubrication. This method is used in industrial applications, where rolling bearings are subjected to heavy loads, slow relative movements and high working temperature. Solid lubrication is very effective and yields relatively long running times. The most commonly used solid lubricants are graphite and molybdenum disulphide. These solid lubricants are applied to the raceway surfaces in the form of powder loose, sliding lacquer or paste. Graphite and molybdenum disulphide lubricants can be used for high operating temperatures of up to 450 °C [4].
Open the catalog to page 1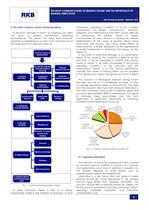
THE MOST COMMON CAUSES OF BEARING FAILURE AND THE IMPORTANCE OF BEARING LUBRICATION RKB TECHNICAL REVIEW - FEBRUARY 2010 2 Fig. 1 - Common bearing failure causes 2. The most common causes of bearing failure In practice, damage or failure of a bearing are often the result of several mechanisms operating simultaneously. The failure can result from improper assembly or maintenance or from faulty manufacture of the bearing or of its adjacent parts [3]. In some instances, failure is due to a design compromise made in the interests of economy or from unforeseen operating conditions. It is the...
Open the catalog to page 2
THE MOST COMMON CAUSES OF BEARING FAILURE AND THE IMPORTANCE OF BEARING LUBRICATION RKB TECHNICAL REVIEW - FEBRUARY 2010 3 Fig. 5 - Required kinematic viscosity, ƒÞ, at reference temperature Fig. 4 - Reference kinematic viscosity, ƒÞ1, at reference bearing speed and pitch diameter Fig. 3 - Abrasive wear on the outer ring raceway The excessively long time lubrication without renewing and unsuitable lubrication of rolling bearings represent a large percentage of premature bearing failures (approximately 20% each), and in most cases they can be prevented [9]. Unsuitable lubricant is a...
Open the catalog to page 3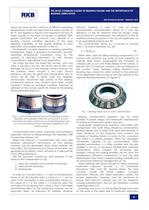
THE MOST COMMON CAUSES OF BEARING FAILURE AND THE IMPORTANCE OF BEARING LUBRICATION RKB TECHNICAL REVIEW - FEBRUARY 2010 4 Fig. 7 - Bearing failure due to water contamination a) b) Fig. 6 - a) The frosted appearance of this bearing raceway illustrates what happens when the oil viscosity is too low and metal-to-metal contact occurs. b) Bearing failure due to continual welding contact between asperities on the metal surfaces about the same oil film is built up at different operating temperatures if both oil types have the same viscosity at 40 °C. The diagram in figure 4 and equations (2) and...
Open the catalog to page 4All RKB Europe catalogs and technical brochures
-
Company Business Card - T3
1 Pages
-
Cylindrical rolelr bearings
2 Pages
-
Technological bearings
2 Pages
-
Project S12
2 Pages
-
RKB Product Table
2 Pages
-
This Is RKB
24 Pages
-
RKB Phosphate Treatment
2 Pages
-
RKB General Information Form
12 Pages
-
Project "241 KPP VL"
2 Pages
-
Project "EPB"
2 Pages
-
Project "MDU"
2 Pages
-
Project "ABI"
2 Pages
-
TQOS Maintenance
3 Pages
-
AF2D Multiroll Cage Design
2 Pages
-
RKB_Europe_SA_ISO_9001
1 Pages
-
RKB_Europe_SA_ISO_14001
1 Pages
-
RKB_Europe_SA_OHSAS_18001
1 Pages
-
RKB_Europe_SA_ISO_27001
1 Pages
-
RKB_Europe_SA_ISO_10002
1 Pages
-
RKB_Europe_SA_ISO-TS_16949
1 Pages
-
RKB General Quality Program
50 Pages
-
RKB Special Projects
68 Pages
-
RKB Metals Industry Leaflet
2 Pages
-
RKB Company Snapshot
2 Pages
-
RKB Brief Company Profile
2 Pages
-
RKB_Taper_Roller_Bearings_Assy
39 Pages
-
RKB Bearings Production Range
34 Pages
-
RKB Bearings Catalogue
168 Pages
-
RKB Taper Roller Bearings Assy
39 Pages
-
Made in RKB
1 Pages
-
RKB Basic Load Ratings
14 Pages
-
Why RKB
1 Pages
-
Bearing Industry Matrix
2 Pages
-
RKB Basic Information Form
1 Pages
-
RKB_Business_Card_T3
1 Pages
-
RKB_Business_Card_T2
1 Pages
-
RKB Message of the President
2 Pages
-
RKB Brief Introduction
2 Pages
-
RKB Digital Presentation
50 Pages
-
RKB PRODUCTION FLOW CHART
1 Pages
-
Company name and motto
6 Pages