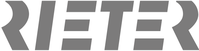
Catalog excerpts
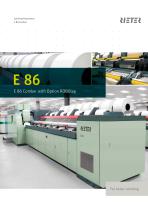
Spinning Preparation E 86 Comber E 86 Comber with Option ROBOlap OUTSTANDING FEATURES TECHNICAL DATA
Open the catalog to page 1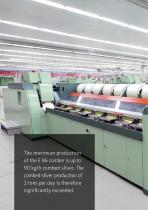
The maximum production of the E 86 comber is up to 90 kg/h combed sliver. The combed sliver production of 2 tons per day is therefore significantly exceeded.
Open the catalog to page 2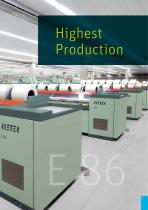
Highest Production
Open the catalog to page 3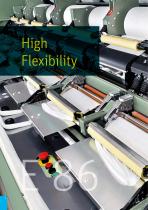
High Flexibility
Open the catalog to page 4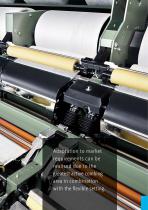
Adaptation to market requirements can be realised due to the greatest active combing area in combination with the flexible setting
Open the catalog to page 5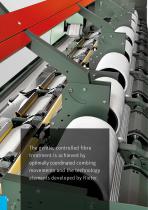
The gentle, controlled fibre treatment is achieved by optimally coordinated combing movements and the technology elements developed by Rieter.
Open the catalog to page 6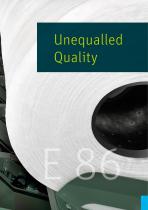
Unequalled Quality
Open the catalog to page 7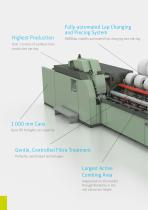
Highest Production Fully-automated Lap Changing and Piecing System ROBOlap enables automated lap changing and piecing Over 2 tonnes of combed sliver production per day 1 000 mm Cans Up to 90 % higher can capacity Gentle, Controlled Fibre Treatment Perfectly coordinated technologies Largest Active Combing Area Adaptations to the market through flexibility in the noil extraction height 8
Open the catalog to page 8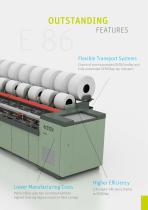
Flexible Transport Systems Choice of semi-automated SERVOtrolley and fully-automated SERVOlap lap transport Perfect fibre selection combined with the to ROBOlap highest clearing degree results in fibre savings
Open the catalog to page 9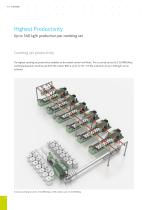
Highest Productivity Up to 540 kg/h production per combing set Combing set productivity The highest combing set productivity available on the market comes from Rieter. This is carried out by the E 36 OMEGAlap combing preparation machine and the E 86 comber. With a set of 1 E 36 + 6 E 86, production of up to 540 kg/h can be achieved. Economic combing set with 1 E 36 OMEGAlap, 6 E 86 combers and 1 E 26 SERVOlap
Open the catalog to page 10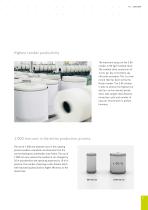
Highest comber productivity The maximum output of the E 86 comber is 90 kg/h combed sliver. The combed sliver production of 2 tons per day is therefore significantly exceeded. This is a new record that has been set by the Rieter comber. The E 86 comber is able to achieve the highest production, as the relevant parameters, batt weight, feed distance moved per cycle and number of nips per minute work in perfect harmony. 1 000 mm cans in the entire production process The use of 1 000 mm diameter cans in the combing process enables a standard can dimension from the card to feeding the...
Open the catalog to page 11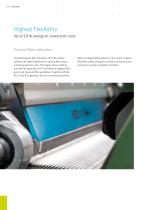
Highest Flexibility Up to 10 % saving on conversion costs Optimal fibre utilisation Oriented towards fibre utilisation, the E 86 comber achieves the highest demands for optimal fibre output and low production costs. The largest active combing area with an expansion of 45 % enables the highest fibre purity and improved fibre parallelism. Together with the Ri-Q-Comb Flex geometry this has an extremely positive effect on targeted fibre selection. This results in higher flexibility in fibre utilisation, as well as being more economical in use than competitor machines.
Open the catalog to page 12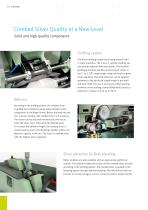
Combed Sliver Quality at a New Level Solid and high-quality components Drafting system The Rieter drafting system has already proved itself in many machines. The 3-over-3 cylinder drafting system enables optimal draft distribution. Precise fibre guiding guarantees faultless processing of cotton in the 1" to 1 7/8" staple length range and leads to good sliver regularity. The draft distances can be adapted optimally to the particular staple length in pre-draft and main draft. The use of new types of fibre guiding elements in the drafting system (AIRshields) causes a reduction in clearer cuts...
Open the catalog to page 14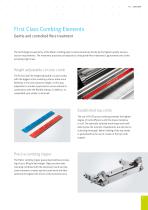
First Class Combing Elements Gentle and controlled fibre treatment The technological superiority of the Rieter combing plant is demonstrated primarily by the highest quality and production requirements. The movement processes are adjusted so that gentle fibre treatment is guaranteed even under extremely high stress. Height-adjustable circular comb The Ri-Q-Comb Flex height-adjustable circular combs with the biggest active combing surfaces allow more flexibility in the noil extraction height. In this way, adaptation to market requirements can be realised in combination with the flexible...
Open the catalog to page 15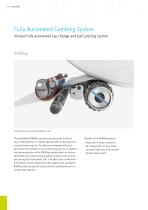
Fully Automated Combing System Unique fully automated lap change and batt piecing system Automated batt piecing by the ROBOlap system The established ROBOlap system is already on the market in over 3 000 machines. It enables operator effort to be reduced to a purely monitoring role. The efficiency compared with semiautomated E 86 combers is increased by around 2 %. In addition, the piecing operation of the ROBOlap system leads to a measurably better and constant piecing quality compared with manual batt piecing (see illustration). This is an effect that is reflected in the evenness of the...
Open the catalog to page 16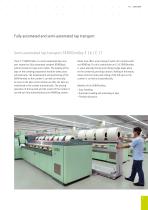
Fully automated and semi-automated lap transport Semi-automated lap transport SERVOtrolley E 16 / E 17 The E 17 SERVOtrolley is a semi-automated lap transport system for fully automated combers (ROBOlap), which transports 4 laps and 4 tubes. The loading of the laps on the combing preparation machine takes place automatically. The displacement and positioning of the SERVOtrolley on the comber is carried out manually. As soon as the laps on the comber are idle, the laps are transferred to the comber automatically. The piecing operation of the lap batt and the restart of the comber is carried...
Open the catalog to page 17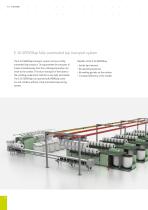
E 26 SERVOlap fully automated lap transport system The E 26 SERVOlap transport system carries out fully automated lap transport. This guarantees the transport of 8 laps simultaneously from the combing preparation machine to the comber. The return transport of the tubes to the combing preparation machine is also fully automated. The E 26 SERVOlap can operate both ROBOlap combers and combers without a fully automated lap piecing system. Benefits of the E 26 SERVOlap: • Gentle lap transport • No operating expenses • No waiting periods on the comber • Increased efficiency of the c
Open the catalog to page 18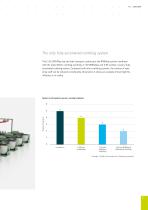
The only fully automated combing system The E 26 SERVOlap lap and tube transport system plus the ROBOlap system combined with the latest Rieter combing machines, E 36 OMEGAlap and E 86 comber, create a fully automated combing system. Compared with other combing systems, the number of operating staff can be reduced considerably. Illustration 4 shows an example of how high this influence is in reality. Number of staff needed to operate a combing installation 6 E 86 with ROBOlap & OMEGAlap E 86 with ROBOlap & OMEGAlap & SERVOlap *Example: 76 000 K 46 spindles and 1 348 kg/h production
Open the catalog to page 19All RIETER catalogs and technical brochures
-
Compact-Spinning Machine K 48
32 Pages
-
Ring Spinning Machine G 38
8 Pages
-
Rieter Draw Frames
36 Pages
-
2023 VARIOline
58 Pages
-
E 90
20 Pages
-
Rotor Spinning Machine R 37
28 Pages
-
Rotor spinning machine R 70
12 Pages
-
Air-jet spinning machine J 70
20 Pages
-
High-performance card C 81
28 Pages
-
Performance card C 77
28 Pages
-
G 38
28 Pages
-
SUESSEN Premium Parts
120 Pages
-
SB-D 26
28 Pages
-
RSB-D 26
28 Pages
-
C 80
8 Pages
-
C 75
32 Pages
-
ESSENTIAL
8 Pages
-
Alok Industries Limited
12 Pages
-
Allianz
8 Pages
-
Accessories by Rieter
6 Pages
-
R 66
32 Pages
-
SERVOtrail
28 Pages
-
RSB D 24
32 Pages
-
G 36
28 Pages
-
R 36
2 Pages
-
Double-Head Draw Frame SB-D 22
24 Pages
-
A 12 UNIfloc
2 Pages
-
SPIDERWEB
24 Pages
-
ECOrized
2 Pages
-
K 46 Compact Spinning Machine
28 Pages
-
K 42 Compact Spinning Machine
28 Pages
-
C 70 High-Performance Card
32 Pages
Archived catalogs
-
SERVOtrail
2 Pages
-
2016 VARIOline
64 Pages